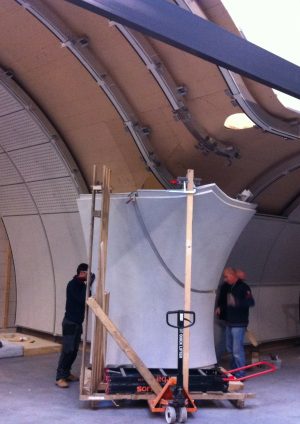
Benefits of Contractor Prototyping: GFRC Cladding on Crossrail
Document
type: Journal Publication
Author:
Jim Abatti, Jorrin ten Have
Publication
Date: 03/12/2020
-
Abstract
Extensive prototyping was carried out during the design and delivery of the Elizabeth line for the line-wide architectural components. Previous papers have covered the process of client prototyping and its key benefits. This paper concentrates on the prototyping carried out by the contractors during the construction stage, with focus on the Glass Fibre Reinforced Concrete (GFRC) tunnel cladding. The three suppliers involved were interviewed to share their experiences. In the summary, some conclusions are made about the potential benefits of the prototyping approach for DfMA (Design for Manufacture and Assembly) in architectural design and construction.
-
Read the full document
1 Introduction
Extensive prototyping of the line-wide architectural and engineering components was carried out during the design and delivery of the Elizabeth line in aid of the progressive development of technical requirements, assurance of safety and maintenance, stakeholder engagement and delivery of product value and quality. Previous papers[1] have covered the process of client prototyping and its key benefits. This paper concentrates on the prototyping carried out by the contractors during the construction stage, with focus on the Glass Fibre Reinforced Concrete (GFRC)[2] station tunnel cladding. As a methodology, the key decision makers in each contractor/supplier team were interviewed with the same questions for the purpose of eliciting the value and benefits of the prototyping approach for DfMA (Design for Manufacture and Assembly)[3] in architectural design and construction and for the delivery of outcomes required of large infrastructure projects.
They included David Shillito, director at Laing O’Rourke (LO’R); Patrick Weijers, project manager and currently managing director at Sorba; and; Franz Maidl, department head of CAD and research and development at Lindner.
This paper describes how the process used by the client company Crossrail supported the delivery of consistent outcomes at the new central London stations through the lens of one line-wide component type; the GFRC tunnel cladding. It describes the role of prototyping as a bridge between technical and design objectives on one hand, and contractor design, testing, manufacture and installation on the other. The process relates to the overall benefit and risk strategy for the principal project outcomes required: safety, reliability, usability, low-cost maintenance and passenger experience.
Benefits and risks were progressively integrated into contractors’ work informed and benchmarked by highly resolved client requirements in the form of drawings, technical reports and performance specification, validated at design concept stage by trials, prototypes and testing. In this way, contractors were able to draw on an inventory of tools with confidence that they would work in use.
The process described also mitigated risk of construction stage changes, reduced errors and actively promoted collaboration between client, designer, stakeholders and multiple contractors with extended supply chains through shared client-side information that originated at pre-contract stage.
2 Crossrail Project for the Elizabeth line
Crossrail Limited is the company delivering a new railway for London and the South East, running from Reading and Heathrow in the west, through 42km of new tunnels beneath London to Shenfield and Abbey Wood in the east. The project is being completed in phases and planned to open fully in 2021. The new railway, which will be known as the Elizabeth line, will carry an estimated 200 million passengers per year. Integrating new and existing infrastructure, the project includes the construction of 10 new stations as well as the upgrading of 30 existing stations.
Within central London there are eight new underground stations and two new above ground stations, linked by a common identity created using standardised components. This unified set of architectural components, products and assemblies form part of a line-wide design package for the public areas.
From 2009, a multi-disciplinary design team developed the line-wide design strategy, since forming a working partnership to integrate these essential components of the Elizabeth line. The team comprises engineers and package leaders from SNC-Lavalin’s Atkins business, architects from Grimshaw, product designers and wayfinding experts from Maynard, and lighting designers from GIA Equation. The line-wide designs include a range of components such as tunnel cladding, platform-edge screens, furniture, lighting and signage.
Extensive assessment of the global marketplace identified which materials and components would meet Crossrail’s project requirements and where customised designs were required. Many of these were then developed using a process of standardisation, prototyping and user testing to refine and enhance the design for manufacturing, installation and future maintenance. This approach is in line with Design for Manufacture and Assembly (DfMA), an industrial design concept that has gained more prominence recently in architecture with a view to maximise benefits from pre-fabrication.
2.1 GFRC Cladding and Client Prototype
In the five mined central London stations, the escalator barrels and public spaces at platform level are lined with curved Glass Fibre Reinforced Concrete (GFRC) panels. These provide a robust finish to cover the rough surface of the sprayed concrete tunnel engineering. The panels perform well with daily wear and tear as well as in bomb blast scenarios. Another function of the cladding is to distribute reflected light from luminaires and provide acoustic attenuation through perforated GFRC acoustic panels (see Figure 1).
Figure 1 – Production of acoustic GFRC panels at the GRCUK factory ©GRCUK
As a cladding material, GFRC is relatively new to the London Underground (LU), so its use required extensive engagement to satisfy its performance in meeting fire safety and maintenance requirements over the project’s baseline design life of 120 years. The sheer quantity required (more than 50,000 sq m) meant that a high level of standardisation was imperative to keep capital and lifecycle costs down, production and installation manageable, provide a consistent product performance.
In line with the principles of DfMA (Design for Manufacture and Assembly), the number of variations was kept as low as possible, both for individual panel geometries and in the design of the junctions and interfaces. The quantity and value of GFRC and its associated performance requirements justified the case for full-scale prototypes of the tunnel junctions; one full scale client prototype was built during the design phase in a separate facility at Vinci Technology Centre UK in Leighton Buzzard[4].
Conventionally, an architectural ‘mock-up’ is used as either an off-site visual benchmark or an installation for specific testing (for example, water tightness testing on external facades during the construction stage). The GFRC client prototype went beyond this in scope and purpose, addressing issues of manufacture, buildability, access and importantly, providing a feedback loop back into the design process that included the client and stakeholders. The prototype tested that concept stage requirements could be met and allowed the design team to progressively develop its technical performance. After the client prototyping at Leighton Buzzard was concluded, the requirement for the construction of a full size GFRC prototype was carried forward in the deliverables of the contractor.
3 Purpose of Contractor Prototype
The Contractor GFRC prototype, as required in the Station Works specification, served a purpose for both the client and the contractor. Each GFRC contractor had to build their own full-scale prototype, as an evolution of the client prototype, validating that their design and construction could meet all requirements. For the client, it was used to monitor visual appearance (i.e. the quality of production and alignment of installation), carry out access and maintenance trials, and limited performance testing (such as soft body impact tests and repair procedure tests). On occasions that the prototype did not perform to the required level in any aspect, amendments were made, and further trials carried out until the desired performance was met – thereby significantly de-risking the construction prior to full production. The second purpose of the prototype was for the Contractor to learn and optimise their systems and quality issues within their supply chains. It allowed the Contractor to coordinate and plan their supply chain in anticipation of full manufacture and installation.
Outside of the prototypes, further assurance was attained by the preceding sample regime that confirmed in progressive steps the general finish, light reflectance, anti-graffiti coating application, quality of panel perforations and edge geometry, and bomb-blast performance[4]. After the Contractor prototypes were completed and the appropriate technical approvals met, further benchmarks on site were used to judge installation quality.
In order to identify the key benefits and lessons to be learned from the Contractor prototyping, as mentioned above the three contractors who supplied GFRC for the tunnel cladding were interviewed. These were GRCUK (part of the Laing O’Rourke group), Sorba (who worked with Concrete Valley), and Lindner. Their experiences of the benefits of the prototyping process are grouped around the relationship to the Crossrail client, the design and construction phase, and the wider long-term benefit for the contractors.
4 Contractor Experience: Client
The GFRC cladding design was developed from concept design in 2009 to tender information by May 2011, with the design information progressively assured through a series of gate reviews. Although the GFRC cladding was designed to be implemented across five central London stations, Crossrail decided to procure the package as part of the individual Station (‘Tier 1’) contracts. This decision was partly based on procurement evidence in 2011 that there was no single company in the UK with enough capacity to supply all the stations within an acceptable risk profile.
To Laing O’ Rourke (LO’R), who won the tender for two of the tunnelled stations[5], the GFRC presented a major risk to the delivery of the stations. David Shillito, director at LO’R and Operations Director at GRCUK, confirms that LO’R set up their own manufacturing facility as a means of establishing control over the finishing of the product and increasing delivery certainty in handover to Crossrail. LO’R purchased a GFRC company, GRCUK, which was one of only three larger suppliers in the UK at the time, with the express purpose of utilising their people, skills and experience.
Of the other Tier 1 contractors, one went with GRCUK and two others awarded the GFRC packages to Sorba and Lindner respectively[6]. These two companies, one based in the Netherlands and the other in Germany, are cladding design and construction specialists, but they had limited experience with GFRC as a product. Sorba partnered with supplier Concrete Valley. Lindner originally worked with Betsinor in France, then GRC Beton in Poland, and ultimately set up their own facility.
For Crossrail as a client, the client prototype developed at Leighton Buzzard provided confidence in the performance of the GFRC system. This was translated into the project requirements as set out in the Station Works specification, drawings, and various guidance reports such as Lessons Learnt, Access and Maintenance Strategy and Cladding Setting-Out Guidelines.
The level of information provided was judged to be appropriate by the contractors while leaving enough room to optimise the detailed design. Patrick Weijers, Sorba, confirms that the technical requirements were clearly communicated from the client to the contractor, with line-wide design guidance showing the outline boundaries of what needed to be designed to and confirming the elements available for subcontractor design.
Crossrail also encouraged the contractors to learn from each other with the purpose of avoiding asymmetric information in the contractors’ development process and to aid in achieving consistent contractor’s designs. Franz Maidl, Lindner, concurs and adds that Lindner were afforded opportunities to share and collaborate through being shown the prototype produced by LO’R.
All contractors admit that the level of knowledge-sharing between them could have been better, but they point to the attitudes of the Tier 1 contractors getting in the way of this at times. One aspect where they believe they could have learnt more from each other was in the process of material acceptance. Both Sorba and Lindner accept that the collation of MCRs (Material Compliance Records)[], conducted at each project site, duplicated records for a single component, such as a gasket which equally could be used by another contractor on other station projects within the Crossrail programme. A single accessible repository for the collation of these records on a programme basis (where concessions had been granted), could have ensured more consistent information from client to contactor and avoided some of the issues caused by asymmetric information.
Weijers acknowledges that such a level of knowledge sharing would have been difficult to achieve prior to the award of the last GFRC package on the project due to commercial tensions.
After the initial sample regime and detailed designs had been accepted, all three GFRC contractors built their full-size off-site prototypes of a typical tunnel junction, measuring approximately 8m x 9m to a height of 5m (see Figures 2 and 3). The installation of the physical prototypes provided Crossrail with a level of assurance on the buildability, appearance and operation of the system, thereby significantly de- risking this part of the project. Shillito recounts that LO’R’s physical prototype gave the client a level of confidence that he would otherwise not easily have achieved before construction on site (see Figure 4). For his own business, it helped de-risk buildability and programme, so the prototyping benefits were distributed across the project. A lesson here for future design and build mega-projects is that the combination of consistent information from client to contractor and early construction stage testing, such as prototyping, can bring multiple benefits to enhance outcome certainty.
Figure 2 – Sorba Full scale prototype ©Sorba
Figure 3 – Lindner Full-scale prototype ©Lindner
Figure 4 – Full scale prototype at LO’R with client Julian Robinson ©Jorrin ten Have
The prototyping was part of the wider thorough assurance processes followed by Crossrail. The organisation had to satisfy many stakeholders, from representatives of the project sponsors to future Infrastructure Managers (IMs), so prototypes were key in the demonstration that the project could be built and maintained safely and in an efficient manner. This in turn provided the contractors with an element of learning about maintenance planning and quality control.
Specifically, the GFRC prototypes served to demonstrate the access and maintenance strategy to stakeholders like LU[7]. Panels were taken off and re-installed during inspections, demonstrating the equipment and methods involved and timing the operations to ensure these would be able to be carried out in the limited time available during engineering hours. As each of the contractors’ designs varied in the detail of their fixings and framing, the access strategy had to be proven for all individual systems. Crossrail maintenance planning engineers and LU premises engineers travelled to inspect all the contractor prototypes in the UK, the Netherlands and Germany multiple times between 2015 and 2017 to witness these trials in person and comment in detail. All these procedures were signed off on Inspection Test Plans[8] and became part of the contractors Operation and Maintenance manuals.
For Sorba, the rigorous testing of access and maintenance on prototypes was a novel experience. Weijers asserts that through Crossrail’s requirement to demonstrate these strategies in detail, Sorba has become more aware of the importance of this aspect to operators and going forward they will demonstrate and design with asset maintainability at early stage in future projects.
5 Contractor Experience: Design and Construction
A clear aim for the prototyping was for the contractor to learn how to manufacture and install their systems. Like prototyping in product design, this process resulted in many feedback loops into the detailed design to simplify production, minimise waste and optimise material use. For LO’R, it presented a leap in terms of the skills present in the company; both for the GFRC material itself and the cladding design. In contrast with Sorba and Lindner, LO’R is not an experienced cladding specialist. Teaming up with the office of Bryden Wood[9] as technical advisers and through the process of prototyping LO’R managed to overcome this handicap and even optimise material weights and the number of panel variations.
Approximately, 35,000 square metres (some 6.5 football fields) of GFRC panelling and 7,000 types were used across LO’R’s three stations. With Sorba, there were approximately 800 panel types on Farringdon station, and on Bond Street station with Lindner some 750 panel types. For LO’R, typical lead times for performance testing, prototypes and mock-ups would be six months. An evolution in learning and development for LO’R over 18 months helped to obtain the handover certainty that Crossrail as client required. It can thus be understood that a tangible benefit for major design and build projects alongside consistent, evidential information is planning in extended timescales to develop the production process and technical understanding with samples and prototypes.
Many trials were conducted with different mould types and materials, methods of sand blasting and cast-in fixings to achieve the desired outcome. So, by the time the first version of the prototype was ready, many of these lessons had been recorded in a large manual for internal use in the company. After the prototype established the physical feasibility of the installation, LO’R could concentrate on further optimising both panel variations across three stations. The moulds proved a critical item for many contractors, in terms of design, sign off, and the time it took for production and delivery. Due to the complex geometry of the junctions, many moulds were required Also, depending on the type of material used, ranging from low- to high-density foam, timber, and GFRP, some moulds were used as one-off, some for series of up to 10, and others to 50 before the mould would become unusable (see Figure 5).
Figure 5 – Double curved foam mould ©GRCUK
LO’R, with designer Bryden Wood developing their digital models, were able to rationalise the number of moulds. The reduction in the number of moulds (for 27,500 panels) was significant: a 30% reduction – 3,300 moulds reduced to 2,300 moulds. With each mould costing some £3,000 pounds, LO’R were thus able to introduce savings of approximately £3 million. Arguably, as parametric 3D modelling and optimisation is employed on further complex major projects, it will aid the consistency of technical information shared from client to contractor.
Reliance on external suppliers for the moulds pushed several contractors to set up their own in- house mould production. Lindner’s experience also shows that the prototyping process allowed them to further refine and rationalise the geometries of tunnel radii and panel types, thus reducing the number of moulds. Sorba and Concrete Valley took an innovative approach to this problem; they cast the single curved panels on a deformable and re-usable steel bed, thereby greatly reducing the number of required moulds (see Figure 6). This fabrication method was only possible using a poured rather than sprayed GFRC. Generally, poured GFRC is of a lower strength category, so Sorba had to demonstrate that the chosen mix (including high performance concrete), method and panel thicknesses would sufficiently address all of Crossrail’s performance requirements. While it took longer to evidence compliance through calculations, test panels, load tests, and full-scale prototyping, Sorba saved time and money later in the process – an example of how early testing and investments is suited to a successful DfMA approach and consistent project outcomes.
Figure 6 – Deformable steel moulds at Concrete Valley ©Sorba
While the other contractors did not follow this route, each made their own other innovations on the system. For LO’R, optimisation of panel weights was a key aim. They achieved this through a combination of cast-in stainless steel ribs in the horizontal spanning direction and varying the thickness of the panels according to their size and location. Lighter weight panels were easier to handle and used less concrete. This panel optimisation was combined with a pin hooking system that allowed for a very fast installation of panels once the main frame members were accurately positioned. The system innovation prompted a series of prototype tests to ascertain the effect of this system on access and maintenance. In particular, the system did not allow each acoustic panel to be individually removable – a performance requirement of the design for long term maintenance. After successful time trials at the full-scale prototype in the presence of LU engineers, it was decided to leave the lowest row of acoustic panels individually removable and use the pin hooking system for the upper panels. This process showed that the prototype was not there merely as a finished piece for acceptance, but also functioned as a working test and design development model. LO’R’s third innovation was the structural system around the tunnel junctions. Rather than using 3D curved steel members for framing, LO’R used an integral GFRC shell, made up of four connected elements as the structural carrier frame. This unusual approach, called the ‘tusk’, was calculated in detail and prototyped at full scale in order to give Crossrail the confidence that it was going to perform satisfactorily.
For the client, these innovations presented potential efficiencies in cost and construction, but the specification requirements for access and maintenance had to be closely guarded. The prototype proved to be the most effective way to ensure that the systems could be safely and efficiently maintained.
Lindner’s approach to innovation was to base the GFRC framing system on technology developed in their interior cladding business. By using a toggle clamping system accessible through the vertical joints, each panel became fully individually demountable without the need for multiple face fixings on each panel. Although the principles of this system were explored through drawings and models, it was again the prototype that demonstrated the effectiveness of the approach.
The complex geometries of the stations and the technological innovations proposed by the contractors were only possible to achieve through detailed and accurate 3D modelling. Lindner produced a detailed 3D model which was used to pick up details such as additional bracketry to aid the fabrication process. The model served as a general BIM model but it also became a means to determine construction processes and the exchange of information between the Tier 1 contractor/station designer and Lindner as a Tier 2 supplier of the GFRC cladding (see Figure 7).
Figure 7 – Lindner 3D model ©Lindner
In some way, the prototyping was therefore not only a test of the physical objects, but also of the processes required to achieve these. The contractual set-up provided many challenges in the communication and acceptance of proposals. Franz Maidl identifies that Lindner would often receive inconsistent information being passed down the supply chain. Lindner would receive the line-wide design in parts, amended with updates from the Tier 1 contractor via their designer. Lindner experienced numerous changes and new instructions which became a challenge to manage due to the lag-time in information being received by Lindner as a Tier 2 supplier. Thus, the contractor’s designer was not always able to review designs submitted by Lindner as they had changed works information instructed to them. The process of client information being passed along the supply chain became slow at times, alongside an elaborate contractual mechanism which was not acting lockstep with the required information flow[10].
LO’R’s Shillito criticises the process when compared against advanced manufacturing processes such as in the automotive industry – the inspiration behind DfMA in construction – where change requirements are held back by the sponsor before manufacture even commences.
6 Contractor Experience: Wider Benefits
The tunnel cladding on the Elizabeth line-wide design presented a large volume and was complex to deliver because of 3D geometries, demanding performance requirements and restricted installation. The challenges of delivering this package posed such risks to programme and cost that the contractor had to gain a higher degree of control over their own suppliers and manufacturing processes. This was most obvious in the case of LO’R who set up their own new factory as GRCUK and were therefore able to plan out and optimise each step of the production process. But beyond responding to a need on the project this move has transformed part of LO’R’s business. LO’R subsequent to the Crossrail programme now possess their own GFRC business where previously they held none and have used lessons learnt on Crossrail to drive forward their manufacturing processes. Already, the firm is looking to use these new capabilities on subsequent projects such as the Sydney Metro. Shillito here does not merely refer to the physical production of the cladding panels; the process of applying a fully digital workflow is still relatively new in the construction industry.
Lessons learnt through the physical prototyping could be fed back into the digital workflow and the client was able to review detailed proposals and variations directly in 3D. This way of working still informs GRCUK’s current work but Shillito has found the uptake within the larger organisation of LO’R to be slow.
Lindner was confronted directly with the risks of the package when their initial GFRC supplier went into administration. Relatively late in the programme, they had to change supplier[11]. The experience motivated them to take even more control of the process and set up their own GFRC business.
Although the decision by both Contractors to set up their own GFRC facilities seems primarily driven by risk reduction and future business opportunities, the process of prototyping and design development presented by Crossrail enabled LO’R and Lindner to get familiar with the product. It allowed them to build up enough of a knowledge base to understand the risks and opportunities related to the material as well as the digital processes involved in the making of the panels.
It is clear from the points above that the process of the Contractor developing the GFRC production design has indirectly hugely benefited their own capabilities regarding future work. In contrast, the Contractors were initially reluctant to engage in a thorough design and prototyping process. At several points the client requirement for prototyping was challenged and the need for maintenance trials was questioned. Although the process at that time may have seemed to the Contractor to be time consuming and costly and the benefits unclear or limited, they gained from the knowledge built up in the process to improve their own operations and business. A better understanding of these indirect benefits could help to overcome the initial reluctance.
7 Conclusions
In summary, the prototyping process for the GFRC cladding on Crossrail presented various benefits for the contractor in relation to different aspects of the process.
7.1 Client
The level of information provided by Crossrail was consistent, effective and evidential, allowing three different Tier 2 contractors to understand the performance requirements of the cladding system while allowing them enough room for individual innovation to optimise their detailed design and manufacture. Consistent information combined with the planned prototyping process provided the client with a level of assurance that the different solutions developed by the contractors would all meet the requirements of the system. The physical prototype helped de-risk the GFRC cladding by providing the client with a level of assurance on the buildability, appearance and operation of the system. The prototype was used to demonstrate safety and access as part of this assurance. The prototyping process allowed the Contractor to learn how to include maintenance planning and quality control in their design and manufacturing processes.
7.2 Design and Construction
The prototype aided the contractor to learn how to manufacture and install their systems prior to full production and site installation. This resulted in simplified production, minimised waste and optimised material/mould use, thereby saving money on the production costs. The process allowed the contractor to build up the necessary skills and knowledge including advanced 3D parametric modelling with geometric outputs that could be used directly for production of moulds (see Figure 8).
Figure 8 – Consistent finishes and quality across Elizabeth line stations
7.3 Wider Benefits
The quantity and complexity of delivering the GFRC with its associated risk led contactors to use their learning for their own business development, with two of them setting up new production facilities in the process. This means the benefits from learning on Crossrail can be carried forward to future opportunities.
The contractors all developed in-depth knowledge about the materials and production processes that were not previously part of their core business. Having proven their systems by physical prototype, the contractors were able to develop their digital workflow to a high accuracy, setting up processes seamlessly linking design development and design changes to rationalisation, production design and manufacture.
7.4 Key Learning for Other Major- and Mega-Projects
Crossrail’s approach to line-wide design was informed by client expertise across a wide range of UK mega-projects such as St Pancras, HS1 and the Jubilee line extension. It forms relevant learning for most future major- and mega-projects, as a design and procurement process but also as a risk assignment approach in contrast to more traditional methods.
In Crossrail’s case, the client acknowledged project risks at an early stage and mitigated these through collaborative working relationships. This approach involved the progressive disinvestment of risk from client to contractor, ultimately benefiting operational cost, reliability of quality and durability. Important aspects of this approach were defining the line-wide requirements, allowing for design iterations and testing early in the process, and reducing complexities to a level where the supply chain could effectively resolve the remaining ones. Designs were then carried through with client and contractor prototyping and benchmarks for collaborative working, input from supply chain expertise and sponsor engagement and buy-in. This paper has focussed on the contractor prototyping aspect of the approach.
In summary, the GFRC contractor prototyping provided a test of the physical objects, but also of the processes required to achieve these. Having identified the above benefits, the relevance of these to the wider industry and DfMA approaches can only be understood by looking at the project conditions and the challenges overcome. The GFRC cladding on Crossrail presented a potential economy of scale, through reduction of the time on site and the complexity of product. Sectors that feature a comparable scale, complexity of construction, and maintenance critical operations would all be likely candidates, such as the transport and energy sector, and to a lesser extent large commercial or residential development with a high degree of repetition.
Crossrail also provided a project condition where the long civil works programme allowed for time to engage in prototyping and testing of the fit-out. Budgets were allocated to support this process from, initially with client prototypes and throughout with client-side technical advice and guidance.
Challenges were both the management of information and the management of variation. Some of the information flow processes, such as MCRs and 2D versus 3D technical submissions, were only developed throughout the process and at times suffered from complicated contractual relationships between the different tiers of contractors and consultants. In order to allow contractors room for optimisation and innovation, Crossrail had to actively manage the quality and consistency of the outcomes through continued guidance from the original design team (see Figure 9).
Figure 9 – Installation of GFRC cladding in a station tunnel
The main lesson from the GFRC prototyping on Crossrail is how this process supports de-risking and optimising a large and complex part of the project through the combination of performance requirements and prototyping requirements. It is an approach that aligns with the idea of DfMA and digital workflow in architectural design and production. The necessary level of client involvement, through planning, early investment and continued guidance should not be underestimated. In parallel, many contractors are reluctant to engage in prototyping; it is seen as costly, slow and unnecessary. This was also the case on Crossrail in the initial phases of contractor involvement. However, the benefits that resulted from the prototyping have become clear to the contractors during the process and all three are now strong advocates of Crossrail’s approach to this part of the line-wide design; they are already applying the gained knowledge to other major- and mega- projects such as the Sydney Metro and London Underground extensions.
Perhaps further industry guidance on prototyping as part of DfMA in construction could be developed to help to educate and communicate this process for future projects. The authors of this paper certainly hope that these lessons from Crossrail will inform future clients and contractors to organise their processes using the full benefits that prototyping can bring.
References and footnotes
[1] Neill McClements, ‘The Value of Common Design – C100 Crossrail Architectural Components’ and Simon Atherton, Stuart Moxon, ‘The Importance of Construction Mock-ups and Trials’ in Crossrail Project: infrastructure design and construction Vol. 1, ed. by Mike Black and others (London: ICE Publishing, 2014) 2 Glass fibre-reinforced concrete consists of a composite of high-strength, alkali-resistant glass fibres embedded in a concrete matrix.
[2] The concept of Design for Manufacture and Assembly originates from the manufacturing industry as a form of lean engineering with the aim of reducing manufacturing and assembly costs and to quantify improvements through decisions in the design process.
[3] After an initial visual mock-up of a section of platform was completed in 2010, Crossrail constructed a full scale GFRC cladding prototype working with GFRC manufacturer BCM during 2012-2013.
[4] A series of prescribed tests on panels of varying sizes was carried by each contractor out prior to building the full prototype. GFRC as a material has varying properties depending on the types and amount of aggregates used as well as the glass fibre length, method of manufacture etc. Light reflectance, acoustic performance and blast performance could not be accurately calculated for this type of cladding and therefore required physical laboratory testing.
[5] Tottenham Court Road station and Liverpool Street station.
[6] GRCUK, Sorba and Lindner acted as Tier 2 contractors responsible for the design, manufacture and installation of the GFRC cladding. They in turn used different material suppliers and installation contractors. 10 As part of the Quality Assurance plan on Crossrail, Tier 1 contractors were contractually obliged to summit material compliance records on each component/material to be utilised on the project. These provided evidence for compliance on issues such as fire resistance and durability and were checked against the Employer’s requirements.
[7] The future operation and maintenance of the central Elizabeth line stations falls under the Infrastructure Managers, London Underground and RfL (Rail for London).
[8] Inspection Test Plans (ITPs) were part of a rigorous process to check against requirements and gain acceptance from the IMs.
[9] Bryden Wood is a design and engineering practice focussed on developing DfMA solutions and off- site construction.
[10] Dan Harvey, ‘Crossrail May Not Open Until 2021 – Reports on Problems with the Project Identified in a Report From the NAO’ Modern Railways, June 2019 pp 17-20.
[11] Lindner changed supplier twice, from Betsinor to GRC Beton to their own in-house production facility, now named Lincrete.
-
Authors
Jim Abatti - Atkins
Jim Abatti is a Senior Architect within the Infrastructure sector of the Atkins legacy business. He has worked on various roles on the Crossrail programme, ranging from lead architect on the frame-work design consultant role for Bond Street station, supporting contractors at Farringdon and latterly as part of the line-wide design team.
Jorrin ten Have - Grimshaw
Jorrin ten Have is an architect and Associate Principal within the international architecture practice Grimshaw. Jorrin has led the line-wide design team as project architect since the start of contractor involvement to construction and installation on site. As part of this role, he was extensively involved in the detailed development and prototyping process of the GFRC systems and advised Crossrail on their acceptance of the contractor’s designs.
-
Acknowledgements
David Shillito, GRCUK, Sharing experience and insight
Franz Maidl, Lindner, Sharing experience and insight
Patrick Weijers, Sorba, Sharing experience and insight
-
Peer Reviewers
George Stowell, Atkins