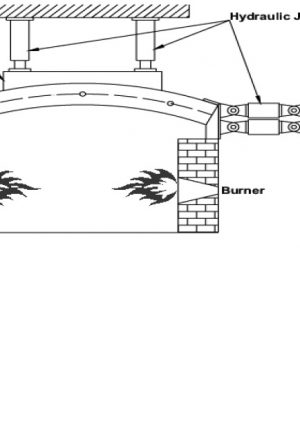
Design of Crossrail’s Precast Tunnel Linings for Fire
Document
type: Technical Paper
Author:
Jessica Ryburn BEng (Hons) MSocSci CEng MICE, Harnaik Mann MEng, Stephen Doran BSc CEng FICE, Karen Cheung BEng MSc CEng MICE, ICE Publishing
Publication
Date: 03/11/2014
-
Abstract
This paper describes the approach taken to design Crossrail’s precast concrete running tunnel linings for structural stability during a severe fire incident.
In recent decades there have been a number of fire incidents in road and rail tunnels which have caused severe damage to the lining structures. These incidents have demonstrated that fires in tunnels can heat up much more rapidly than assumed by the standard cellulose design fire curve and that concrete in tunnel linings is prone to explosive spalling. As these issues are not as prevalent for the design of other types of structures they are not (yet) explicitly covered by prescriptive design rules in design codes and standards.
The approach taken for the design of Crossrail’s precast concrete tunnel linings involved an initial design phase assessment followed by pre-construction phase verification testing. The design phase assessment used thermal material properties obtained from historic testing of the Channel Tunnel Rail Link (CTRL) precast lining segments. These properties were used to model the temperature distribution in the Crossrail lining segments when exposed to a RABT-ZTV fire design curve. A simplified calculation method was then used to estimate the capacity of a reduced structural cross-section, which had been estimated from the temperature distribution and included a nominal allowance for spalling. This was compared against an accidental loading case.
Prior to construction, prototype Crossrail lining segments were subjected to full scale fire testing under load. Crossrail’s main running tunnels are split into three separate construction contracts, each of which is independently manufacturing precast concrete segments using different concrete mix designs. Therefore three separate test programmes were undertaken.
The results from these test programmes are compared with the design phase predictions and show good agreement.
-
Read the full document
Introduction
Crossrail is a new high frequency, high capacity railway, involving the construction of 21 kms of twin 6.2 m diameter precast concrete segmentally lined running tunnels beneath central London.
An important design requirement for the Crossrail tunnel linings is that in the event of a fire the linings must continue to carry the ground loads. This is not only for passengers and staff in the tunnel escaping and the emergency services responding, but also to ensure that such an accident does not result in a collapse that endangers populated areas of the city on the surface above.
In recent decades there have been a number of fire incidents in road and rail tunnels which have caused severe damage to the lining structures. These incidents have demonstrated that fires in tunnels can be much more intense than assumed by a standard design fire curve and that, especially in such conditions, the high strength concrete used in tunnel linings is prone to explosive spalling.
The design for such severe fires is not a prevalent requirement for other types of structures and therefore design for these fires is not (yet) explicitly covered by prescriptive design rules in design codes and standards. The approach taken by Crossrail therefore involved not only a design phase assessment based on the principles of BS EN 1992-1-2 but also pre-construction testing in order to verify the design.
The main running tunnels were split into three construction contracts, each of which is independently manufacturing the precast segments used in their section of the project. Therefore three sets of verification testing were carried out for three different concrete mixes and are presented for comparison with the design phase assessment.
Specified requirements
Applicable Time-Temperature Curve
Structural fire resistance is usually assessed against an assumed “design fire” time-temperature curve, which defines the temperature at the surface of the concrete throughout the duration of the fire.
The design fire for building structures is usually taken to be the ISO 834 (BS 476) standard fire curve, which is a “cellulosic” fire based a fuel load comprised of wood, paper, furniture and fabrics. Fuel loads in tunnels however, can be greater than this and burn much more rapidly with greater intensity. Therefore project standards required that the tunnel lining meet the more severe RABT-ZTV (EUREKA) curve, reflecting the recent adoption of EU Directive 2008/163/EC –L64 – TSI on Safety in Railways Tunnels in the trans-European conventional and high-speed rail system.
The RABT curve assumes an intense fire of short duration. A maximum temperature of 1200oC is reached within 5 minutes, and the fire duration is 60 minutes. A cooling period between 60 minutes and 170 minutes is defined. By contrast the standard curve only reaches a temperature of 576°C after 5 minutes and a temperature of 945°C after 60 minutes. No cooling period is defined. The significance of the much higher rate of heating (thermal shock) of the RABT curve fire is that the risk of explosive spalling of the concrete lining is greatly increased.
Figure 1 RABT EUREKA Time –Temperature Curve and Standard ISO 834 Time Temperature Curve
Mitigation against spalling
Crossrail’s precast tunnel linings comprise of Steel Fibre Reinforced Concrete (SFRC) and except in a few specific locations, do not contain conventional reinforcement bar. A minimum concrete compressive strength of C50/60 was specified although the actual concrete strengths used in the works tended to exceed this requirement in order to satisfy other aspects of the specification.
Concrete is usually considered to perform well in fire scenarios as it does not combust and has good insulating properties. Concrete begins to loose strength around 300°C and suffers considerable reduction in strength if subject to temperatures above 550-600°C, however if there is no spalling, the over-heated concrete is usually limited to the surface facing the fire and this heat damaged concrete surface layer continues to act as insulation for the inner concrete which, being cooler, retains strength and continues to carry load. If spalling occurs, that is if pieces on the surface of the concrete break-off, a new layer of concrete will be exposed to elevated temperatures. This layer may in-turn overheat and spall exposing the next layer. If such progressive spalling is allowed to occur the section size could be reduced to the point where it is no longer adequate to sustain the loads. Hence minimising the potential for concrete to spall is a key design requirement.
Following industry practice, Crossrail’s approach to mitigate against the risk of spalling was to specify the use of polypropylene fibres, which melt at relatively lower temperature (140°C) creating a more porous structure which allows vapours to escape thereby mitigating potential spalling due to excess pore vapour pressure. In order to reduce the severity of potential spalling due to internal thermal stresses, the choice of aggregate was also limited to Limestone or Granite, these materials have a coefficient of thermal expansion closer to the cement paste compared with other aggregates.
However the phenomenon of concrete spalling is not well enough understood to be sure that a prescriptive approach to concrete mix design will guarantee that spalling will not occur. Therefore the specification additionally required that the chosen mix design, when tested under a load which representing the maximum ground load, did not exhibit any surface spalling exceeding 25 mm depth.
Structural Design Assessment
Thermal Analysis
As the design fire curve varied from the standard fire curve, the general thermal profiles given in Eurocode 2 were not applicable to this design and so another source of information was required to estimate the temperature profile through the lining section under the design fire conditions. The approach adopted for Crossrail’s assessment was to investigate the data from physical fire tests that were carried out on an earlier project, the Channel Tunnel Rail Link (CTRL). This was based on the reasoning that CTRL had used similar Steel Fibre Reinforced Concrete to that specified for the Crossrail project and would therefore be applicable data.
However a straight correlation was not possible as the CTRL tests had been carried out against the standard fire curve rather than RABT data. Therefore instead the temperature data from the CTRL tests was back analysed using a software package called TEMP/W. This information had been obtained with thermocouples that had been placed at different depths within the test panel. The aim of the back analysis was to establish appropriate values for the thermal parameters: thermal conductivity and volumetric heat capacity.
The final calibrated temperature profile showed good agreement with the CTRL data. Contrary to expectations for a higher strength concrete, the lower limit of thermal conductivity given in BS EN 1992-1-2:2004 3.3.3 provided the best match. Volumetric heat capacity was taken to be 2.5×106 J/m3.
These thermal properties were then used to model the thermal response of the Crossrail lining against the specified RABT curve.
The results of Temperature vs. Time for different thermocouples are presented in Figure 2.
Figure 2 Modelled thermal response of Crossrail lining under RABT-ZTV fire curve (Cheung and Doran, 2010)
Structural capacity calculation
Eurocode 2 broadly categorises three different methods for verifying the structural capacity of concrete structures exposed to fire. These are:
• Tabulated Data
• Simplified Calculation Methods
– 500 0C Isotherm method
– Zone Method
• Advanced Calculation ModelsBoth the tabulated data and 500°C Isotherm Method calculation method are based on standard cellulosic fire exposure and were therefore not strictly applicable the Crossrail segment design. The zone method and advanced calculation methods require knowledge of the material properties of the SFRC for the relevant temperature range and more significantly, for the relevant rate of heating. This information was not known. Hence the designers had no strictly complying codified design methodology for this situation. However the 500°C Isotherm Method, described Annex B of EN1992-1-2, did provide a codified principal for basing structural capacity calculations on a reduced of the cross-section thickness, ignoring the heat damaged zones at the concrete surface. Therefore the 500°C Isotherm method was adopted because in the absence of relevant data it was considered that a more onerous calculation method would not have guaranteed a more accurate result and also because pre-construction testing would provide the opportunity to verify the design assessment.
Annex B of EN1992-1-2 describes the 500°C Isotherm Method. The heat damaged zone is defined as the depth of the 500°C isotherm. The strength and stiffness of the heat damaged zone is neglected, whilst the remaining section retains its initial values of strength and elasticity.
Based on the TEMP/W modelling, the 500°C Isotherm curve was found to be located 40mm from the heated side. An additional loss of section of 25-35 mm due to spalling was allowed. Therefore section capacity calculations and segment joint capacity calculations were based on a reduced 225mm thick section. These calculations assumed an accidental load case with partial load factors taken as 1.0 and material factor of 1.2 in accordance with BS EN 1990 and BS EN 1992-1-1 respectively.
Figure 3: Section model adopted for structural calculations
Testing of Prototype Segments
Loading during testing
For physical fire tests to be relevant they need to mimic in the in-service conditions in terms of the magnitude and duration of the fire, the ground loading and restraint of the element tested (refer Figure 4). Owing to a circular shape and embedment in the ground, segmental tunnel linings will be prevented from thermal expansion during a fire and therefore be subject to additional stress due to thermal effects. These thermal stresses can be quite significant especially in the hotter surface layers.
Figure 4: Typical in service loads on a tunnel
In the last few decades there have been a number of research projects in Europe to investigate the effects of fire on tunnel linings which have used varying test set-ups, including the use of post tensioning cables to mimic in-service hoop loads. For Crossrail a similar test set-up that was developed for the EUREKA project was adopted. The test set-up seeks to mimic the ground loads via application of force via horizontal and vertical jacks as shown in Figure 5.
Figure 5: Fire test set-up arrangement used at Crossrail, which was adopted from the EUREKA-Project EU499
The initial intention of the fires test specification was to preload a test segment using hydraulic jacks to a load equivalent to the ground load and then restrain the segment so that it could not deform during the fire test. However it would have been difficult to restrain the segments in such a manner with the available test equipment, so instead the segment was preloaded to a load equivalent to the worst case in-service ground loading plus an additional load calculated to be equivalent to the thermal stress that would be experienced by the restrained fibres on the intrados of the segment during a fire. During the fire test the segment was permitted to deform while the load was held constant.
Test Configurations
Fire Test for two of the Construction Contracts (C300 and C305) were carried out by Efectis Nederland BV Centre for Fire Safety and the third (C310) at MFPA Leipzig GmbH, Leipzig Institute for Materials Research and Testing. The two test facilities employed slightly different test set-up arrangements to suit their existing facilities and the individual requirements of each particular contract as shown in Figures 6a and 6b and 7a to 7c.
Figure 6a: Arrangement of Thermocouples in Test Segments tested at the Efectis Nederland facility (thermocoupes at 125mm – 275mm depth were omitted in the C305 samples). (Vermeer and Kortekaas, 2012), (Vermeer and Noordijk 2012)
Figure 6b: Arrangement of Thermocouples in test segments tested at the Liepzig facility (Dehn and Juknat, 2012)
Figure 7a: Test load arrangement for C300, Efectis Facility (Vermeer and Kortekaas, 2012)
Figure 7b: Test load arrangement for C305 Efectis Facility (Vermeer and Noordijk 2012)
Figure 7c: Test load arrangement for C310 Leipzig Facility (Dehn and Juknat, 2012)
Mix Design
C300 BFK-13 (mix B10) C305 Specimen 1 C310 CRL8 Test Laboratory Efectis Efectis Leipzig Age at testing (days) 68 65 36 PP-fibre content
(kg/m3)
1.01 2.0 1.5 Steel fibre content
(kg/m3)
35 30 30 Powder content (kg/m3) 410
(287 CEM ; 123 PFA)
450
(337 CEM I, 113 PFA)
460
(258 CEM I, 172 GGBS, 30 filler)
Aggregate type Limestone Limestone 86-93% Limestone2 Moisture content Not known Not known 3.75% 28 day cube compressive strength (MPa) 69.1-88.3 68.5-75.2 87.9 – 94.7 Table 1: Passing test sample mix design
1 The steel fibre content was increased to 40kg/m3 for the actual segment production in order to satisfy other specification requirements.
2 Permission granted to use an aggregate source local to the precast factory, which contains 6-14% other minerals.
All three Contracts tested more than one sample with differing amounts of polypropylene fibres. The data of the passing samples are presented in Table 1. There were a number of other samples with lesser poly-propylene fibre contents that were tested and did not pass.
Results and discussion
Passing Samples
The measured thermal distribution through the segment during the fire test are shown in Figure 10a to 10c below and summarised in Table 2. It can be seen that these results are comparable to the modelled design temperature distribution in Figure 2.
For further comparison, Figure 8 from BS EN 1992-1-2 shows the design thermal response under standard fire conditions for a 200 mm thick slab and is also summarised in Table 2. Figure 9 shows the results from the CTRL physical fire tests. The maximum temperatures obtained from the BS EN 1992-1-2 standard fire curve temperature distribution are in a comparable range to maximum temperatures observed in physical tests again RABT curves at depths of 25-100 mm, although the standard values are not always conservative compared to the physical test results. However as BS EN 1992 allows the use of 500oC Isotherm Method with any time heat regime which causes similar temperature fields in the fire exposed member, these results gives confidence in the applicability of the structural calculation method used in the design assessment.
Scenario Average spalling depth (mm) Max Spalling depth (mm) Temp at approx. 50mm depth1
oC
Temp at approx. 75mm2 depth
oC)
Design prediction, RABT fire 0 03 405 (after 120 minutes) 260-280 (after 120 – 170minutes)
C300 passing test sample, RABT fire 13.5 35 350 – 380 (at 100-120 minutes) 250-280 (after 120 – 170minutes) C305 passing test sample, RABT fire 8.4 13 mm 300 – 325 (at 120 minutes) 230 (after 120 – 180minutes) C310 passing test sample, RABT fire 3 14 mm 375 – 420 (at 100-120 minutes) 40 mm depth
275 -315 (at 100-120 minutes) 60 mm depth
220-250(after 120 – 175 minutes) 80mm depth Standard fire, 200 mm thick slab,
EC 1992-1-2:2004 Figure A.2
0 0 390 (after 120minutes) 240-330 (after 120-180 minutes) Table 2: Summary of passing Crossrail fire tests
1For the C310 test, no thermocouple was present at 50 mm depth – 40 mm & 60 mm is data presented in table instead.
2 For the C310 test, no thermocouple was present at 75 mm depth – 80 mm is data presented in table instead.
325mm allowance for spalling was taken into account in the structural capacity calculations, however thermal modelling was based on 300mm section
It can be seen from Table 2 that the C300 sample with 1% poly-propylene content did not strictly comply with the specification for maximum spalling depth. However as the depth of the 500oC isotherm was less than the design expectations and at the 75mm depth the temperature was less than 300oC, it was accepted to use 1% polypropylene fibres with that concrete mix.
Figure 8: Figure A.2 from BS EN 1992-1-2:2004 showing design thermal response for a 200mm thick slab exposed to a standard fire
Figure 9: Results from CTRL physical fire tests of test panels expose to a standard fire (Union Railways, 1997)
Figure 10a: C300 measured thermal response of passing test sample (Vermeer and Kortekaas, 2012)
Figure 10b: C305 measured thermal response of passing test sample (Vermeer and Noordijk, 2012)
Figure 10c: C310 measured thermal response of passing test sample (Dehn and Juknat, 2012)
Non-passing samples
Figure 11: Non passing test sample (for C310) using 0.9 kg/m3 polypropylene fibres (Dehn and Juknat, 2012)
For comparison an example from a non-passing sample is shown in Figure 11 below. This sample exhibited average spalling 60 mm and a maximum spalled depth of 155 mm, with the 500 oC isotherm essentially extending to a depth of 100 mm. It should be noted however, that despite being preloaded with a compressive load representing the maximum depth ground load plus restrained thermal expansion, none of the segments, not even the non-passing segments, exhibited a structural failure during the fire test.
Conclusion
The design phase thermal analysis results, which were based on thermal properties obtained from back analysed data from testing carried out on the CTRL project, show agreement or conservatism compared with the thermocouple data from the Crossrail physical test results. Additionally none of the physical fire test samples failed structurally while tested under loads representing the deepest cross section of the route. Also the temperature profile observed in the segment provides verifying evidence to support the validity of structural design calculations against a RABT-ZTV fire curve using the 500 oC Isotherm Method.
The non-passing fire test samples demonstrate that the most important factor in designing for fire is to ensure the potential for spalling is limited. This was achieved in the three concrete mix designs for Crossrail Segments by the inclusion of between 1.0 and 2 kg/m3 polypropylene fibres and use of limestone aggregate.
Although Crossrail intend to actively minimise the risk of a major fire incident from occurring in the tunnels through such steps as controlling the potential fuel loads and ignition sources within the tunnel and employing appropriate emergency strategies, over a long anticipated service life of 120 years and beyond the risk of a major fire incident can never be completely ruled-out. However, by taking the steps described above, and in particular by verifying that excessive spalling does not occur during a RABT-ZTV fire exposure, the designers have ensured that the potential for a major fire incident to escalate into a collapse disaster is implausible.
Acknowledgements
Permission to reproduce extracts from British Standards (Figure 9) is granted by BSI Standards Limited (BSI). No other use of this material is permitted. British Standards can be obtained in PDF or hard copy formats from the BSI online shop: www.bsigroup.com/Shop or by contacting BSI Customer Services for hard copies only: Tel: +44 (0)20 8996 9001, Email: [email protected]
References
Cheung, K. and Doran, S. (2010) “Bored Tunnel PCC Segmental Linings – Fire Calculation” C122-OVE-C4-XCL-CRG01-00008, Crossrail limited
Dehn, F. and Juknat, M. (2012) “Fire Test for Crossrail C310” Test Report No. PB 3.2/11-247-1 MFPA Leipzig GmbH
Union Railways (1997) “Fire Performance of Concrete for Tunnel Linings” Channel Tunnel Rail Link Technical Report No 000-RUG-RLEEX-00005-AB, Union Railways Ltd
Vermeer, M. and Kortekaas, P. (2012) “Fire resistance tests for Crossrail C300 tunnel” Efectis Nederland report 2012-Efectis-R0129 Efectis Nederland BV
Vermeer, M. and Noordijk, L.M. (2012) “Fire resistance tests for Crossrail C305 tunnel” Efectis Nederland report 2012-Efectis-R0698 Efectis Nederland BV -
Authors
-
Acknowledgements
Efectis Nederland BV, Figure 10a and 10b reproduced by permission
MFPA Leipzig GmbH, Figure 10c reproduced by permission