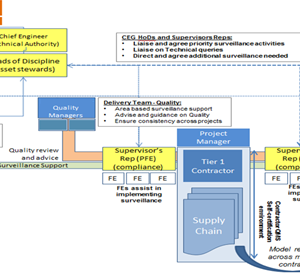
Technical Surveillance – lessons learned
Document
type: Micro-report
Author:
Kerli Saarnik MCQI
Publication
Date: 18/05/2023
-
Abstract
This report provides the Crossrail technical surveillance methodology that can be adopted on future projects of this nature. The surveillance process is important as it provides an independent check of on-going works, risk-based sampling of works to ensure its conformance to the works information and relevant specifications and standards.
Summary of lessons learned:
- Surveillances to be based on the project’s weekly look ahead programme as work activities constantly change from the main project schedule.
- In addition to the seven day notification, the surveillance procedure should also make allowances for visiting site with little or no notification.
-
Read the full document
Introduction
The Technical Surveillance[1] process was developed to perform independent risk-based quality surveillance through sampling to check that the Contractor’s detailed design or samples of completed work, or work under construction, installation, testing and commissioning was compliant with processes, drawings, specifications and standards defined by the contract Works Information and Crossrail requirements.
Implementation of Technical Surveillance across the programme was supported by Crossrail’s 3 Lines of Defence Integrated Assurance Framework (3LoD IAF) that provided integrity and compliance for programme delivery.
Figure 1 – 3 Lines of Defence Model
Each line of defence is independent, incrementally building assurance evidence of programme maturity.
The framework was originally approved by Crossrail on 28 February 2019. This was amended in November 2021 following changes to the corporate governance, bringing Crossrail under TfL governance arrangements. The framework is illustrated in Figure 1 above and comprises the following elements:
- First Line (LoD 1) – Programme Delivery Controls covering both Crossrail and Rail for London (Elizabeth line) organisations. These functions are embedded into day-to-day management of the organisations each overseen by the relevant Director.
- Second Line (LoD 2) – Project and Programme Assurance (PPA) coordinates and integrates across all of Crossrail’s and RfL (EL) assurance using a risk-based approach to assess and report on confidence in delivery, adequacy of assurance and potential threats (risks) to objectives. This includes the Technical Surveillance Process.
- Third Line (LoD 3) – TfL Internal Audit and a subgroup of the Independent Investment Programme Advisory Group (IIPAG) provide an independent assessment of the overarching integrity and performance of Crossrail’s 3LoD IAF conducting independent risk-based internal audits and reviews as necessary.
Works Information Part 20 Quality Management, Section 20.2 General Requirements; “The Employer, the Project Manager, the Supervisor and any third parties authorised by the Project Manager, including LUL, NR, DLR, TfL, statutory authorities and statutory undertakers, shall have the right to conduct audits, inspections and tests of any part of the works that are being executed in connection with their assets by the Contractor and to observe the execution of these activities”.
Technical Surveillance process
Surveillances undertaken by Crossrail were generally carried out on permanent works for Tier 1 Contractors and their supply chain. Temporary works, demolition works and utility works were only checked if requested or if a particular concern was identified. The Quality Team was independent of delivery and carried out surveillances as required on specific areas where a risk was highlighted. Technical surveillance did not certify the work, this remained the responsibility of the organisation (Tier 1) as defined by the contract. Wherever possible and practical (and to avoid duplication) collaborative surveillances were undertaken jointly with the Contractor.
A risk-based programme was devised in liaison with SRs, CEG and other stakeholders (IMs etc). This was updated every four weeks and issued.
Figure 2 – Crossrail Quality Surveillance model
Surveillances were based on the following:
- perceived risk of activities in collaboration with the Supervisor Rep
- contractor programmes
- technical complexity of a particular activity
- risk register information
- current trends of NCRs
- Quality Performance Index (QPI) scoring trends
- QPI – League table of contractor’s performance measuring following: starting works without accepted ITP, Code 2 and Code 3 documents, delivery of certification, NCRs raised by contractor, NCR closed on time etc
- previous experience.
Figure 3 – Quality Organisation and Reporting Lines
Surveillance steps:
The person carrying out the surveillance (assessor) would issue a Surveillance Notification one week before the planned surveillance to the Supervisor Rep, who would communicate the Surveillance Notification to the Contractor via a formal project manager communication (PMC).
A checklist would be prepared using the Technical Surveillance Checklist template. The checklist was devised using the works information and associated specifications and standards and seek evidence of compliance.
- Opening Meeting
The Supervisor Rep, the relevant CRL Quality Manager, Contractor Quality Manager or their nominee and Contractor Representative responsible for the works were requested to attend a surveillance Opening Meeting. The Opening Meeting detailed the surveillance format, the topics to be covered, and the process following completion of the surveillance.
- Surveillance
A representative of the Contractor responsible for the work undergoing surveillance was required to be present during the surveillance.
The surveillance would consist of but not be limited to the following:
- Review of contract documentation to confirm that requirements have been met;
- Examination of work in progress and completed work to confirm that requirements have been met;
- Review of records in progress and completed work to confirm that requirements have been met.
The surveillance identified whether or not there was evidence of compliance to the checklist, which would result in either NCR’s, positive or negative Observations being raised.
- Exit meeting
Those in attendance at the Opening Meeting were requested to attend an Exit Meeting to discuss and agree any findings arising from the surveillance, and any documentation/ information required for post visit review. An Exit Note was prepared by the assessor using the Technical Surveillance Exit Note template[4]. This was signed by the Contractor Quality Manager or their nominee or Contractor Representative.
Documentation and/or information requested for post visit review would have to be provided by the Contractor within 3 days of completing the surveillance. Unless a valid reason (at the discretion of the assessor) was presented, failure to provide the requested information within the allotted time frame will result in a non-conformance.
- Surveillance Reporting[4]
A Technical Surveillance Report was produced by the assessor using the Technical Surveillance Report template.
An executive summary provided an overview of the works, the activities examined and findings (NCRs and/or Observations).
The main body was an account of the results of examination of the various activities that were taking or had taken place during the surveillance visit. The detail of each topic verified had to include references to identity the work examined (e.g. pile number, location of excavation, design process, design output), references to records, supporting documents and documents that specify requirements as appropriate.
The completed Surveillance Report would be finalised, reviewed by Supervisor Rep, approved by Head of Quality and issued within 3 weeks of conducting surveillances and formally issued to the Contractor via PMC.
Figure 4 – Statistics
Lessons Learned and Recommendations for Future Projects
- Surveillances to be based on the project’s weekly look ahead programme as work activities constantly change from the main project schedule, obtaining an advance copy of the schedule is essential to assist with surveillance planning and to highlight key activities on site.
- In addition to the seven day notification, the surveillance procedure should also make allowances for visiting site with little or no notification.
- It is important to get ‘buy-in’ and support at the highest level to help to drive the importance of the necessity for audits and surveillances across the programme.
- Two ways communication with site team to build trust and improve the free flow of information.
- An effort should be made to gain the confidence and support of Site Teams so they can see the benefit of the surveillance process.
- The surveillance process should be developed at an early stage in the programme so it is universally accepted by all parties within the organisation. It can then be used to provide clear detail and visibility of risk based activities.
- Wherever possible and practical (and to avoid duplication) collaborative surveillances should be undertaken jointly with the Contractor.
- Detailed Surveillance Checklist with clauses from Works Information, Specification etc copied into the check list.
- Do not hesitate to raise findings but be open and communicate to the site team at first instance and give them chance to explain.
- In some cases it was difficult to get contractors to close out findings raised from surveillances. Raising significant findings as NCRs helped to raise the profile of findings to address this.
- Make people feel comfortable, explain how your visit/findings can help the project overall and share the learnings from other sites.
- Publish a 12 weekly rolling risk-based schedule and ensure factors such as adverse NCR trends, critical activities feature into the formulation of the schedule.
- Ensure findings are clear, unambiguous, and agreed within the closing meeting. Any actions agreed should be tracked via regular quality meetings and their progress monitored via dashboards visible to project management.
- The surveillance process should follow typical audit protocol as per ISO 19011 with the inclusion of photos, documents, and other relevant information as evidence.
- The surveillance process would benefit from incorporating detailed trend analysis of surveillance findings. At Crossrail the benefit of this was not fully realised.
References
Appendix A – Technical Surveillance Procedure
Appendix B – Technical Surveillance Notification
Appendix C – Technical Surveillance Checklist
Appendix D – Technical Surveillance Exit Note
Appendix E – Technical Surveillance Repor
Abbreviations
3LoD IAF – 3 Lines of Defence Integrated Assurance Framework
CEG – Chief Engineer’s Group
CRL – Crossrail Ltd
DLR – Docklands Light Railway
EL – Elizabeth Line
ELC – Elizabeth Line Committee
ELDG – Elizabeth Line Delivery Group
ELPAG – Elizabeth Line Programme Assurance Group
IIPAG – Independent Investment Programme Advisory Group
IM – Infrastructure Manager
LUL – London Underground Limited
NCR – Non-conformance report
NR – Network Rail
PPA – Project and Programme Assurance
RfL – Rail for London
SR – Supervisor Representative
TfL – Transport for London
-
Document Links
-
Authors
Kerli Saarnik MCQI - Crossrail Ltd
Kerli Saarnik MCQI, charted quality professional, was the Stations, Shafts and Portals Quality Manager at Crossrail from November 2019 until March 2023. In that role she was responsible for implementing all aspects of Crossrail’s quality assurance management system through design, construction, testing, commissioning and handover and leading the team that monitored and oversaw contractor performance and compliance with all contractual information governing quality control and quality assurance.
Kerli began her career at Crossrail working for Tier 1 contractor at the very start of the project, implementing the quality management for tunnelling, sprayed concrete, station build and Mechanical, Electrical and Plumbing (MEP) work in construction.
She has over 20 years’ experience working on the construction including major infrastructure project experience within both client and contractor organisations.