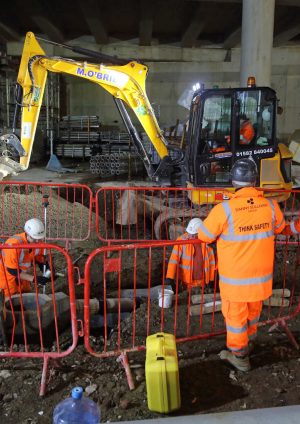
Collaborative Approach to Health and Safety Assurance Activities
Document
type: Micro-report
Author:
Ian Charlick
Publication
Date: 27/09/2016
-
Abstract
Traditionally, assurance activities have consisted of legislation/contract focussed audits, potentially leading to Corrective Action Requests (CARs), which the Contractor closes without assistance. Crossrail assurance audits were designed to trigger collaboration between Client and Contractor; the audits are (in addition to checking on compliance) an opportunity for both parties to work together, to ensure that the improvements implemented represent best practice. The audits are focussed on improving health and safety, rather than just demonstrating compliance.
This paper would be of interest to Health and Safety assurance specialists, contractors and any projects looking to improve their health and safety assurance.
-
Read the full document
Introduction and Industry Context
The purpose of Health and Safety Assurance is to provide confidence that an organisation, service or product:
- Meet specified health and safety requirements; or
- Identified the need for intervention when health and safety requirements were not met or were unlikely to be met
Crossrail’s Health and Safety Assurance processes have grown and evolved through the progress of the project. When the project started construction in May 2009, assurance activities were ‘light touch’ with each contractor providing self-assurance on their management of health and safety at their projects; by regular submission of assurance questionnaires; backed up by a single health and safety audit for each project annually.
Crossrail recognised that the light touch process was not always delivering sufficient confidence in the contractors’ health and safety management, as they were reluctant to raise issues against themselves with returns at times identifying no corrective actions, no observations and no good practices.
Audit Schedule
In 2013, Crossrail revised the Health and Safety Assurance programme, and implemented a comprehensive assurance audit schedule covering the then 23 project contractors/sites. The audit schedule was risk based, with 14 key topics and included up to six tightly focused audits per contractor, each year. This framework for audits has continued since and for the 2015 – 2016 year, there were 80 Health & Safety Assurance audits (on a variety of contractual and legislative requirements) and 21 Occupational Health audits.
In addition, with the secondment of a London Fire Brigade Watch Officer, in 2014, to take the role of LFB Crossrail Liaison Officer, 11 Fire Safety Assurance Assessments were carried out.
Audit Procedure
Audits are carried out by three Health & Safety Assurance Specialists in the Crossrail team.
Assurance Audits last one day, with an opening meeting at the start, to confirm the scope and the format of the audit. The audit is then concluded with a closing meeting, at which findings are discussed, including any Corrective Actions Requests (CARs), Observations and Good Practices that have been identified.
Audits are typically attended by the Tier 1 / Principle Contractor’s Health & Safety management representatives, with appropriate topic specialists providing detailed information and documentation, as required. Local Crossrail Health & Safety Advisors are also often in attendance throughout the audit, with Crossrail Project Managers (or other senior project team members) in attendance at opening / closing meetings.
Closing meetings are mainly attended by local Crossrail and Contractor Project management, topic specialists and Health & Safety representatives, allowing an opportunity for a collaborative approach to identifying actions that can be taken to correct non-conformances and prevent recurrence.
Where appropriate, Auditors are able to share some details of good practices and actions taken at other sites, in order to correct similar non-conformances or observations, to assist Contractors.
Corrective Action Requests (CARs)
Once agreed, CARs are “owned” by the Contractor. For completion of actions, however, Auditors are available to attend site, as appropriate, to view changes to equipment, processes / procedures and to give feedback on progress.
Protocol for CARs requires Lead Auditors to write out their findings, on a CAR Form, in two parts:
- The Required Condition
- Condition Found (non-conformity)
Auditors work in collaboration with Contractors and local Health & Safety Advisors, to determine appropriate actions to deliver a suitable improvement in the area of concern and to agree realistic dates for completion.
Observations
Observations identified during audits are also discussed during close out meetings, to help identify potential improvements which can be implemented locally.
Good Practice
Identification of good practices is encouraged throughout audits, even if they are not related to the audit topic. Auditors are able to refer to practices and innovations seen at other locations, so that these can be considered by Contractors on their sites.
Good practices identified, are highlighted at the Principal Contractors, Health & Safety Forum, which is attended by Health & Safety Managers from Tier 1 contractors and are also sent to the Learning Legacy team, for wider dissemination.
Audit Reports
Audit Reports, including details of any CARs, Observations and Good Practices are issued for all audits. Reports are issued within 10 working days of an audit, in order to maintain momentum in closing actions and to keep them topical for auditees.
Details and dates of closure actions for all CARs raised are recorded on an “Audit Findings Tracker” spreadsheet, which includes conditional formatting to identify any CARs which have 28 days or less until their planned closure date, turning red, if they go overdue. The tracker is sent out weekly, with distribution including; Project Managers and senior Crossrail Directors.
Lessons Learned
It was invaluable for Auditors to maintain a dialogue with auditees and continue to work collaboratively to discuss close out actions and improvements with relevant auditees after the audit. Visiting sites to view changes in processes, procedures, personnel or equipment that have been made and so maintain a close working relationship.
Organisations should consider the need to engage the right people in order to carry out these audits – individuals who take a collaborative approach, rather than just issuing corrective actions and leaving it to the contractors to implement.
The benefits of mutual collaboration this are clearly demonstrated as for the audit year 2015 / 16, 91% of CARs were closed on time, with the remainder closed shortly after their deadlines, therefore providing complete confidence in the assurance process.
A recommendation for improvement would be that the assurance and monitoring arrangements should be agreed at the start of the project and included in the Works Information. Failing to do this created difficulties introducing the process when construction had already started and this may be something for other projects to consider.
-
Authors
Ian Charlick - Crossrail Ltd
Health & Safety Specialist – Assurance
Ian Charlick is a Health and Safety Specialist within the Assurance team at Crossrail. He has held a number of Health and Safety roles in the rail construction industry over the past 15 years in organisations including London Underground, Metronet, Balfour Beatty, Telent and Thales. Ian has built up a substantial railway knowledge during his career, covering operations, maintenance and renewals, as well as railway civils, signaling and communications. He joined Crossrail at the beginning in January 2014, conducting contractor Health and Safety Assurance activities, including audit and assessment. Ian also works closely with the Metropolitan Police and London Fire Brigade Crossrail Liaison Officers, on business continuity, security and fire safety matters.