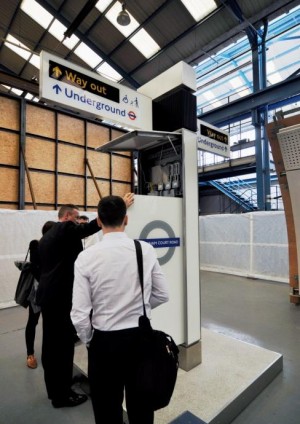
The Value of Common Design – C100 Crossrail Architectural Components
Document
type: Technical Paper
Author:
Neill McClements, ICE Publishing
Publication
Date: 03/11/2014
-
Abstract
Atkins, Grimshaw and GIA Equation form the multi-disciplinary C100 consortium for the project. Taking passenger experience as the key driver, the consortium is designing the architectural components that will be used throughout the platform and tunnel environments to create an integrated line-wide identity. Working with the individual design teams for each station, C100 have prepared ten component packages, including wall and floor finishes, lifts, escalators, lighting and signage suitable for use in all the new stations.
-
Read the full document
Introduction
The C100 team have brought practical and commercial value to the Crossrail project by maximising the benefits of common design. Simple, forward-thinking and intuitive passenger environments have governed the design, which will be completed in 2018.
Atkins, Grimshaw and GIA Equation form the multi-disciplinary C100 consortium for the project. Taking passenger experience as the key driver, the consortium is designing the architectural components that will be used throughout the platform and tunnel environments to create an integrated line-wide identity. Working with the individual design teams for each station, C100 have prepared ten component packages, including wall and floor finishes, lifts, escalators, lighting and signage suitable for use in all the new stations.
This systematic approach creates a unified passenger experience, maximises value and efficiency yet allows each station to respond to its context with an individual identity at street level.
The benefits of common design are manifold and is grounded by the following principles:
- Design efficiency
- Simplified testing and approvals
- Manufacturing and installation efficiency
- Simplified maintenance and future station upgrade
- Improved passenger experience
Fig. 1 The C100 common components to be applied to Crossrail central section stations
Fig.2 Artist impression of C100’s design for the concourse tunnel
Design Efficiency
Efficiency is articulated across the design concept. The first task for the team was to engage collaboratively with the client and the different station design teams to develop an appropriate balance between common and individual design responses for the project. Through this collaborative dialogue a design concept emerged for the central stations which provided for a high degree of commonality in the below ground spaces while allowing for a stronger individual expression at street level.
Commonality, in particular, has been maximised in the tunnel spaces where the functional brief is similar across the different stations. In contrast the street level ticket halls are subject to unique local constraints and it was deemed appropriate that each station should have an individual design response to reflect this.
Once this design approach was established C100 worked closely with C121 tunnel engineering team to further explore opportunities for the standardisation of the different tunnel geometries. More than 80 different tunnel sections across the five tunnelled stations have been reduced to nine standard sections for the platforms, cross passages, concourses, and escalator tunnels.
In addition to this, the collaboration with C121 led also to the development of the distinctive curved transitions between the different standardised tunnels. These transitions exploit the physical properties of the proposed sprayed concrete engineering lining to widen the tunnel sections locally to junctions between tunnels.
This ultimately provides a number of functional benefits. For the passenger, this assists passenger flow and improves safety by eliminating blind spots when changes in direction occur. Design efficiency is further acknowledged during the construction stage; these smooth transitions assist with the application and waterproofing of the engineering lining at the junctions between tunnels.
Fig.3 Diagram of common design in the underground levels and location specific design at street level
Fig.4 Common identity is strongest in the 5 tunnelled stations
It was decided that the rough finish to the sprayed concrete primary structural lining required a secondary cladding system in order to provide a high quality passenger environment which can be easily maintained. A lightweight fibre reinforced concrete panel system has been selected as a cost effective solution which allows the realisation of these distinctive curved transitions between tunnels. Central to this, has been the standardisation of the different tunnel sections which in turn results in standardised junctions between tunnels. The innovative standardisation of these complex double curvature geometries allows the re-use of moulds to exploit economies of scale across the stations. Similarly, the single curvature panels are set out based on standardised cladding grids across all stations driving down costs and simplifying future maintenance.
Fig.5 The use of sprayed concrete tunnel engineering (left) influences the curved tunnel transition design (right)
Fig.6 Curved tunnel transitions improve safety by reducing blind spots and creating a distinctive signature for the Crossrail tunnel environment
The resulting kit of parts, rather like a giant plumbing kit, can then be applied and adapted by the different design teams to meet the specific layout arrangements at each station.
Fig.7 A standard kit of parts
Fig.8 Diagram of standardised tunnels and junctions
Fig.9 Standardisation of tunnel cladding system
Fig.10 Zoning of technology elements (blue) e.g. Platform edge screen, totem, lighting and digital advertising
As well as developing common solutions for cladding and flooring within the tunnel environments C100 also developed, in collaboration with the station teams, a common approach to servicing the spaces, which maximised design efficiency. Servicing equipment has been zoned and focussed on a series of technology elements such as platform edge screens and services totems. These technology elements allow the de-cluttering of spaces and focus servicing equipment where it can be easily accessed. Like the tunnel finishes these have been standardised across stations to maximise economies of scale and drive further value into the project.
In addition to these major servicing elements, a common family of components such as signage, seating, gatelines and ticketing has been developed which will help to provide a coherent passenger environment across all spaces above and below ground. A standard approach to the design of these recurring finishes and components, along with the interface detailing with surrounding elements across a number of stations, significantly reduces the design resource required by the different station teams to complete the design. In light of this, Crossrail’s design management resource requirement is also reduced.
This strategy therefore leaves station teams to focus on adapting the generic kit of common elements into their designs and provides sufficient time to focus on the unique aspects of each station location.
Simplified Testing and Approvals
A major infrastructure project such as Crossrail involves a number of key stakeholders including London underground and Rail for London who will be jointly responsible for the operation and maintenance of the infrastructure when it opens in 2018. It is therefore crucial that these key stakeholders are engaged in the design process and in the selection of finishes and materials to ensure that the chosen components are appropriate for their environments.
Thorough assurance procedures therefore need to be put in place to achieve progressive stakeholder sign off through the design process. By increasing commonality across the different stations the process is aided by reducing the number of different systems and materials that need to pass through this approvals process. A vital part of this strategy is the development of samples, mock-ups and prototypes as well as the reduction in the number of mock-ups and prototypes usually developed. C100 are currently developing a range of advanced mock-ups and prototypes of the common components which brings a number of benefits. They facilitate the early testing of the concept with end users to ensure that they are fit for purpose ahead of the completion of the design by contractors. In addition to this, the mock-ups and prototypes allows further design refinement with input from specialist suppliers as well as further stakeholder and input feedback. Initiating the production of the models provides vital constructability lessons to be tried and tested, which creates assurance before arrival on site.
Once the contractors are on-board a more extensive testing regime will be required which includes surveying the components in terms of fire performance; impact testing; acoustic testing; blast testing as well as materials and finishes testing. The line-wide procurement of the common components will subsequently reduce the amount of repeat testing required for each system resulting in significant cost reductions to the project.
Fig.11 Review of totem prototype
Fig.12 Fire Equipment cabinet mock-up
Fig.13 Fibre reinforced concrete tunnel cladding prototype
Fig.14 Review of curved wall signage
Fig.15 trialling of anti-graffiti coating
Manufacturing and Installation Efficiency
Fig.16 CAD/CAM fabrication of master mould for 3D curved cladding panel
Fig.17 Production mould
Common design provides a number of tangible benefits for manufacturing and installation. Taking the concrete cladding as an example, common design, when combined with line- wide procurement of this system, can lead to significant efficiencies and cost savings for the project. The raw materials can all be purchased from a single source ensuring consistent performance and visual characteristics while capitalising on economies of scale. Tooling set-up costs at the outset of production are also significantly reduced. In the case of the cladding this could be achieved through multiple re-use of the same cladding moulds across all five stations. Whilst the cost of producing a complex double curvature mould would be cost prohibitive if this was a one off, if the mould is used to produce multiple panels then this becomes a very cost effective cladding solution for the central stations. The line-wide procurement of the common elements will mean that the contractor designed panel profiles including structural stiffening ribs and secondary fixing structure will also being standardised.
This approach allows a consistent installation methodology to be developed for all stations which can be refined through the development of mock-ups and prototypes prior to commencing the installation on site. This helps to remove risk to the construction programme by allowing any installation problems to be identified early and designed before getting to site. Efficiency is also improved through repeat working as site teams become familiar with the installation methodology.
It is worth noting that the economies of scale offered by common design makes it beneficial for the installer to invest in specialist equipment which may be customised specifically for the project. This investment will provide significant gains in terms of both productivity and the quality of the installed system.
In addition to this, site safety is also significantly improved through the increased predictability that a tried and tested installation methodology brings.
Fig.18 Finished 3D curved cladding panel
Fig.19 Trial installationSimplified Maintenance and Station Upgrade
Fig.20 Specialist equipment for cladding installation / replacement
Lasting simplicity and coherence are inherent to the Crossrail ethos. There is a symmetry between the simplicity of the installation phase of the upgrade and the future access for maintenance work on the stations.
The implementation of standardised panel sizes, profiles and fixing systems means that access methodology remains consistent across all stations. The over-arching nature of common design is highlighted in the possibility of using the same bespoke handling equipment developed for the initial installation for future maintenance requirements. Maintenance of the stations is further simplified by the introduction of a single material for floor and cladding across all tunnel spaces, for which replacements and spares can be held centrally for urgent repairs should the need occur.
As the servicing elements themselves are also a part of a common family both their maintenance and future upgrade of stations is simplified. This includes elements such as PES wall, totems, service booms and lighting. These elements have been designed as modular ‘plug and play’ systems that can allow for the quick and easy maintenance and upgrade of services which accommodate the stations’ journey into the future when new technologies emerge. As well as this, the components themselves utilise hard wearing self-finished materials which are easy to clean and are appropriate for regular handling by maintenance staff. This Common approach to servicing allows similar access & maintenance procedures to be followed across the different stations and could potentially result in one standard set of operation manuals. In light of this, maintenance staff skills will also be transferable across the five stations.
Fig.21 Cladding replacement strategy
Improved Passenger Experience
In addition to the tangible commercial and practical benefits described above, common design can play a key role in improving the overall passenger experience. The design puts people first, ensuring a highly efficient, safe and user friendly journey. Introducing commonality to similar elements across a number of stations helps to increase familiarisation and makes the environments more legible and intuitive for passengers to navigate through. These naturally intuitive environments are then supported by a common approach to the placement of key wayfinding signage which is located in a consistent manner across all stations. At a detailed level, the increased design development and refinement of products and finishes made possible through common design will create a higher quality passenger environment.
It is hoped that the completion of the Crossrail project will mark the arrival of a new world class transport environment. From a practical point of view securing raw materials from a common source and utilising the manufacturing processed will result in a consistent visual product across the different stations which will strengthen the perception that the stations are high quality environments. The repetitive use of elements that are unique to the project will also help to generate a unique and recognisable identity for Crossrail. For instance, the distinctive curvature of the flowing tunnel junctions will become an instantly recognisable motif of the Crossrail project. Similarly, the sleek aesthetic of the high technology elements such as the full height platform edge screens and services totems will help to reinforce this brand identity across both box and tunnelled stations. An additional layer of consistent finishes and components in the form of floor finish, lighting, signage, seating, speakers, and CCTV for example will further strengthen the unique Crossrail identity and provide a strong sense of coherency across all stages of the passenger journey from train to street.
Creating a timeless facility which is easy to use, manage and operate is a core value of the project. It is hoped that the Crossrail project will reinforce London’s status as a growing world city and improve the public’s view of London’s transport system. The C100 team has used the process of common design to challenge and enhance traditional railway construction, making use of current best practice, tools and techniques to contribute to an innovative and affordable railway that will be fit for the 21st Century.
-
Authors
Neill McClements - Grimshaw
C100 Lead Architect, Partner, Grimshaw