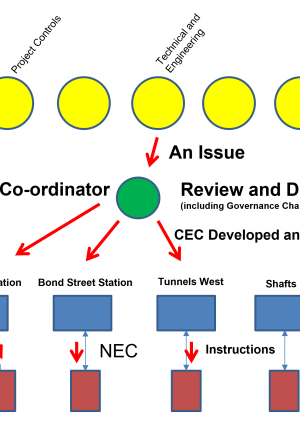
Central Communications (CEC) – Improving Formal Communications on a Major Programme
Document
type: Micro-report
Author:
Mike Adkin BEng CEng MICE
Publication
Date: 18/05/2023
-
Abstract
A key challenge to a major programme is establishing a mechanism to efficiently communicate information from the centre, down to multiple site teams and into the supply chain. This paper explains how the contract management system was developed to incorporate directions to site times (“CECs”). The CEC process was integral to ensuring the safe and efficient integration of the railway, particularly through the programme’s later stages, including COVID recovery and railway commissioning.
-
Read the full document
Introduction and Industry Context
Crossrail was one of the largest construction projects of the early 21st century. The delivery phase lasted 14 years (2009 to 2023) and comprised around 200 separate design and works contracts of which 30 were termed major contracts with values of typically £50m plus.
This paper sets out the background to the development and implementation of the programme’s Central Communication process (known as “CEC”). The CEC process proved invaluable in directing disparately spread teams on matters such as:
- the adoption of processes for access/egress along the line of route with multiple interfacing Principal Contractors;
- The processes for ensuring safety with the progressive energisation of the overhead line electrification through the tunnels;
- Safely and efficiently stopping works and progressively opening up works within the COVID pandemic period;
Main Story
A key challenge to the programme was working out how to flow down efficiently and effectively directions into the 20+ site teams and then down as instructions, communications or early warnings to the 30+ main tier 1 contractors.
Following procurement, significant effort had already been invested in a fully integrated document management system (eB) and contract administration system (eBCA). As such the programme benefited from a consistent approach both geographically and by discipline. By 2013, all main tier 1 contracts and site teams were using this common platform.
As contracts progressed, it became apparent that a further “instruction/direction” layer was required between the central function teams/departments and the site teams for common issues (issues affecting some or all sites). The figure below illustrates the wide range of issues prompting such instructions or directions.
Figure 1. Drivers for Central Communications
By the early stages of construction works, several Crossrail directorates (Technical, Delivery, Commercial) had developed their own, largely paper/email-based mechanisms for trying to get directions passed down to site teams and on to contractors. These methods depended upon spreadsheets or Sharepoint trackers and manually time intensive reminders outside the eB system. Reporting to ascertain that such directions had been delivered and appropriately actioned were difficult to demonstrate. Follow up, or supplementary directions became increasingly complicated to administer by such manual means.
It became clear that a more sophisticated communication mechanism was required. Thus, an additional layer of “instruction” or “direction” was added into the project’s eB/eBCA management system. The CEC (CEntral Communication) was thus developed, with the Commercial directorate taking overall ownership. The idea was relatively simple, a work-flow process co-ordinated at the programme centre, prepared a multi-site internal instruction. This instruction explained the nature of the issue, cross referenced the governance obtained (technical, financial etc), provided the draft wording for the Project Manager’s instruction and included necessary linked documents and or earlier related communications all within the eB system. An example is illustrated below:
Figure 2. CEC structure
The CEC process established both a tool and process under the direction of a “CEC co-ordinator” from the commercial department. As illustrated below, the co-ordinator played a role similar to an American football quarterback. An issue was picked up, triaged, and consulted upon. The co-ordinator sought consensus on resolution of the issue, working with change and technical assurance panels for approval as necessary. The co-ordinator crafted the wording of the CEC and pulled together associated supporting documents and or reference to earlier CECs.
Figure 3. The CEC process
In a similar way to contract communications, the CEC passed through a work-flow sign off with relevant consultees. Once the wording had been agreed, the CEC was executed and auto email distributed to the key persons associated within each site team selected (Project Manager, Supervisor, Contract Administrator etc).
Once the email was received by the site, each local team reviewed the CEC directions and would then launch the start of a linked instruction, early warning, or communication to their contractor(s) using menu button options on the CEC tool. This function automatically created the draft contractor communication into a standard template and copying base CEC information.
Figure 4. Site team actions
Once a CEC had been issued, the CEC co-ordinator could track in real time, the progress by which site teams were actioning their CECs. Such reports were used to measure the performance of site teams by days taken to complete. Site teams could similarly view their site-specific CEC directions as a source of truth as illustrated below:
Figure 5. CEC status report by contract
Further reports were developed which were able to present related correspondence from the contractors. Thus, it was possible to collect Implemented Compensation Events for common multi-site issues.
As the project progressed into the testing and commissioning phases, so the tool was enhanced to include infrastructure maintainers and concession teams for rolling stock and operators.
The CEC was pivotal in ensuring both a standard approach and establishing programme wide discipline (avoiding ad hoc directions). The CEC provided quickly demonstrable audit records of actions linking leadership decisions to site actions. Site teams, in a similar way to contractors, could thus insist on being formally directed from the centre via a CEC.
However, the key objective was for the programme to be able to readily confirm that all sites had carried out their actions consistently and in a timely fashion. Thus, it was possible for example to establish within less than 24 hours that all Crossrail construction contractors had been instructed to initiate the COVID safe-stop directions as directed by the Crossrail leadership.
Lessons learned
The CEC process issued around 800 instructions to site teams, spawning around 13,000 downstream communications.
The CEC tool really proved its worth during the later stages of the programme when integration between the sites became critical for issues such as energisation of the overhead electrification or the railway entering into operation under the Railways and Other Guided Systems Regulations. At these key stages it was essential that the central team could be assured that each site team had implemented their CEC directions promptly and in a consistent manner.
The success of the CEC process depended greatly upon the CEC co-ordinator’s skill and experience. The position required a unique blend of engineering and commercial knowledge coupled with a knowledge of how to develop and manage work-flows, and information management systems. The CEC tool was progressively honed as the programme developed but its success depended largely on the continuity of the CEC co-ordinator, with their embedded knowledge of the programme history, contract works information, contracts and project teams.
Recommendations for Future Projects
The CEC system described above does not seek to solve every situation but was tailored for dealing simply and effectively with most internal formal communication requirements. During the later stages, the tool was developed further to include communication directives to other industry stakeholders (e.g. maintainers, operators and concession managers).
The key recommendations for major programmes are:
- Properly think through at an early stage, how decisions are to flow down into the site teams and supply chains. This task is a pan-programme wide activity and thus requires careful consideration. It often falls between the cracks in an organisation.
- To be effective, the flow down process needs to be integral to the programme’s document management system. Larger programmes often have greater time and resources to enable the processes to be configured and honed. Any process will depend upon how good the underlying document management system is and how well this has been implemented.
- The selection of the CEC co-ordinator is critical. This needs to be someone with all-round programme management experience, together with an interest in the tools and the aptitude to get involved in the detail of development and implementation. Much of the success of the Crossrail CEC tool was down to the word smithing of the instructions, and from having consulted appropriately and proportionately. The position requires continuity in post as it depends upon accumulated knowledge, and the establishment of a rapport with the key members of departments and site teams.
- A further key part of the CEC process is the ongoing publicity to new senior level staff joining the programme, so as to explain the benefits, and the expectations for their and their team’s compliance.
-
Authors
Mike Adkin BEng CEng MICE - Jacobs
Mike Adkin is a chartered civil engineer with over twenty years experience on major UK rail programmes including HS1, HS2 and fourteen years on Crossrail. He held roles as head of contract management on Crossrail (2009 to 2010) and HS2 (2012 to 2013).
His specific area of interest is the development of tools and processes to both inform strategic and tactical decision making, and to manage the flows of information up and down the supply chain on mega infrastructure programmes. Between 2011 and 2013, the author adopted systems developed at Crossrail, to successfully support the start of the HS2 programme.