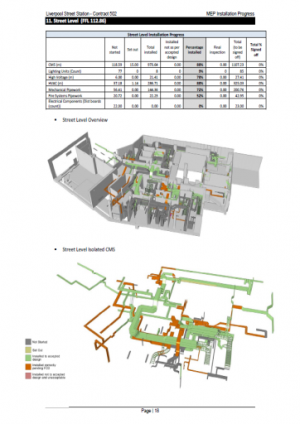
Crossrail Project: Application of BIM (Building Information Modelling) and Lessons Learned
Document
type: Technical Paper
Author:
Malcolm Taylor
Publication
Date: 09/07/2018
-
Abstract
Between 2008-12, Crossrail Limited (CRL) established the main elements of the programme information environment, part of which is now known as Building Information Modelling (BIM). This paper describes a number of the initiatives used to exploit the opportunities BIM technology can bring to design and construction. The paper illustrates specific tactical initiatives to exploit technology advances such as the use of 3D models into 4D and 5D as a tool to manage construction fit-out, as well as being linked to asset data through a geographical information system (GIS). The process of handover into operations and maintenance is also described. The paper also summarises the benefits and lessons learnt in creating and using BIM processes and technologies.
-
Read the full document
1 Introduction
Just as bar coding revolutionised the retail sector in the 1970s, the construction industry has an opportunity to use digital technology and processes to become more effective and efficient.
In 2011, the Government announced that all publicly funded projects must reach BIM (Building Information Modelling) Level 2 by 2016. The construction industry’s capability for visualisations and data management flourished, and BIM technologies were adopted by many architects, designers and some contractors – but not that many clients.
In the 10 years since Crossrail’s Parliamentary phase concluded in 2008 technology has advanced unrecognisably. Mobile devices and apps are now in everyday use; the cost of processing power has decreased by a factor of fifty and data storage costs are fifteen times lower. The price of sensors has halved, whilst bandwidth is forty times greater.
This has had a profound effect on how major projects like Crossrail can manage and leverage data, not only when building infrastructure but also understanding how it behaves when in use. Crossrail had always intended to build two railways: one virtual, to facilitate design and construction and then the subsequent management of the physical. For Crossrail to successfully transition into the Elizabeth line as an operational railway, both must be achieved and the advances in technology need to be exploited in both construction and operation.
Between 2008-12, CRL established the main elements of the programme information environment, part of which is now known as Building Information Modelling (BIM). A previous paper (Crossrail project: building a virtual version of London’s Elizabeth line) described the development of the Common Data Environment (CDE) and the information landscape. That paper also illustrated that the Crossrail BIM environment and many related processes were established prior to the 2012 UK Government mandate on BIM.
This paper now describes the application of BIM with examples of a few of the tactical initiatives used to exploit the technologies available. This paper also summarises the benefits and lessons learnt in creating and using BIM processes and technologies.
2 Overview of BIM
Crossrail defines BIM as the process of generating and managing information throughout the whole life of the asset lifecycle by using model-based technologies linked to databases of reliable information. The CRL BIM objective has been stated as:
To set a world-class standard in creating and managing data for constructing, operating and maintaining railways by:
- Exploiting the use of BIM by Crossrail, contractors and suppliers
- Adoption of Crossrail information into future infrastructure management (IM) and operator systems
The BIM strategy seeks to take advantage of new available technologies to link databases of information, together with Master Data Management (a BIM Level 3 concept), all of which give leverage to the value and potential of information in design, construction and project management decision-making. Further details of the approach taken by Crossrail can be found in the learning legacy document on BIM principles.
The CRL BIM environment at its basic level comprises a set of several linked databases which use workflows to carry out business activities, rather than a set of separate specific software applications. Following the trend in the BIM world, the federated 3D parametric CAD models on Crossrail were kept as light and as unintelligent as possible, with all the asset details being contained in separate linked databases – this allows the asset data to be structured in a much more user-friendly and efficient way. The 3D models are also easier to manipulate, for example linked to scheduling packages to create construction sequences. So the initial core service of the Project Information team on the Crossrail programme in a BIM context was to create a Common Data Environment providing a ‘Single Source of Truth’ for all information enabling the future operators and maintainers to manage their assets.
The duration of the Crossrail programme, which has taken over 10 years between Parliamentary Approval and opening of the railway, has profound implications in terms of technology development and expectation. Long construction contract schedules can make it difficult for both clients and contractors to take advantage of new technologies. For example, Wi-Fi on trains and in stations is expected as normal in 2018, but was never an original functional requirement for the railway in 2008. Fortunately, the NEC Target Cost nature of most contracts meant that new ideas and innovations could be adopted and brought into use by agreement.
3 Technology Initiatives
3.1 Use of 3D & 4D Modelling to manage Construction Fit-out of MEP&A
Project planning and control during construction can be achieved using a variety of different methods. Traditionally this involves utilising the 2D design drawings and using planners experience and known production rates to calculate task durations. Progress is then tracked through a combination of marked up 2D drawings, Excel spreadsheets and word of mouth. Crossrail has its construction contract deliverables based upon the traditional way of planning, but wanted to take advantage of how 3D modelling technologies could help improve understanding of progress and enable more informed decision making. The commitment to working in 3D is critical, much more than simply the creation of visually correct objects. In a BIM context, CAD is about space management and interface configuration, allowing designers of many different disciplines to use technology for smart clash detection and control of interfaces.
Using various software (e.g. Primavera, ProjectWise, Bentley Building Suite, Synchro Pro Navisworks, and Solibri), for specific elements and MEP disciplines the project schedule was linked to the 3D information to produce the 4D model. The information could exist in a number of different formats and particular care had be taken to ensure the most relevant formats were chosen. Viewpoints could then be created within the 4D model and appearance profiles set up to create visualisations that could show the progress of design and installation at any particular point in time, and also includes quantities to create a 5D aspect.
Using 4D models to plan helps speed up understanding of progress within the project team considerably, also as it is quicker and simpler to understand it means that greater levels of detail can be visualised. The 4D models help analyse the schedule and visualise conflicts that are not apparent in the normal Primavera-type Gantt charts and diagrams. This enabled the project team to easily visualize time constraints and opportunities for improvement in the project schedule. The 4D model can also be used to manage expectations for payment as it allows all teams to understand progression better. It supports the planning team and financial team to have the same understanding so no work is paid for until it is agreed that the task is complete. An example of a typical report output is shown in Figure 1.
Figure 1 – 4D model output in a typical report
Although 4D was never specified contractually in the Works Information, there are many other examples of its use, such as:
- Demonstrating the propping sequence removal within confined shafts and tunnels at Liverpool Street Station
- A time line model of the complex benching sequence for Sprayed Concrete Lining (SCL) to create the cavern at Stepney Green
- Providing visual clarity and understanding of the scope of work to be tendered at Westbourne Park and Paddington New Yard
3.2 Linking Asset Data through a Geographical Information System (GIS)
Tracking the location of assets is an essential asset management function. We have sought to use the potential of the geometric and feature information from 3D models by translating this information into our GIS. This allows designers and assurance staff to be much more efficient in understanding what assets are in particular spaces or rooms. Part of the asset inventory metadata within the information database eB includes the named space in which the asset can be found. Historically across the industry, the ability to share information between CAD and GIS has been laden with difficulties, both in terms of the way in which information is stored, and the taxonomical classification of that information. Nevertheless it was required that data be shared between these systems as seamlessly as possible.
In order for geospatial information to be able to be interoperable between different systems within Crossrail, adherence to a common data architecture was required. As the Open Geospatial Consortium (OGC) had already built common geographic information architecture in the form of the Simple Feature Access Standard, this was adopted by Crossrail.
A workflow within ESRI extracts and transforms a space from the 3D CAD model. The use of an extruded 2D floor plan then enables the user to make a spatial query and identify which assets are within that space. For example, the user could go into the GIS, call up a station model in the 3D GIS, look at a floor plan and click on a specific room. They could then call up all assets within AssetWise that are located in that room. This enables the user to ensure that what is in there is correct, understand if anything is missing or continue with further queries within AssetWise about the assets. This use of a GIS can drastically reduce the time taken (reported anecdotally as by at least 75%) to understand what data is where.
Figure 2 – GIS
This type of functionality has now been developed to allow this form of interrogation to be done by streaming over the internet, thereby giving considerable opportunity and access to this type of data.
3.3 Augmented Reality
In 2014 a mobile phone/tablet application was begun on the Custom House station project. The trial implemented a Bechtel-developed AR mobile (iPad) application to validate whether it brought process and quality efficiencies to existing site activities. The main metrics focused on process cycle times and information quality which it was assumed should lead to better decision making.
We believed that AR had the potential to benefit construction in a number of areas (or “use cases”). The specific use case tested in this pilot focused on how construction progress information can be captured against an AR 3D model in the field and automatically pushed back into the 4D model environment to assist with project planning activities.
Figure 3- AR Pilot
The pilot successfully demonstrated a significant process cycle time improvement from 96 work-hours per month to 26 work-hours per month. This was realised because the construction progress updates were being entered directly into the 3D model (via the AR viewer) and then automatically pushed back to the 4D model being used by the planner. This removed a number of non-value-add manual steps from the traditional process.
This trial demonstrated the potential value of AR to construction but also highlighted that there are numerous factors and considerations that currently limit its suitability for large scale deployment. The trial is detailed in the Learning Legacy Augmented Reality Trials on Crossrail
3.4 Handover of Information into Maintenance & Operation
Crossrail Ltd. is only accountable for the early stages of the infrastructure life cycle – the design, construction and commissioning phases of the railway, not the operation or maintenance. Along with handing over the physical railway to the operators and maintainer, Crossrail must hand over all the associated information and data required for these activities, as well as all relevant records.
Handover of information and data from the capex environment to the operation phase has always been a difficult and often fraught stage for infrastructure projects of any scale. For Crossrail, our Central Section had nine major stations each being delivered by different teams. Each station itself was made up of multiple contracts (advanced works; design; construction; etc.) by multiple parties that could produce information in a multiple number of ways. Each station comprises of typically 15,000-25,000 individual assets, each of which require documentation and supporting data that needs to be consistent across the Crossrail programme.
So the approach taken was for each individual contract within a station / facility or along the route to have a standard template for its deliverables. This template was created within our Information Database (AssetWise, formally known as eB). This would enable the data to be collected and managed in our CDE appropriately as the single source of truth. In a BIM context, it was originally conceived that the future operator and main maintainer would also use the CDE (in line with PAS1192 Part 3) for operation and maintenance, so that the future Elizabeth Line could continue work within a BIM Level 2 type environment. The concept was for the CDE to act as the master data source and from which playlists of information could be created as shown in Figure 4.
Figure 4 – Information Playlists
During 2018-19, Crossrail will now be handing over information directly to a variety of organisations: Transport for London, Rail for London and London Underground, as well as a number of other potential interested stakeholders such as Network Rail and local London Boroughs.
The greatest disappointment from a BIM perspective is that RfL decided to stay with the more traditional approach to their asset information management. They and London Underground Ltd simply require Crossrail to provide them with copies of information to be placed into their own separate RfL and LUL information systems for document control, asset management etc. The data and information packages are based on the LUL Mandatory Asset Information Deliverables (MAID) listing of documentation. RfL did initially set out with an aspiration of being at least BIM Level 2 but this has not materialised. For maintenance and operations, TfL do not yet have a unified approach across their business where currently it is perceived there is an emphasis on bringing technology into use rather than improving operational processes with smarter information management. Sadly, most of the relational links created between different types of data – useful during the delivery of the programme – will be lost. Although at BIM Level 2 during design and construction, at an operational level RfL and LUL will be working at a BIM Level 0 or 1 when the Elizabeth Line is opened.
TfL will corporately receive a complete archive of the CDE including all key information produced throughout the design and commissioning of the railway, including all relevant corporate data, but this will not be a day-to-day working environment as envisaged within the original BIM concept.
4 Benefits of BIM
Bearing in mind the broad objectives of BIM look to improve processes and activities across the full asset lifecycle, the range of benefits can be wide. The benefits achieved from BIM can be broken down into three main categories: direct, indirect and cost / time benefits. Each of these are outlined below.
4.1 Direct Benefits
The key benefits from working in a BIM environment in design and construction are improvements in efficiency (time saved etc.) and effectiveness (quality, compliance, etc.). They include:
- Reduced wastage (fast spatial interface coordination, minimising clashes)
- Improved efficiencies (faster collaborative approvals)
- Reduced information loss (using only the most recent document/drawings)
- Reduced programme risk (through 4D analysis)
- Improved performance (linking documentation and 3D models etc. into GIS mapping)
- Collaborative model transfer from designer to contractor
- Smart asset management by linking data 3D models directly to an asset inventory database (not fully achieved with Crossrail)
4.2 Indirect Benefits
There are a number of indirect benefits and these include:
- Safety – a better understanding of construction through visualisations, by combining 2D and 3D
- Environmental – a reduction in waste through model clash detection and improved carbon efficiency
- Reliability – always the most up-to-date information from an integrated single source of truth
4.3 Cost & Time Benefits
For people unfamiliar with the breadth of BIM technologies available, there is occasionally a belief that working in a BIM environment can be expensive and not give a viable return on investment. Evidence based, this is not the case for most multiple contract construction programmes.
In Crossrail the creation of a BIM environment with the use of a CDE by all parties in design and construction to deliver a working railway has been a significant success, both in terms of cost efficiency and management of the programme of over 100 main separate contracts. Defining most of the information requirements and types early on meant there was never any doubt as to what was wanted. The use of workflows within linked databases for processes and activities meant that different types of data and information could be collected and related in a ‘single source of truth’. Had Crossrail retained different software packages for each of the specialist activities needed in design and construction, rather than using workflows, this would have indicatively cost over £10 million per annum for 7 years in additional software and support staff costs.
Use of visualisations such as the 3D model through design and then into 4D and 5D for progress reporting, are now commonplace BIM applications. The 5D approach as outlined in Section 3.1 above was brought into use on a number of sites and typically saved £1.2 million at each contract through the reduction of two full time equivalent staff needed to process and agree progress.
The analysis and interrogation construction scenarios using a 3D model with different planning schedules at Farringdon Station cost some £120k but enabled £8 million to be saved from risk contingency.
5 Lessons Learned & Recommendations for Future Projects
Over the design and construction phases, a reflection back on what was done – particularly in difficult or uncertain areas – may help others not to make the same mistakes, or help build upon any areas of success. Utilising BIM on the Crossrail project a number of lessons were identified.
5.1 The Common Data Environment
- The CDE needs to be structured with the end in mind and at the pre-feasibility or conceptual stage of the project.
- Use an object-orientated relational database(s) with workflow capability as the main information management and repository. This will enable direct links between project functional requirements and systems, assets, documentation etc. as well as allowing business processes to be brought into place with minimum ease or IT integration. The database needs to be able to handle ‘objects’ (within which any form of data may reside), as well as ‘event objects’ which are a powerful way of managing transactional workflow activities.
- Determine what types of information will be required when, and identify an asset breakdown structure (ABS) to system level for most facility types. From the ABS a Work Breakdown Structure (WBS) together with a supporting Cost Breakdown Structure (CBS) can evolve. And finally an Organisational Breakdown Structure can then be developed to deliver the intended works. These data structures form a key backbone of the technical and programme control activities in the delivery and future maintenance of the infrastructure
- The level of detail collected only needs to be commensurate with the scale and lifecycle of the project at that time. There is now good guidance on levels of detail (graphical, non-graphical and documentation) on Government and BIM Task Group web sites.
- Revision controls, which display the current data in a manner that makes it easy to access and view the history of earlier revisions, provide great assurance to the authenticity of information.
- Big projects with a large supply chain need greater prescriptiveness in terms of detailed information requirements to ensure consistency, which will in turn yield more predictable results.
- Standardised templates for deliverables should be used for all contracts to enable the integration of deliverables and their assurance prior to handover into operations and maintenance.
- Document and data approvals management enables tracking progress of approval. Process and workflow functions including tasks, RFI’s, Contract correspondence and change control, actions and tracking progress against those actions.
- Keep the 3D models as light as reasonably practicable but retaining their object orientation and directly linkage to a well-structured data repository where you can sift, sort and form all sorts of useful relationships for maintenance and operations.
5.2 Asset classification and definition
Details of Crossrail’s approach to asset classification can be found in the learning legacy document on asset information management which sets out the CRL approach to Asset Information Management and gives a number of lessons learned including:
- The importance of having an aligned Organisation and Asset Management Strategy. As noted with the CDE, the project needs to start with an Asset Breakdown Structure and then develop and relate to the other forms of breakdown structure (work; cost; and organisation).
- Clear requirements, which include: classification, coding and dictionaries which are an important part of linking data sets together. The classification and coding are the lifeblood of the future maintenance system.
- Utilise Asset Dictionary Data Definition Documents to set out exactly what is required for each maintainable asset element. The data required for each asset needs to be collected during construction was and then stored in a records database, which can be linked to all the relevant associated Operation and Maintenance documentation, as well as the 3D models.
- The need for Asset Tag IDs throughout designs (including 3D Models / Drawing / Schematics).
- Operation and Maintenance Manuals should be started in the design stage and handed over to the main contractors for completion. This enables their early visibility and will ensure consistency of use.
5.3 Process
- The cultural barriers to implementing BIM should not be underestimated, as there is a requirement to make significant changes to well embedded work processes. This starts in procurement to set the right collaborative approach
- As a client, be very mindful of suppliers who say their software is fully interoperable as you may pick up the risk of data incompatibility. Working to BIM Level 2, any federated model exists as a completely distinct and separate entity. Individual models do not interact; they only supply the data that is used to create the overall model. This means the liabilities of those who supplied the models is clearly unchanged and with the creators. The client (or steward) of the combined model has to make sure they all fit together. So it is important for the client to be prescriptive about model formats etc. together with good CAD standards so they do not carry the risk of things not fitting.
- Clear requirements, levels of detail and instructions are essential to ensure that the project requirements are understood. For example, what level of detail from fabrication is required to be added to design drawings to complete them as As-built.
- All projects using CAD should specifically require the 3D model(s) as a primary deliverable and to be kept up to date as the project progresses. This is the most effective way of managing the spatial coordination of different disciplines and avoid unnecessary waste through clash detection.
- Design change should be managed within the CDE and not as an external additional process
- Clearer more prescriptive guidelines are required for the coordination of redlining, As-built and schedule integrated modelling, particularly where this work is carried out by multiple designers and contractors
- Understanding the Infrastructure Maintainers information requirements and involving them early in the project is critical
- Details of the Crossrail core set of processes within a single workflow based Information Management System (IMS) are given in the learning legacy document on the information system. This paper also gives a set of useful specific lessons learned in implementation of the system.
- Crossrail’s method of processing contractual CAD drawing deliverables received from the supply chainis explained in a learning legacy document on management and client assurance of contractual drawing deliverables.
- Use of metrics for assessing the quality of information deliverables of all types is essential. Key performance indicators and measures of quality should be established at the start of any project and compliance embedded into contract terms.
5.5 Construction Progress Reporting in 4D and 5D
- Progress scheduling should be set up to combine the 3D model with schedule as early as practicable. Once the schedule exists in one form or another the 4D model can help to visualise constraints and provide opportunities for schedule improvements through the re-sequencing of activities, the redesign of building components and/or the reallocation of work areas in advance of site presence.
5.6 People
- Adoption of BIM requires strong leadership with a clear understanding of the ultimate deliverable or ‘vision of the end’. Crossrail were fortunate to have a Chief Executive (Andrew Wolstenholme) from 2011-2018 who was a supporter and champion of BIM.
- Collaborative working is essential to ensure all parties (client, designers, contractors, third parties) and departments (technical, commercial, engineering, procurement and construction) are pushing in the same direction for BIM adoption across the project lifecycle
- BIM implementation will only be as strong as the weakest link in the supply chain. Training through the whole supply chain is critical particularly in the current environment where BIM competencies are still growing. Crossrail and Bentley Systems created an Information Academy to encourage the delivery of best practice throughout the project supply chain.
- The whole project team needs to understand their role in BIM as it affects all phases of the project lifecycle. This needs to be supported by specialist central staff, such as the Project Information Management Team and scheduling specialists who act as the glue to bind the teams together
- Newsletters, Lunch-&-Learn talks, poster campaigns etc. were just some of the many tools used to help communicate the BIM and information management messages
5.7 Technology
- Clients need to push for open standards and a move from using proprietary formats that restrict the supply chain and stifle innovation. However, as a Client, if there is a chance that you will be left to deal with poor data interoperability, this should be avoided by being prescriptive on, for example, file formats. Be very wary about software vendors promising their systems are compatible with everyone else’s system – reliance on this can be fraught with risk.
- Consistent application of standards is fundamental to the success of BIM. This includes modelling standards but also standards that relate to data that links to the model, for example schedule Work Breakdown Structure (WBS) needed for successful timeline modelling
- Parametric 3D models are an essential foundation for leveraging time, cost, and design analysis. Use of 3D modelling should always be prescribed, to leverage and improve space management and coordination of different engineering disciplines
- As the importance of the 3D model increases so does the importance of model data security. Data model security within the CDE needs to be well structured, flexible and scalable. Areas of higher security, such as station access protection measures or sensitive control systems may need to have higher levels of security and limited access.
5.8 IT
- Ensure that the technology infrastructure (networks, broadband etc.) are well established for site / satellite offices so that they become effective and not disengaged remote hubs
- Buy in software, do not try to create or adapt applications unless there are specific project benefits
- If specific bespoke software is required, use best-of-breed off-the-shelf, even if is not exactly right. Certainty and reliability are required, and in many cases it could be better to adapt processes to suit. However tempting, do not customise software systems except as a last resort. This requires additional support with ongoing project costs as software gets upgraded and the customisation needs to be reviewed for compatibility.
- Through the course of the Crossrail project numerous IT systems were used to support and deliver different aspects of the project. Once the Elizabeth line is handed over to Rail for London (RfL) to operate and all the Crossrail contracts have been closed, none of these IT systems will be needed for the ongoing operation of the Elizabeth line. Archiving these systems is a challenging task, and details of the approach taken, together with the lessons learned, can be found in the learning legacy document about archiving Crossrail data
Acknowledgements
The author would like to thank and acknowledge the important role played by past and present members of the Crossrail Technical Information Department and IT Directorate, whose hard work, skills and commitment ensured the information (BIM) strategy was successfully delivered.
-
Authors
Malcolm Taylor - Crossrail Ltd
Head of Technical Information