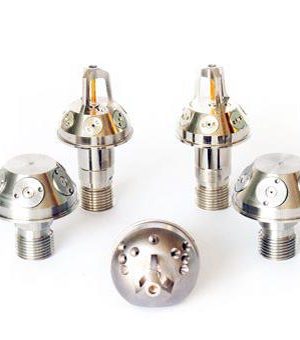
Watermist Systems – Understanding the Technology
Document
type: Technical Paper
Author:
Gerry Mullan EngTech MIFireE, ICE Publishing
Publication
Date: 09/07/2018
-
Abstract
The misunderstandings of a Watermist system during the initial stages of the Crossrail project and the subsequent designs produced which failed to meet the fundamental request to provide an engineered solution to the traditional sprinkler system leads me to explain the Watermist system in more depth.
The following aspects will be addressed in this document;
- Understanding the differences between high and low-pressure applications;
- Demonstrating how the nozzle selection makes a significant difference to the design and debunking the myth that high pressure systems use less water;
- Discussing the importance of the Fire Test Report when initially designing a Watermist system;
- Comparing historic and modern-day guidance and standards;
- Typical applications and the use of existing fire test reports;
- Watermist risk assessments and their importance in considering the correct system;
- Extinguishment, Fire Control and Suppression explanation;
- Other considerations such as extent of system, zoning and control valve locations, cause and effect, interactions with other systems;
- Documentation, manuals and certification.
Crossrail required the installation of an automatic fire suppression system as a minimum to protect assessed “back of house” rooms on the Central Stations and a reliance on fire compartmentation to mitigate the need in all other areas. Compliance to Fire Industry Association Code of Practice for the Design and Installation of Commercial and Industrial Watermist Systems and BS 8489-1 Commercial and Industrial Water Mist Systems, LU 1-085 and Sub-surface regulations, amongst others.
The provision of inconsistent designs across the central section and the discrepancy in types of rooms, locations and extent of suppression provided in the designs will be discussed.
The paper will discuss the factors mentioned above and perhaps simplify guidance for similar future projects.
-
Read the full document
Introduction
At the project’s inception, there was no definitive British Standard in place and reliance was based on the Fire Industry Association (FIA) Code of Practice for Commercial and Industrial Watermist Systems. This fulfilled, at the time, an urgent need in the fire safety community and provided the first definitive guidelines on the safe and effective use of Watermist technology which will enable clear guidance to be given by fire safety decision makers.
This Code of Practice gave recommendations for the design, installation, commissioning and maintenance of Watermist systems, and gives performance criteria for fixed Watermist systems for specific commercial and industrial hazards.
The Water Mist design procedure was based on the following Crossrail key statements:
- The room/space will be newly constructed, with no pre-existing conditions;
- The fire strategy was prepared for the station; which identified all non-compliances and fire engineering solutions; and
- Management procedures recommended or assumed during the process was noted on the room specification form with the Infrastructure Manager and Operators consulted to ensure personnel, training and support was available.
A library of risk assessments undertaken were used to share best practice and commonalities across the assessments.
The Fire Precautions (Sub-surface Railway Stations) Regulations 2009 clause 5 states;
Means for fighting fire
5.— (1) Paragraph (2) applies to these parts of station premises—
(a) a room containing any electricity generator, transformer or switchgear, other than one in which any machinery for operating an escalator, passenger conveyor or lift is installed;
(b) any storage area, including an area set aside for storing refuse pending its disposal; and
(c) any part of the premises used as a shop.
(2) The parts to which this paragraph applies must be provided with a means for fighting fire comprising a system which is activated automatically in that part of the premises in case of fire in that part.
Reference to the Crossrail Programme Functional Requirements (CPFR) document was also key in the initial design of the Watermist system as Table 1 outlines:
Table 1 – Crossrail Programme Functional Requirements
CPFR Ref: Clause 4988 Appropriate good industry practice asset management shall be employed in the development of Crossrail to derive optimal maintenance activities, tasks and frequencies. 5020 The design of Crossrail infrastructure, assets and systems shall optimise whole life cost requirements in accordance with the Whole Life Cost Principles. 5290 The design of assets and the selection of systems and components shall minimise the number of spare part types that will need to be held. 4990 The design shall minimise the impact on the environment of the maintenance, repair and renewal of Crossrail assets and systems. 4995 Due regard shall be taken of all & any specialist or bespoke maintenance regimes or arrangements when designing and integrating Central Operating Section systems to pre-existing ones. 4996 All systems or sub-systems shall be maintainable end-to-end by the relevant Infrastructure Maintainer. 4998 The designs shall minimise the number of assets and systems that will require specialist inspection, maintenance and repair skills. 5025 The designs shall, so far as is reasonably practicable, eliminate components which cannot be inspected, maintained or renewed without removing other components. 2042 Water supplies shall be provided by utility companies for both domestic purposes and sprinklers/fire mains. 2043 Where sprinklers/fire mains are supplied they shall be fed via a dual supply arrangement, so that in the event of failure in one source there shall be an alternative supply. For a fire to survive, it must rely on the presence of the three elements of the ‘fire triangle’: oxygen, heat and combustible material. The removal of any one of these elements is enough to suppress or extinguish a fire.
While traditional water sprinkler systems remove only the heat element of the triangle, Watermist systems remove both the heat and oxygen elements by dispersing water through specially-designed nozzles.
The smaller the water droplet sizes are, the larger the surface area becomes per litre of water and thus the more effective the system is in rapidly reducing the temperature of a fire. To put it another way, when water is converted to steam – which is what happens to the water droplets in water mist – then a large amount of energy is taken from the fire, which results in rapid cooling.
Figure 1 – Crossrail Acceptance Criteria?
Because of their proven effectiveness in fighting fires, Watermist systems have become increasingly popular in land applications.
First to the market were high pressure water mist solutions, but low-pressure systems are increasingly preferred by owners and authorities. It must be noted that the first nozzle appeared as early as 1870 by Fogtec©.
Key Requirements
Understanding the differences
Watermist, is designed as a risk specific system and dependent upon the fire testing analysis and not a generic fire system to be designed from “a set of written rules”.
However, there remains a misperception that low pressure water mist systems use more water than high pressure systems. But approval data published in DNV EXCHANGE demonstrates that there is very small difference between the systems and that low-pressure systems can even use less water on occasions.
Another misperception is that low pressure systems can cause more damage to electric and electronic equipment than high pressure systems. In fact, cabinets and cables may be better cooled by the larger water mist droplets.
Object protection
An object protection system is used to protect stand-alone equipment, such as diesel engine generator and deep fat fryers, by discharging water directly onto the fire risk by local application.
Volume protection
Volume protection systems are used to discharge Watermist throughout the entire protected area using open nozzles or closed; automatic ‘heat sensitive’ type nozzles where only the nozzles in the immediate vicinity of a fire are expected to operate.
Low pressure Watermist systems
These systems have been designed to retain all the proven performance and reliability of traditional water-based systems, while capturing the efficiency of small water droplet, Watermist technology.
The design of the nozzles provides reduced droplet sizes of 0.10mm diameter at a pressure of less than 12.5bar to deliver a typical flow of just 12 litres (2.6 gallons) per minute from each nozzle. The result is reduced pipe diameters, ease of installation, less system weight and minimal water discharge. Low operating pressure also provides the option of using either copper or plated carbon steel pipework, as alternatives to stainless steel.
Low pressure frangible bulb systems ensure that only those nozzles operate which are in the immediate vicinity of the fire. They are ideally suited for the protection of rooms, corridors and spaces where light-to-moderate fire loads of ordinary combustibles exist. Low pressure open nozzle systems are ideal for the protection of hazards involving flammable liquids. Open nozzle systems are not applicable to the Crossrail project.
High pressure watermist systems
The average total surface area of the droplets in the mist from a typical high-pressure water mist system is at least 100 times greater than conventional sprinkler droplets for the same volume of water. Therefore, significantly smaller amounts of water are required to absorb an equivalent amount of energy from a fire.
Oxygen depletion is significantly increased by high pressure Watermist at the flame front in both object protection and total flooding applications within completely enclosed spaces, particularly where the fire is large in relation to the space.
Wetting of surfaces is also an important effect where control of deep-seated fires is a prerequisite. A further highly beneficial effect of high pressure water mist is the dramatic reduction of harmful products of combustion caused by the washing out of smoke particles from the fire.
Nozzle Selection
Nozzle specifications are central to the performance of the water mist system, to ensure correct coverage and fire protection.
Watermist systems will typically discharge significantly less water than traditional sprinkler systems. For many applications, this is an advantage both in terms of the design requirements of the system and the reduced potential for water damage in the event of a system operation.
Key features of a Watermist nozzle are as follows;
- Cooling ability enables installation of a glass window in the fire door
- High spacing
- Few nozzles – architecturally attractive
- Efficient cooling
- Window cooling – enables purchase of cheaper glass
- Short installation time
- Aesthetic design
The nozzles shown below are used in high-pressure applications.
Figure 2 – High Pressure Application Nozzles
The nozzles shown below are used in low-pressure applications.
Figure 3 – Low-Pressure Application Nozzles
Fire Test
Historically, different systems have been tested and demonstrated to be effective against many specific applications. A few examples include their use in cabins on board ships, in machinery spaces or for specific localised protection of objects.
Table 2 – Questions Explored on Crossrail
Ref: Question 1 The basic design and installation parameters of all Watermist systems should be obtained from performance tests – has this been conducted? 2 Performance test procedures may be generic to a certain fire hazard, in which case first principles can be applied, or they may be particular to a specific application within a fire hazard – would this be applicable? 3 What are the possible fire hazards and has a fire protection engineering evaluation of the fire hazard, the compartment conditions, size and the performance objectives been considered? 4 Have the fire tests been developed, carried out and interpreted by qualified fire testing laboratories? 5 What are the likely ignition sources and how could they be mitigated? 6 Should a fire occur within the area/space, is flashover likely to occur? 7 Could evidence be provided to confirm that a generic fire test procedure would cover a Crossrail fire hazard? When a Watermist system is tested for the purpose of fire extinguishment, attention should be given to maximizing the probability of fire extinguishment in real applications. One way of doing this is to test against several fire and ignition scenarios, and to use a broad range of
Watermist system assessment parameters to find out the optimum choice of parameters to be measured and recorded. The performance objective for the Watermist system undergoing the tests should be recorded.
The main fire performance objective of the Watermist system under test should be evaluated in terms of fire extinguishment, fire suppression or fire control, as appropriate for the volume or object to be protected.
Table 3 – Crossrail Watermist Procedures
Evaluation Fire Test Parameters The evaluation of the fire hazard should result in a list of possible fire scenarios, which are grouped to determine the test fires that are required. The test fires should be defined at least in terms of Fuels – type and quantity (wood, plastics, cable, flammable liquid, gas, etc.)
Arrangement (crib, pile, shelved storage, pool, flowing fire, spray, etc.)
Size (dimension of the fuel array, area of the pool or flow rate of a flowing or a spray fire and degree of enclosure)
Obstructions to Watermist and Ignition source
Ventilation and air movement
From fire dynamics point of view, the term “compartment conditions” is primarily related to whether the fire is freely-ventilated (fuel controlled) or ventilation-controlled (an enclosed fire). These conditions should be replicated in the test enclosure. Enclosure dimensions, particularly height and configuration
Air exchange rate, vent dimensions, position, and orientation
For freely-ventilated and ventilation-controlled fires, the ambient conditions (temperature, moisture, air flow) surrounding the hazard, and the fire resistance and tightness of structures close to the hazard, should be evaluated
The main fire performance objective of a Watermist system should be evaluated in terms of fire extinguishment, fire suppression or fire control, as appropriate for the volume or object to be protected. Other parameters that may be used to evaluate fire performance include Structural integrity
Damage to sensitive equipment or systems
Smoke and water damage
Visibility
Tenability
The Watermist system should be operated in the tests using: Maximum nozzle spacing
Maximum ceiling height or maximum distance of nozzles to hazard
Minimum design pressure at nozzles
Additives, as intended to be used in real installation
Relevant obstructions close to nozzles such as a simulated false ceiling, joists, beams or heating, ventilation or air-conditioning ducts
To fully determine the limits of the installation parameters, fire tests should also be conducted using Minimum nozzle spacing
Minimum ceiling height or minimum distance from nozzles to hazard
Maximum design pressure at the nozzles
As stated previously, critical to the successful operation of a Watermist system are the system design details. Of equal importance are the building design details – the fire loads, obstructions, ventilation, ceiling height, compartmentation and openings in the protected space. These design details need to be fully addressed in both the fire performance tests and installed systems to ensure their effectiveness.
Considerations
The equipment should be acceptable for use as according to BS 8489 Part 1:2016 Table 1 (formerly DD 8489 as defined in the Crossrail Baseline standards); Occupancies and acceptable fire test protocols for an automatic Watermist system*, which denotes BS 8489 Part 7:2016 and FM 5560 Appendix G:2016 as the test protocols.
* Specific areas within buildings can be protected by Watermist where relevant fire test protocols exist, which would point to VDS 3811, DBI Danish Fire and Security Technology or equivalent if relevant.
It can be seen from the above-mentioned documents that Watermist is seen by all standards institutes as risk and fire test specific and stepping outside these “controls” would be at the designers own risk.
Typical Applications
Light Hazard applications are defined as areas with low fire loads and low combustibility and with no single compartment greater than 126m² and with a fire resistance of at least 30 mins.
Schools, Prisons and Hospitals are examples of a light hazard application.
Ordinary Hazard applications are defined as areas with medium fire loads and medium combustibility or where products of medium combustibility are manufactured or processed.
With Watermist, Ordinary hazards are sub divided into 2 groups.
Ordinary hazard group 1 applications are generally classed as Hospitals, Hotels, Libraries, Restaurants, Schools, Offices and Data Processing Centres.
Ordinary hazard group 2 applications are generally classed as Fire Stations, Bakeries, Museums and Car Storage facilities.
Risk Assessments
Before designing a Watermist system, the volume, occupancy or object to be protected should be identified and a hazard analysis carried out to establish the exact nature of the potential fire hazard(s) affecting that volume, occupancy or object. If enhanced availability is required for volume protection systems, then the recommendations in BS 8489:2016 Annex B should be followed.
This process specifies requirements and gives information on
- Basic design – designer Program of Requirements;
- Detailed design – installation design;
- Installation and delivery;
- Maintenance
This in turn gives criteria for the acceptance of fixed Watermist systems for specific hazards and provides fire test protocols for a variety of hazard groups.
The outcome of the process shall be an installation with a scope for:
- Fire extinguishing;
- Fire suppression;
- Fire control.
The Watermist installation shall have a defined application such as:
- Local Application Systems;
- Total Compartment Application Systems / Volume protection;
- Zoned Application Systems.
Water mist systems have been utilised where suppression is required and the following applied:
- A sprinkler system cannot be used due to water supply restrictions;
- A sprinkler system is not considered viable due to practical or logistical constraints.
The possible residual risk shall be determined for the intended scope and application.
In case a scope and application is only partly suitable, the level of residual risk shall be quantified.
The owner / user shall be informed explicit about this residual risk and shall be made aware about this residual risk.
Fire Control, Suppression & Extinguishment
The Watermist system creates a mist of fine water droplets. Droplets in variable sizes circulate in the airflow, suppressing the supply of oxygen and absorbing the heat energy. It that way it breaks the chain of combustion.
Water is an effective agent for firefighting as it is readily available and environmentally friendly. When water is added as mist it is most efficient at reducing and dissipating heat and thereby controlling, suppressing and extinguishing a fire.
Table 4 – Types of System
Type of system Duration Fire Tests Suppression & Fire Control Minimum storage capacity using automatic nozzles, the duration should be commensurate with the nature of the occupancy as defined in Table 1* and should in all cases be not less than 60 minutes depending on the risk. Table 1* Extinguishing Using open nozzles, the water supply should be based on the minimum discharge duration given in Table 3*, and the maximum dimensional and area coverage including spacing of nozzles as established by the tests listed in Table 2*.
Using automatic nozzles, the duration should be at least twice the time taken to extinguish the fire and to prevent re-ignition as established in the fire test report
Table 2*
Table 3*
* Referring to BS 8489-1:2016 Based on the low fire load, robust compartmentation and fire control in conjunction with London Fire Brigade, the minimum storage capacity remained at 30 minutes as to the baseline standards.
Further information is provided in table 5 below:
Table 5 – Baseline Standards
Suitability of equipment
Low pressure systems have simpler piping requirements and less risk of clogging. Using a common pump unit and control system, makes it easier to operate and maintain. Furthermore, low pressure systems have lower power requirements than high pressure ones, providing a further potential saving in emergency generator costs.
All water mist systems must pass the same performance-based tests according to accredited certification bodies. As a result, there can be no difference in the extinguishing efficiency between low pressure and high-pressure systems.
As a substitute
Watermist systems are increasingly being considered and used for the fire protection of buildings, including offices, hotels and other commercial premises.
Watermist technology is selected by many in the fire industry as a space saving solution and systems may also offer additional environmentally attractive design. Different Watermist systems operate at different system pressures between about 3 bar and 120 bar or more. Watermist systems can suppress fires by wetting, cooling and through localised oxygen displacement (by conversion of water droplets into steam in the flame zone).
Calculations
All calculations describing proposed works and referencing drawings would be approved by the Fire Engineer, before procurement of all relevant materials. System piping shall be fully hydraulically designed, taking into consideration the entire piping system, to deliver the minimum required water flow and pressure to the assumed maximum area of operation (AMAO). This would include the following;
- Friction Loss
- Flow Rates
- Thrust
The k-factor formula is the start of all hydraulic calculations for fire protection systems for both manual and computerized calculations and is also required for the checking of both types.
The discharge from a Watermist nozzle can be calculated from the formula below:
when q = flow in L/min
k = nozzle discharge coefficient or k-factor for head in Lpm / bar0.5
p = pressure in bar
This formula can be rewritten to give us:
Friction loss in pipe can be calculated using the Fire Protection industry standard Hazen Williams formula: –
When
p = pressure loss in bar per meter
q = flow through the pipe in L/min
c = friction loss coefficient
d = internal diameter of the pipe in mmGalvanized steel pipe has a friction loss coefficient of 120.
If the system is outside the normal pressure and flow range or the system is to use additives, or will be subject to unusual temperature conditions then the Darcy Wisbech equation may be more appropriate.
Velocity in pipe can be calculated using the following formula:-
Positioning and Spacing
The system was required to be installed in easily accessible areas for repairs and alterations.
The pipework was not to be embedded in concrete floors or ceilings or where possible in concealed spaces that make inspection, repairs and modifications difficult.
Example below showing nozzles covering the void area;
Figure 4 – Nozzle Positioning
Materials
Please refer to BS 8489-1:2016 Annex A for the main elements of a Watermist fire suppression system. All materials should be made of corrosion-resistant material.
Drain Valve
Shall be provided immediately downstream of the water flow alarm switch on each zone and control valve and any area where the system could have trapped water.
The valve shall be made of corrosion-resistant material and adequate provision shall be made for the disposal of waste water.
Stop Valve
All stop valves controlling the flow of water to Watermist systems should have an open/shut indicator and shall be securely fastened by strap & padlock in the operational mode. Furthermore, valves should have the facility to be monitored by supervisory switches to provide remote indication of their status.
Control Valve
Control valves should be in accordance with the acceptance criteria of BS EN 12259-2 or BS EN 12259-3 or equivalent.
Check Valve
Control valves should be in accordance with the acceptance criteria of BS EN 12259-2 or BS EN 12259-3 or equivalent;
Test Valve
The test facility shall simulate operation of any single automatic Watermist nozzle;
Pipe & Fittings
Very small unobtrusive stainless-steel pipes are generally used due to their corrosion resistance, fire properties and smooth internal bore;
- Nozzle arm piping is normally from 10mm – 22mm (Sprinkler typical 25mm – 50 mm)
- Distribution piping is typically from 22mm – 38mm (Sprinkler typical 65mm – 100 mm)
- Main piping is typically from 38mm – 63mm (Sprinkler typical 100mm – 200 mm)
All pipework and equipment that may be subject to temperatures below 4º C should be insulated and trace heated to protect against freezing. The trace heating panel should also be monitored for faults by the fire alarm system.
Supports
Pipework supplying Watermist systems (high and low) are subject to relatively large forces, caused by activation pressures when the nozzles are opened. Therefore, the pipe supports and fixings to be used for this purpose must be carefully designed and installed to resist the forces, i.e. restraint supports as shown below.
Figure 5 – Pipe Supports and Fixings
Equipment
- The water quality shall be demineralized water, deionized water, wholesome or sweet industrial water;
- Water supply equipment shall be housed in buildings or sections of premises used for no other purpose than housing fire protection systems. The water supplies, stop valves and control valves should be installed such that they are safely accessible even in a fire situation;
- The durations should be based on the hydraulically most favourable operating areas, i.e. those areas where the maximum flow would be delivered;
- Shall be protected against the effects of frost and maintained at a minimum temperature of 4 °C;
- Tanks shall be monitored for water level and protected against the risk of freezing;
- Sectional tanks to have external flanges;
- Pumps shall be designed to start both automatically and manually, be of sufficient capacity (flow and pressure) to achieve the necessary pressure and duration and be rated at 110% pump
- power demand;
- Pumps shall be equipped to ensure a continuous flow of water through the pump to prevent overheating when operating against a closed valve;
- Where there is more than one pumpset installed, the suction pipes should be interconnected with means to exclude one pumpset without affecting the other;
- Power supplies to the pump controller should be solely for the use of the Watermist pumpset and separate from all other connections and/or taken from a connection from the main switch.
Figure 6 – Watermist Systems Key Components
The schematic above shows some of the key components in a Watermist system and do not represent actual systems required for Crossrail applications – this was the designer’s responsibility.
Learning Legacy
The Fire Strategy and Fire Risk Assessments for the Station will almost certainly necessitate some deviations from the recommendations in the current British Standard. They should always be discussed and agreed with the authority having jurisdiction and the local fire and rescue service.
The generic design principles that required discussion were:
- Making sure the Watermist system can be accepted by the Infrastructure Manager?
- Low pressure frangible bulb systems ensure that only those nozzles operate which are in the immediate vicinity of the fire. They are ideally suited for the protection of rooms, corridors and spaces where light-to-moderate fire loads of ordinary combustibles exist.
- Fault rectification kept to a minimum by utilizing standardized components and adequately “zoning” areas into maintainable sections.
- Pipes and fittings shall be installed in such a way that the pipework is not exposed to damage, e.g. by fire, by passing vehicles, by frost, or by contact with dissimilar metals.
- A water mist system that can be considered as equivalent to a traditional sprinkler system and therefore should also be inspected accordingly.
Conclusion
The uniqueness of water mist is that it combines the suppression effect of gas and traditional sprinkler systems. As well as removing the oxygen like a gas system, it simultaneously cools the fire like a traditional sprinkler. The cooling effect additionally lowers the risk of re-ignition.
For many in the fire industry, Watermist systems will continue to offer an alternative to more traditional sprinkler systems. The progress being made now has the potential to result in robustly tested and certified water mist systems for low hazard commercial premises. This will help to provide confidence to Transport for London that a Watermist system was suitable for the intended application to which it is being installed.
The Watermist contractor must provide a copy of their ‘Watermist Design and Installation Manual’ that contains all the design and installation rules for the referenced system.
- Misinterpretation of systems that are designed and tested for suppression or extinguishment – CRL have areas requiring fire control (suppression) due to the low fire load and the relatively fast response times for the London Fire Brigade.
- Cylinder systems were originally specified for Crossrail which never took into consideration the logistics, shelf life, pressurised equipment, low water supply storage and most importantly; the minimum flow and pressure required for a successful fire test should be met or exceeded by all the nozzles in any area of operation. If the fire test is passed using a constant pressure source then a decaying pressure source should not be used, and vice versa – cylinder systems are defined as a decaying pressure source.
- Misinterpretation of which areas require protection and compliance with BS 8489 Part 1:2016 – the selected system was “volume protection” which concludes where the spread of fire is likely to involve two or more enclosed volumetric spaces, account should be taken of adjacent fire hazards, and the Watermist system should be designed for the combined hazard.
Bibliography
- Fire Safety Engineering Principles CRL1-XRL-E1-GTA-CR001-00001
- Crossrail Programme Functional Requirements CR-XRL-Z-GPR-CR001-00004;
- Volume 2B – General Requirements Part 29 – Contractor’s Design, Assurance, Records and Certification CRL1-XRL-R-GPD-CRG03-50001;
- Designing for Health & Safety Procedure CR-XRL-Z7-GPD-CR001_Z-50002;
- FIA Code of Practice for the Design and Installation of Commercial and Industrial Watermist Systems 2008;
- BS EN 12259 (all parts), Fixed firefighting systems – Components for sprinkler and water spray systems;
- The Fire Precautions (Sub-surface Railway Stations) (England) Regulations 2009;
- BS 8489-1, Fixed fire protection systems – Industrial and commercial Watermist systems – Part 1: Code of practice for design and installation;
- BS 8489-7, Fixed fire protection systems – Industrial and commercial Watermist systems – Part 7: Tests and requirements for Watermist systems for the protection of low hazard occupancies;
- BS EN 15004-1:2008, Fixed firefighting systems – Gas extinguishing systems – Part 1: Design, installation and maintenance;
- FM 5560:2016, Approval standard for water mist systems;
- LPS 1283, Loss prevention standard – Requirements and test methods for the approval of Watermist systems for use in commercial low hazard occupancies;
- BS EN 13501-1:2007+A1:2009, Fire classification of construction products and building elements – Part 1: Classification using data from reaction to fire tests;
- Risk Management Guidelines
- IWMA Newsletters/Position Papers
Acknowledgements
- Danish Institute of Fire and Security Technology
- UPTUN Guidance Engineering Guidance for water-based fire-fighting systems for the Protection of Tunnels and Subsurface Facilities
- Canute LLP
- Stein Lovskar, Commercial Development Manager, Survitec Group
- Fire Industry Association
- Loss Prevention Council
-
Authors
Gerry Mullan EngTech MIFireE - Crossrail Ltd
Gerry worked in the Crossrail MEP team until July 2017