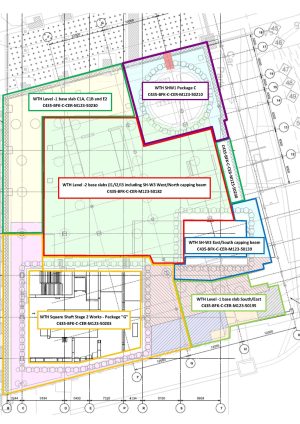
The Importance of Planning in the Production of Construction Deliverable Records
Document
type: Technical Paper
Author:
Chrys Chimarrides CEng MICE
Publication
Date: 10/05/2023
-
Abstract
Planning with the end in sight is crucial in the delivery of all successful projects, and is especially true in the construction industry, where both the works and personnel involved can change at such a rapid pace.
It is hence crucial to ensure robust pans are in place from the outset, at planning phase of any package of works, clearly outlining the approvals and records that will be required, the time they will be produced and the processes that are in place to ensure this happens in the most efficient manner. Engagement and buy-in to this from the top down – from project managers to site engineers – is crucial in achieving these goals.
This paper uses the example of the C435 Farringdon Station contract to summarise what worked well there, and what improvements could be made on future projects to ensure this plan is even more effective.
-
Read the full document
Introduction
Planning with the end in sight is crucial in the delivery of all successful projects, and is especially true in the construction industry, where both the works and personnel involved can change at a rapid pace. The focus in the construction industry – particularly in major civils works – has often been on the timely completion of all physical works on site to meet programme milestones, which in turn could release associated milestone payments. The compilation of the necessary records to illustrate compliance of these works in accordance with the accepted drawings, specifications, Standards, Works Information requirements, etc. has often then taken second place and been treated as an after-thought, for the site engineers and quality teams alone to deal with.
The high fluctuation in personnel when certain packages of works are completed, with engineers moving onto their next assignments, can also lead to the loss in records, knowledge and relationships (e.g. with the supply chains) that would otherwise enable the smooth and timely production of the aforementioned records. This paper suggests the release of personnel should only be considered once they have handed over both (1) the physical works and (2) construction deliverable records for the work packages within their area of responsibility.
It is hence crucial to ensure robust plans are in place from the outset to account for the above at the planning phase of any package of works, clearly outlining the approvals and records that will be required, the time they will be produced and the processes that are in place to ensure this happens in the most efficient manner. Engagement and buy-in to this from the top down – from project managers to site engineers – is crucial in achieving these goals.
This paper uses the example of the C435 Farringdon Station contract to summarise what worked well there, and what improvements could be made on future projects to ensure this plan is even more effective on future projects.
2. Farringdon Station Construction & Certification
The scope of works at Farringdon Station included heavy civils packages (tunnelling, piling, mass excavation, reinforced concrete, structural steelwork), a variety of architectural packages (including blockwork, cladding, tiling, architectural concrete and steelwork, signage, etc.) through to numerous mechanical, public health, electrical works packages, as well as lifts and escalators, spanning across from 2013 to 2021. It was hence crucial to identify from the outset how these works would be split into manageable packages – extract below from the Crossrail Construction Certification for Civil Engineering and Station Works Procedure which provided the guidance to the Contractor in how this was to be managed for the civils packages, later also replicated across all other disciplines:
‘The Contractor is required to identify how they intend to break-up their scope of works into Construction and Sub-Construction level activities. These are to be in accordance with the construction programme, activity, asset owner, Infrastructure Manager or Subcontractor/trade, and shall be formally agreed by the Supervisor’s Rep (PFE).
The Package Breakdown Structure and Schedule is a “live” document which is to be maintained and monitored in accordance with the Construction programme. The Schedule shall indicate the planned and actual dates at which certificate packages are to be presented to Crossrail for acceptance, and the current review status.’
The visualisation of how this was split for the Farringdon Station works is illustrated below:
Figure 1 – Breakdown of Farringdon Station works into packages and sub-packages
The Contractor used the information provided to them in the Works Information (WI) to break down the contract works into the main works packages (‘Construction or Acceptance Certificates’) by discipline, as illustrated above, further broken down into geographical areas (for Civils & Architectural works), e.g. Western Ticket Hall, and subsequently into smaller, ‘Sub-Construction Packages’. Note that MEP packages were split via systems, rather than geographical areas. This was a live list of all construction packages, regularly reviewed and updated as the works progressed, ensuring the information therein was as accurate as could be, and providing a clear snapshot at any moment in time of plan versus progress.
A process was also developed for satisfying these requirements for individual sub-construction works packages. This is best illustrated using Figure 2 below (extracted from the Farringdon ‘Procedure for Readiness Review and Certification Packages’).
Figure 2 – Extract from 18.1 Appendix 1 from BFK ‘Procedure for Readiness Review and Certification Packages’
Planning Phase
The planning phase for any individual package should start several weeks and months prior to the start date of works on site – depending on the complexity of the works – and involves the preparation, review and acceptance of all documentation required to be in place prior to works commencing, inclusive, but not limited to, the below:
- Accepted construction drawings and associated design packages and design check certificates
- Material compliance records
- Inspection and test plans
- Method Statements & Risk Assessments
- Design changes (accepted Project technical Requests [PTR])
- Other relevant procedures, e.g. Cold Weather Concreting Procedures
- Third party approvals
What generally worked very well at Farringdon was the construction team drafting the individual plan for each work package summarising the above, which was then openly presented and discussed between both the Contractor and Project Manager (Crossrail) teams during regular ‘Readiness Review’ meetings, and involved key personnel from both sides, from site engineers to planners and quantity surveyors, through to construction and project managers. This allowed everyone to input into this process for each works package and ensure that all key requirements and approvals were in place, when required.
The establishment of individual ‘Readiness Review Trackers’ from the outset listing all the above deliverables meant that planning with the end in mind became second nature to the delivery teams. These trackers were updated and reviewed regularly by both parties (Contractor and Project Manager teams) who in doing so collaboratively ensured that these lists were as accurate as possible and were hence used as the tool to identify any gaps and outstanding actions, to thus focus attention and resource on these. The acceptance of the pre-construction deliverables, such as material compliance records, is hence illustrated by the red bar in the figure above, shown to the left of the ‘construction period’, i.e. starting before the physical works have commenced.
Construction Phase
Once the construction phase is in motion, the impetus shifts to the accurate and timely compilation of all associated site records, as the works progress, including:
- Inspection & test plan checksheets, illustrating compliance with all checks and control points detailed in the accepted inspection & test plans.
- Inspection & test plan test records, e.g. pull-out tests
- Recording as-built status on site drawings
- Recording site changes, inclusive of non-compliances (separately raised as Non-Conformance Reports)
Key ingredients in ensuring the above are being managed as per the agreed plans include the following:
- Regular (weekly) quality meetings, where any upcoming works requiring inspection are notified in a timely manner, for both internal (Contractor) checks and third party (e.g. Crossrail) checks, especially pertinent for ‘Hold points’, as specified in the Inspection and Test Plans.
- Ad-hoc, unannounced inspections by both Contractor and Project Manager teams of ongoing works, to note both good practices and any non-compliances/areas of improvement.
- Detailed surveillances of certain activities, e.g. concrete placement.
- Inspection and Test Plan validation exercises, which allow for a more in-depth look at the compliance with the requirements of Inspection and Test Plans, which could be used to identify any gaps in the execution of the works and improvements that could be implemented in updates to the plans.
Post-construction/certification Phase
All the above, as well as many less formal activities and discussions, helped the Farringdon team to continuously improve and streamline the process for certification of individual works packages with the main outputs (construction deliverable records) at the end of each sub-package being the below:
- Inspection and Test Plan records
- Red-line and as-built drawings
- Package listings/construction certificates (listing Project Technical Requests [PTRs], Material Compliance Records [MCRs], red-line & as-built drawings, Operation & Maintenance files, Health & Safety files, outstanding snagging works & outstanding documentation)
To aid in the repetitive nature of the production of the above, to focus attention on key requirements and to eradicate repetitive errors, a number of single-page checklists were also jointly prepared between the Contractor and Project Manager teams, which would allow the user – and checker – to ensure they had consciously considered and reviewed each of the steps listed therein. This was found to be especially useful for new members of the team that had joined partway through the project and who were thus less familiar with these requirements.
Figure 3 – Inspection & test plan records, red-line drawings and sub-construction certificates checklists
Other Farringdon processes, over-and-above standard Crossrail procedures, and further to the ones already outlined above, included the below:
- Red-line & as-built production guides, simplifying the requirements into easy-to-follow, pictorial guides with worked, site-specific examples.
- Regular, periodic reviews of new contract communications, inclusive of Project Technical Requests and site instructions that may impact – and hence may need to be illustrated on – red-line drawings, as well as needing to be referenced in the relevant construction certificates.
- Minimum assurance and red-line & as-built requirements matrix for drawings. This document listed all drawing types by discipline, stating the following key information:
- Required reviewers for each drawing type
- Drawing owner, by organisation
- End-of-life status (e.g. red-line), including responsibility for production of each drawing type
- Key notes pertaining to the production of red-lines and as-built drawings, agreed by both Contractor and Project Manager teams, ensuring a common approach to the production of these by the various members of the team involved.
This matrix was particularly useful, as it established a set of rules from the early phases of construction (in 2014) – when the drawing types were limited to the main civils and early MEP works – and further developed over the years as the various drawing types for other disciplines were produced. This ensured that a consistent approach was followed with regards to which of the several thousands of drawings produced would essentially need to be converted to red-lines and/or as-builts, or if there was joint acceptance from both the Contractor and Project Manager sides that certain drawing types could end their life as ‘issued for Construction’ (IFC) status. This aided greatly in achieving the completion of all required red-lines and as-builts on the contract, required for the successful handover of the station to London Underground.
The effectiveness of the various processes and procedures that the Farringdon team used over the duration of the contract works is best illustrated by the fact that this was the first Elizabeth Line Station with London Underground as the Infrastructure Manager to achieve completion of all Civils packages in 2019 (consisting of 140 certification packages). Farringdon Station was subsequently also the first station to have all certification across all disciplines completed and hence handed over to London Underground in March 2021 (totalling 539 individual construction packages, spanning 8 years).
Lessons learned
The paper has briefly summarised some of the key tools the Farringdon team used to successfully complete the certification of all construction works. However, there are still steps that could be taken to improve on these and make this even more effective:
- Limit scope on individual sub-packages, especially where there may be an activity therein that is expected to be completed at a much later date than the other activities forming that sub-package scope of works. This ensures that the compilation of records for the early activities already completed is not delayed to the point in time when the final activity is completed; the records can be prepared and reviewed when the engineers involved in the site works are still present, the information is recorded contemporaneously and relationships with any supply-chains providing input into this process occur while they are still fully engaged in the project. See below illustration of this issue and the way it can also be avoided by splitting the ‘construction activities’ into separate ‘certification activities’ which are prepared and certified as the other sub-package works are progressing on site.
Figure 4 – Annotation of process to illustrate how the construction and certification stages could further overlap by preparing records for completed activities contemporaneously
- Irrespective of the above, it is good industry practice to keep accurate and contemporaneous records, both for illustrating compliance with regards to all quality-related aspects of the works, but also for commercial issues.
- Illustrating the scope of each sub-package scope works pictorially as a pre-requisite, to complement the detailed and very extensive lists of construction deliverables. This makes it much clearer for anyone reviewing this information in future to fully understand the scope of works, including any third parties who may not necessarily have the historical knowledge of the scope of works, as the site teams involved would be expected to. See example in Figure 5 below for Farringdon, which was used to summarise the geographic split for the main packages forming the construction of the Western Ticket Hall base slabs.
Figure 5 – Sketch illustrating the breakdown of the Farringdon Western Ticket Hall base slabs (reinforced concrete) construction packages
This is also pertinent when there is a requirement to handover sections of works early to Third Parties, such as the Over-Site Developers, as was the case on several of the Crossrail contracts, including Farringdon Station.
Conclusion
There are huge benefits in breaking down the contract works at the start of the project into packages and sub-packages (bite-size chunks). These can then be progressively prepared and accepted during the construction phase, providing that assurance early, as opposed to waiting until the end of all construction works prior to starting this process. Doing the latter would invariably lead to errors, omissions, and inefficiencies, especially if key personnel have already left the project at that stage.
This paper has covered some of the process involved on the Farringdon Station contract which were used to ensure the production of construction deliverable records was as effective and efficient as it could be. These are all processes and procedures that although adopted on that specific contract, could be tailored to also suit future, multi-disciplinary projects.
However, success can only be achieved by having the right people involved and engaged from the beginning, and that means the delivery teams, inclusive of all supply-chains. The collaborative relationship between both the Contractor and Project Manager teams on the Farringdon Station contract throughout the years played a huge part on the goals achieved and cannot be underestimated.
As was noted in the introduction, comparing experiences on both the Farringdon Station project and previous, non-Crossrail projects has shown the release of personnel should also only be considered once they have handed over both (1) the physical works and (2) construction deliverable records for the work packages within their area of responsibility. In cases where this is not possible regarding item (2) [construction deliverable records], provision should be made to ensure that any partially completed records/deliverable information are made available or handed over to team members for inclusion in construction packages. This ensures that any retained knowledge is translated across into the construction records, to ensure the information handed over to the ultimate end user is as accurate as possible.
Whilst ensuring robust pans are in place from the outset to achieve the required goals in terms of certification of the works, engagement and buy-in to this from the top down, from project managers to site engineers, is also crucial in achieving these goals. This was evident at the Farringdon Station contract – from both Contractor and Project Manager sides – ensuring teams on both sides were adequately resourced and was a massive factor in the success and handover of the contract.
References
[1] Construction Certification for Civil Engineering and Station Works Procedure
[2] Procedure for Readiness Review and Certification Packages
-
Document Links
-
Authors
Chrys Chimarrides CEng MICE - Crossrail Ltd
Chrys is a NEC Supervisor’s Representative on the new Crossrail Stations. He is a Chartered Civil Engineer with over 17 years’ experience on major, multi-disciplinary construction projects, including the King’s Cross Northern Ticket Hall Project, Blackfriars Station & Bridge Construction Works, the London Olympics Legacy Works and currently on the Crossrail Project.
In the first part of his career, he worked for Principal Contractors – including a design placement – and has been working on the Client side of the Crossrail Project since 2014. He has hence acquired substantial knowledge and experience in design, construction, project management and close-out, working on both the Contractor and Client sides of the industry.