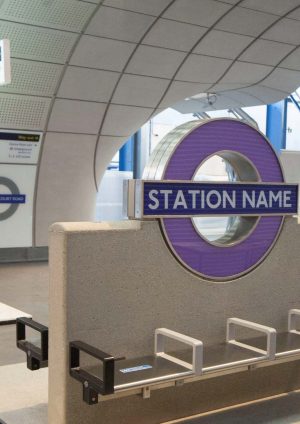
Client Advice and Technical Services to Chief Engineer’s Group
Document
type: Technical Paper
Author:
George Stowell BA(Hons) Dipl Arch MA(Dist) MRIAI RIBA, ICE Publishing
Publication
Date: 09/07/2018
-
Abstract
Between early 2013 and 2018, CEG worked with Crossrail’s programme delivery function and station contractors on station design development and progressive acceptance that requirements were met. In addition, they led the performance verification programme for C100 designs. C100 provided support in both areas of work as they related to eight sub-surface central London station fit-outs. C100 had previously completed the employer’s architectural design intent and in-use strategy for access, maintenance and replacement to sub-surface areas[1] in 2011.
This paper includes reference to, and is complimentary to, previous papers about Crossrail’s sub-surface station design intent by McClements[2] and early stages of Crossrail’s performance verification programme by Moxon and Atherton[3]. Both were written before contractor award stage in 2012, and commencement of the full verification programme in 2013.
To a large extent the professional services were determined by the project context of sponsor involvement, Crossrail’s engineering design management strategy[4], and design vision[7]. The project introduced a new and novel rail type and service standard to the infrastructure maintainer (IM), Transport for London. For example, Crossrail trains run on high voltage 25kv AC overhead lines in tunnel diameters 50 per cent greater than existing ones, and sub-surface public areas which are twice the size and have twice the capacity for passengers. This project context required a highly structured and adaptable approach for achieving the following:
- Certain operational value at opening and over the lifecycle
- World-class passenger experience
- Value for money from construction stage investment.
This paper describes what C100 did between 2014 and 2018 and how it worked, offering recommendations and lessons learnt for project planning and execution on future major projects.
-
Read the full document
Overview
Purpose
This paper explores the value of, and lessons learnt, from client advice and technical services provided to Crossrail’s Chief Engineer’s Group (CEG) by C100 Framework for central London stations during the contractor design and build stage. Services commenced in 2014 and concluded in early 2018 when site benchmarks were accepted by CEG from contractors. The author and reviewers conclude that this paper contains a useful insight into the combination of adaptable project arrangements, mix of deliverables, client expertise and proposals for a new quality standard for public use infrastructure projects to enable design quality, technical performance and in-use stage success.
Executive summary
Between early 2013 and 2018, CEG worked with Crossrail’s programme delivery function and station contractors on station design development and progressive acceptance that requirements were met. In addition, they led the performance verification programme for C100 designs. C100 provided support in both areas of work as they related to eight sub-surface central London station fit-outs. C100 had previously completed the employer’s architectural design intent and in-use strategy for access, maintenance and replacement to sub-surface areas[1] in 2011.
This paper includes reference to, and is complimentary to, previous papers about Crossrail’s sub-surface station design intent by McClements[2] and early stages of Crossrail’s performance verification programme by Moxon and Atherton[3]. Both were written before contractor award stage in 2012, and commencement of the full verification programme in 2013.
To a large extent the professional services were determined by the project context of sponsor involvement, Crossrail’s engineering design management strategy[4], and design vision[7]. The project introduced a new and novel rail type and service standard to the infrastructure maintainer (IM), Transport for London. For example, Crossrail trains run on high voltage 25kv AC overhead lines in tunnel diameters 50 per cent greater than existing ones, and sub-surface public areas which are twice the size and have twice the capacity for passengers. This project context required a highly structured and adaptable approach for achieving the following:
- Certain operational value at opening and over the lifecycle
- World-class passenger experience
- Value for money from construction stage investment.
This paper describes what C100 did between 2014 and 2018 and how it worked, offering recommendations and lessons learnt for project planning and execution on future major projects.
Recommendations
Three recommendations have been drawn from C100’s experience between 2014 and 2018.
1. Value from mock-ups, prototypes and performance testing
Use of client-side pre-construction stage designs in the form of full scale development mock ups, samples, working prototypes and testing would add value to many major projects, especially those involving design and build procurement. Evidence gained would form the bridge between client requirements communicated in drawings, BIM and performance specification, and the contractor design and build stages. During early stage employer’s design development, relevant information from tangible, realistic design tools can inform the right investment mix to deliver the project specific outcomes. These include productivity, sustainability, operational cost, energy use, fire and security performance, equally accessibility, operator welfare and safety. During design and build stages, demonstration of regulatory and requirement compliance, and confidence in achieving outcomes can also be made. In both stages, symmetric information between client and contractors can help build trust necessary for collaborative and productive working.#
2. New British Standard for outcome delivery
Development of a new British Standard or Code of Practice is recommended for mock-up, samples, prototype and testing development on major built environment projects. The standard would be compatible with RIBA Plan of Work 2013 and existing building information management, sustainability, procurement and quality assurance documents. It would assist clients, building designers and contractors, improving levels of confidence and certainty about operational stage outcomes including: a shared language and structure as to how to go about such work, and give project decision makers a tool to use when planning outcome based investment.
3. Using the optimal amount of design information
Quality and value on public sector major projects will be determined by client decisions, briefing and ongoing direction from the right mix of design information to use at each project stage. Each set of design information will contain the level of complexity and resolution appropriate for the project stage. The identified sets are:
- Set one: drawings and BIM models with innovative computer technologies
- Set two: mock-ups, samples and prototypes with testing
- Set three: performance specification with or without prescriptive elements.
Clients should brief design teams, contractors and their supply chain on what is the right mix of information and resolution expected at each project stage, enabling effective resource allocation for design thinking, decision making and effective use of information.
Fit out design strategy
Outline of intended fit-out design strategy
At central London stations, Crossrail undertook three stages of building and fit-out design development. The design and procurement plan from 2008 was for directly appointed station design teams to create a full engineering design at RIBA F1. This was to form the employer’s design intent with operational value strategies.
In 2009, C100 were appointed to design a common set of architectural and engineering components for sub-surface stations[8], passing the completed information set to station designers for integration in station specific conditions. Integrated station designs were then to be tendered to contractors for contract award in 2012. This allowed a holistic fit-out design for each station, including surface and sub-surface areas, with benefits for safety and operational value though standardised components and details with consistent material quality and servicing locations.
The design and procurement plan that emerged between 2010 and 2011 is explained in more detail in the three sections below. It involved retention of the employer’s civil engineering and structural designs, and different levels of resolution between station designs and C100’s common components. In addition, the station contracts didn’t include obligations for cross station design liaison, co-operation or resolution.
Employer’s reference design intent stage – 2009 to 2011
Individual station teams designed ticket halls and urban realms that related to the local London context. C100 team was briefed to design a unified family of products and systems, creating a line-wide Crossrail identity. It is the design of common components in central London stations that are discussed in this paper. The majority of C100’s scope involved elements unavailable in the marketplace because they couldn’t meet requirements. The skillsets needed to design the common components included architectural, engineering, product, wayfinding, mechanical, electrical and public health design for the following:
- Platform edge structure
- Lighting suite
- Public area tunnel cladding
- Signage suite
- Wayfinding panels
- Poster frames
- Communication equipment housings
- Totem structures
- Flooring and skirting
- Platform end walls
- Platform equipment cabinets
- Public area seats
- Balustrades and handrails
- Passenger help point
- Advertising
- Clock
- Lift interiors, escalator cladding.
Architectural station designs were completed in 2011 at RIBA Stage E, with C100 sub-surface designs at RIBA F1. C100’s work also involved co-ordination with employer’s civil engineering design teams. Tunnel sizes were standardised (Figure 1), the quantity of tunnels was reduced and modularisation was optimised, all driving economies of scale in the civils construction work, fit-out construction and in-use stages[9].
Figure 1. Standardised sub-surface station engineering tunnel with simplified intersections.
Station and sub-surface fit-out designs were integrated at the top of the escalators at ticket hall level by station designers (Figure 2).
Figure 2. Design concept longitudinal section (C100 scope in green)
(Dark pink and dark purple tones illustrate upper level, location specific designs. Ticket hall interface shown at top of escalators)
Crossrail’s design strategy between 2013 and 2016 also included CEG’s performance verification programme[10] for C100’s scope of work. Except for where sub-components contained their own Intellectual Property, IP resided with Crossrail. Both sets of designers concluded their work, that was incorporated into the station works information for tender and contract award, in 2012[11]:
- Performance specification
- Drawings and schedules
- BIM models
- Safety deliverables
- Access, maintenance and replacement strategies
- Specialist design and performance design guidance reports
- Sample, mock-up, prototype and benchmark schedule.
Crossrail’s performance verification programme – 2013 – 2016
The programme set out to prove to Crossrail and the IMs that key requirements in C100’s 2011 intent could be met in advance of the contractors’ design phase. CEG’s performance verification programme evolved from pre-tender mock-ups and material testing[12] to a wider set of work involving nearly the full C100 design intent scope (Figure 3). The purpose was as follows:
- Proof of concept design performance to Crossrail and the IMs
- Improve the employer’s C100 design
- Reducing complexity for operational functionality and safety
- Reference point for contractor design proposals
- Production of design guidance to facilitate contractor designs
- Selection of materials and suppliers.
Outputs were especially useful in creating robust client evidence for the achievement of a common approach for passenger experience and operational value. The programme involved the following design tools and techniques:
- BIM and CAD modeling, use of 3-D printing
- Material sample and mock-ups
- Working prototypes and testing
- Ergonomic user group testing
- Operation and maintenance evaluation
- Performance testing by accredited facilities.
Figure 3. Examples of C100 prototypes at Crossrail’s test facility
Information from this stage was instructed to the contractors in the form of ‘revised designs,’ ‘lessons learnt reports’ and ‘design guidance’ to facilitate common, consistent designs across all eight stations.
Contractor design and build stage – 2013 – 2018
Contractors began designing in early 2013. To demonstrate final designs would perform as intended, off site prototypes and on-site benchmarks were executed during the design development process. They included verification programme knowledge and ensured many material quality, operational aspects, and safety requirements were resolved. Most of the detailed station design and contractor prototyping work was undertaken with the contractors’ supply chains in a phase between 2014 and 2016 (Figure 4), satisfying CEG and IMs that the concepts and products were proved, ready for benchmarking, manufacture and site installation.
Figure 4. Prototype of Central London station tunnel cladding by contractor
During this stage, C100 provided client advice and technical support services to CEG’s central function and CEG site architects. It was important that C100’s service offered impartial advice to CEG about the contractor’s designs, ensuring there was no conflict of interest, guidance could be seen to be trustworthy and it was equally valuable at all stations.
Lessons learnt – value of early stage outcome evidence
The delivery of an infrastructure project with pre-known and well understood passenger experience and operational value is best undertaken by reference to the right mix of client information provided early in the design process, for example, drawings, computer modelling and tangible evidence. Insight from C100’s experience is that intensive use of drawings and computer technologies are of most value to the experts and designers in the design process. Tangibles in the form of mock-ups, prototypes and full-scale testing are most useful for those with less knowledge, or those with less time at the early point in the design process; usually the operator, user and specialist sub-contractor. The lesson here is that whilst public sector guidance for major projects identifies value from a greater quantity of design work earlier, in the form of building information management and computer aided design, the C100 experience it is that a wider variety of carefully selected design tools, including drawings, 3D modelling, mocks ups and prototypes are more useful earlier.
Construction procurement strategy
Risk and benefits management
Successful outcomes resulting from any building or infrastructure investment require a well-structured, competent client for effective decision making and efficient utilisation of resources. At contract award stage in 2012, a core part of Crossrail’s procurement approach[13] was to manage cost and programme risk for station fit-out by employing single station contactors to undertake design and construction. The revised approach was not the original one described in 2.1, but was one that emerged to give high confidence about outturn cost and programme. It fitted the professional knowledge base for this purpose but introduced a series of challenges and residual risks. To a large extent the 2012 approach still addressed original causes of project risk resulting from:
- Inherent complexity
- Unpredictable events
Using the station works information, Crossrail’s site engineering managers led day-to-day design and programme management, supported by CEG central and CEG on-site representatives. Crossrail’s site teams were tasked with delivering on time, on budget and to the quality required. In the main they managed unpredictable events. Four original causes of project risk remained:
- Newness, context or technologies
- Asymmetric information
- Stakeholder dynamics
- Technical compliance
CEG was the point of contact with the IMs for technical performance, operational value and passenger experience. Working with the central programme directorate, CEG undertook risk and benefits management in these categories supported by C100 for public sub-surface areas. Newness and asymmetric information risks were, in the main, addressed by sharing pre-construction client prototyping evidence with IMs and station contractors. Stakeholder dynamic risks were addressed by CEG acting as the conduit for, and management of, IM requirements.
Technical compliance of contractors’ designs for operational certainty at opening was again a core CEG function, realised though site presence and the technical assurance role.
Residual risk from contractor procurement
Project risk in the form of operational inconsistency and poorer passenger experience resulted from the lack of contract obligations for common detailed design, and differing levels of design resolution in the fit-out design intent. These residual risks emerged from the single station procurement decision. Both required mitigation to achieve the employer’s intent in the form of the performance verification programme, CEG’s work on accepting designs and through C100’s client advice and technical support services.
Risks were greater in the sub-surface area as C100’s generic design intent was completed at RIBA F1, whereas integrated station specific designs were less resolved to RIBA Stage E. Consequently, opportunities arose for challenge, questioning and debate by contractors about compliance with requirements that included a wide range of quality and technical standards. Evidence sourced from the verification programme was valuable in providing a strong evidence base, helping Crossrail to retain control over design quality and outcome certainty.
Lessons learnt – achieving project results through an adaptive strategy
Crossrail CEG understood that late design change would involve considerable time and professional resources. For one project, the risk is onerous enough; with eight stations, cost and time risks rise measurably. When compounded by the absence of contract obligations for contractors to deliver common design, minor change introduced by the IMs and with differing levels of client design information, strategies were needed to mitigate the potential impacts. Without creative and adaptable approaches identified in section 4.3, that helped managed risks identified in 3.1, the author and reviewers understand that both the passenger experience and in use operational value would have been compromised.
Client advice and technical services
Overview
The C100 team consisted of a pool of 35 structural engineers, architects, industrial designers, lighting designers, wayfinding specialists and material experts. The service was led by a RIBA accredited client adviser in the framework lead role for the C100’s scope. Good communications were facilitated through co-location in CEG offices. C100 had an in-depth understanding of both the Crossrail project, and projects of a similar type and complexity across the world. The main benefits of the C100 service are:
- Guidance where interpretation of requirements differed between stations
- Objective advice where contractors were planning suppliers
- Support for CEG in liaising with IMs about contractor design proposals
- Strong incentive to see the original design intent completed well
- Working across all stations:
- Sharing knowledge, expertise and best practice
- Guiding best-in-class design solutions
- Care holders of core project design values.
Service detail
The C100 team comprised four working groups:
- Core architectural common components
- Core structural components
- Specialist call in group
- Safety advisers for CDM and CSM.
Day-to-day, the architectural common components group worked directly with Crossrail’s head of architecture. The structures group worked with central London stations programme directorate and Crossrail site teams. The two core groups supported 12 CEG site architects based across the eight stations. For both, task prioritisation came on demand from CEG site architects or site engineering managers.
The specialist call in group for material expertise and technical specialisms along with the safety advisers were involved when needed for defined tasks. They were directed by the C100 framework lead. All four groups reported to the framework lead, whose appointment with RIBA accreditation as an independent client adviser gave an additional level of expertise to the team, helping CEG architecture to rationalise and clarify design and outcome related requirements. It is a role that has origins in public sector good practice guidance for the delivery of design quality in the built environment through the ‘intelligent client.’ For example, published guidance from Office for Government Commerce[14] (OGC), HM Parliament[15] (HMP), Royal Institute of Chartered Surveyors[16] (RICS) and Royal Institute of British Architects[17] (RIBA).
C100 provided the following detailed set of tasks in the form of responses to 1,500 contractor and IM queries, review of 69 contractor prototypes, inspection of 225 site benchmarks, manufacturer visits and technical papers:
- Guidance for client prototyping lessons learnt integration
- Strategic guidance and advice on outcome related requirements
- Material and component interface guidance
- Selective drawing and three-dimensional computer model reviews
- Product design guidance
- Technical and material performance reports
- Asset tags and safety label guidance
- Signage and wayfinding schedule and artwork checks
- Site meetings supporting CEG architects and engineering manager
- Factory, workshop, manufacturer and supplier visits
- Sample reviews
- Drawing reviews and commentary
- Visual design guidance
- Equal accessibility advice
- Safety case evaluation of contractor designs
- Liaison with CEG’s fire, acoustic, safety and security experts
- Guidance and comment on operations, maintenance and replacement.
Service examples
Four types of approach are used to illustrate the variety of ways in which CEG, with support from C100, went about helping to deliver a common design for the sub-surface areas. From early 2014 the residual procurement risks identified earlier were, in part, managed by CEG co-ordinating design work in the following areas: platform edge structure; lighting; and signage. For reference, type 1 is the contractor design approach in the completion of tunnel lining cladding. Type 2 is a detailed design for the platform edge structure for localised modification on site. The strategy for lighting and signage are types 3 and 4. Types 2, 3 and 4 illustrate how a client-led approach, using the most appropriate specialist, can add value in the form of supply chain efficiency, design quality and programme certainty.
Station tunnel lining, public area cladding
Type 1 – Design and build reference approach
The total area of public area tunnel linings made from moulded glass fibre reinforced cement (GFRC) is 50,000m2; equivalent to 10 football pitches. Between 2014 and 2016, C100 facilitated geometries, details and interfaces for individually removable panels that could be safety handled in a consistent way for access, maintenance and replacement. Panels also looked alike and functioned consistently for the lighting, security and acoustic performance (Figure 5).
Figure 5. Site installation of lower concourse GFRC tunnel lining
Differences in approach by the contractor designers and supply chain manufacturers, modelling scenarios and testing outputs between each station could have resulted in significant variances in handling and visual characteristics. In final versions, there were three arrangements completed, each with minor variances but consistent functional performance. The benefit from C100 services was in design co-operation across stations and cross fertilisation about best, suitable designs and working methods in fabrication and manufacture.
Platform edge structure
Type 2 – Design of a highly resolved engineering system for site modification
C100 designed a highly engineered modular structural frame to each of two platforms edges at the five mined sub-surface stations. The frame co-ordinates four critical elements forming the ‘platform technology’ wall; platform screen doors, platform lighting, emergency smoke extract and passenger communications. Each station contained up to 0.5 km of framing involving complex integration and materials performance (Figure 6).
Figure 6. Site installation of platform edge structure frame
After the design was complete and instructed to the contractors for minor adaptation, a full-scale client prototype was utilised to test human factors and cleaning. Meanwhile, Imperial College, London tested components for cyclic durability and electrical safety performance. The overall approach enabled a timely commencement of site installation and effective engagement with station contractors over a two-year period. The use of shared information about limited options for design resolution of the complex components enabled a focus on building the structure to the programme’s critical deadline set by train operations in the tunnels. Unlike the GFRC tunnel linings, the structural frame is functionally identical in nature between stations.
Public area lighting
Type 3 – Instruction to one main contractor for bespoke design development; completed design purchased by the other contractors
The sheer time and cost inefficiencies resulting from having eight separate station contracts, each developing 10 lights, required a more efficient approach. Some lighting design remained in the design and build scope, leaving CEG to lead product development for those lights where a common approach was of most value. An example is the platform linear lightbox (Figure 7). It was undertaken by instructing one contractor to develop the light to meet requirements and then instructed its use at other stations.
Figure 7. Site benchmark of platform linear lightbox
This approach proved to be highly effective at providing a line-wide design. It worked well because the contractor could use the highly resolved design from C100’s intent, information gained from the verification programme, a detailed performance specification, and expertise from C100 and CEG lighting specialists. As a result, design iterations were minimal and the product was completed well within the critical path.
Signage and wayfinding
Type 4 – Limited supplier framework with pre-approved designs developed by Crossrail
Crossrail procurement team, working with CEG architects and supported by C100, set up a signage framework comprising three manufacturers for detailed development and signage buying solution. Each of 31 non-regulation signs, including structural totems types were prototyped and iterated to provide fit-for-purpose products. Many signs didn’t need rigorous design development as they were modified prototypes from the verification stage that provided a proof of concept level of design resolution. Twelve required further detailed design, mock-up, prototyping and testing to fit-for-purpose stage (Figure 8). Station contractors were instructed by Crossrail to buy bespoke signs and totems from the framework, saving considerable time and money when compared to each station undertaking the work.
Figure 8. Technical prototype by framework manufacturer.
Lessons learnt – client advice and technical services for value in use
The lesson learnt is that client advice in the form identified by the OGC, HMP, RICS and RIBA, carried out in parallel with expert technical support, is of value with intensely used or long life, new and novel projects. Services can be undertaken on the client side at any project stage. In acting on behalf of, with, or with evidence gained from the end user, the architecturally trained client adviser and technical service expert has a vital lead role to perform in assuring project outcomes are realised from the first day that the project opens.
Conclusion
Major projects typically have a ‘knowledge gap’ in the time between design intent completion and when the contractor’s work is completed on site. The gap varies from project to project. The gap can be widened by the use of performance specifications that ensure technical design and regulatory performance risks lie with the contractor. However, they can introduce a host of complex trade off decisions from the ambiguities, low level of granularity about operational level requirements, and resulting design options that emerge late in the design process.
The gap is not generally about meeting regulatory or technical performance; these are usually tested during construction stage. The gap is about value in use. Closing the gap relies on a client lead approach involving detailed work and sound evidence in trade off decisions about the right long term design choices. For example, human scale and perception, productivity and performance, or where significant human or environmental harm is possible. For Crossrail sub-surface stations, value in use was determined at the early design stage, evidenced by strategies C100 embedded into their design, but also by the wide scope of client support services undertaken separately during the design and build stage.
More certain client side information, earlier, about how outcomes in use can be achieved are the core benefit of mock ups, prototyping and testing. Examples of valued outcomes on Crossrail include: measurable time and cost to maintain services, products and components; maintainer safety; depreciation mitigation; product replacement; passenger communications and time efficient use; user welfare; and long-term performance confidence.
With the evidence of hindsight, it can be confidently said that capital value was added in the C100 client design intent stage though standardisation and harmonising access and maintenance across all stations. The author asks the reader to consider that most in use value was added though CEG’s verification programme and client side services. But also to consider that the two approaches also helped to mitigate cost and programme risk resulting from the change in the fit out procurement strategy.
Acknowledgements
The author would like to acknowledge and record the following for their contributions to the paper; Euan Russell, Jorrin ten Have, Lindsay Farmer and Julian Robinson. A particular thanks is given to Rosemary Smiley, Julian Birbeck and Jean-Marc Barsam who acted as joint technical reviewers.
References
- Black, M. Dodge, C and Lawrence, U (editors) (2014). The Value of Common Design – C100 Crossrail Architectural Components. Crossrail Project: Infrastructure Design and Construction – Volume 1. ICE Publishing
- ibid.
- ibid. The Importance of Construction Mock-ups and Trials
- Barsam, JM. Harris, D and Hooper, A. (2017). Crossrail Project: engineering design management on the Elizabeth line, London. ICE Proceedings, Vol 170 Issue C5
- Crossrail (2009). Architecture Design Guidelines, Vision for the System – Unpublished
- C530 Woolwich; C239 Canary Wharf; C512 Whitechapel; C502 Liverpool Street; C435 Farringdon, C422 Tottenham Court Road, C412 Bond Street, C405 Paddington
- ibid. Black, M. Dodge, C and Lawrence, U (editors) (2014). McClements, p.45
- ibid. RIBA Plan of Work 2007.
- ibid. Black, M. Dodge, C and Lawrence, U (editors) (2014). McClements, p.46
- Allen, S (editor) (2016). Pearman, H. Platform for Design – A Well Tempered Environment. Crossrail Ltd
- Tucker, W (2017). Crossrail Project: engineering design management on the Elizabeth line, London. ICE Proceedings, Vol 170 Issue C5
- ibid. Moxon, S and Atherton, S. The Importance of Construction Mock-ups and Trials
- ibid. Tucker, W Crossrail Project: engineering design management on the Elizabeth line, London
- OGC (2004). Procurement Guide, Achieving Excellence in Construction, Office of Government Commerce, 2004 Guide 09. p05
- HM Parliament (2012). A Better Deal for Public Building.
- RICS (2011). RICS Public Sector Property Asset Management Guidelines, 2ND Edition, p58.
- RIBA (2013). Client Conversations, Insights into successful project outcomes, 8.
-
Authors
George Stowell BA(Hons) Dipl Arch MA(Dist) MRIAI RIBA - Atkins
For the Crossrail project, George was technical lead for the Canary Wharf Crossrail station over site development during 2012. Between 2013 and 2018, he was contract manager and client adviser for the line wide design team, comprising Atkins, Grimshaw, Maynard and GIA Equation. In the latter role for Crossrail Chief Engineer’s Group (CEG), Head of Architecture, the team undertook the following:
- Developed user and maintainer performance requirements through prototyping and testing.
- Assured the central London sub-surface station designs and line wide architectural components.
- Used assurance evidence to advise CEG on acceptance of designs provided by their station contractors.
George is an award winning Chartered Architect and RIBA accredited Client Adviser with over 26 years professional experience on the planning, design and delivery of high quality major public projects.