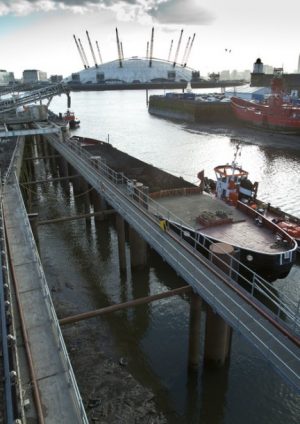
Excavated Materials Story
Document
type: Micro-report
Author:
Lorna Mellings BSc MSc CEnv MIEMA, Greg Limna BEng(Hons) CEng MICE
Publication
Date: 31/03/2017
-
Abstract
The construction of the Crossrail project resulted in the generation of over 7 million tonnes of excavated material, of which over 98% was beneficially reused. Crossrail adopted a client-led approach to the reuse of the material (whereby some of the destination sites and means of transportation were specified to contractors by Crossrail) together with flexibility to allow some of the individual contracts to make their own arrangements for beneficial reuse as appropriate. The benefits of adopting a client-led approach were that it allowed a significant proportion of the material to be used to create a landmark new nature conservation project at Wallasea Island, whilst the early definition of a solution reduced the programme risk associated with a potential lack of suitable disposal sites during the main tunnelling and excavation works and it also allowed the development of infrastructure to allow transportation by water and the early allocation of rail paths which together contributed to 80% (per tonne km) of the excavated material being transported by rail or water.
This paper describes the approach followed by Crossrail to reuse the excavated material from the project, identifying the main stages of the process, the key activities undertaken by both the client and contractor and the lessons learned from implementation. It will be of use to clients of major infrastructure projects who are looking to adopt a similar approach to the reuse of excavated material. The lessons learned at construction sites that were implementing the Crossrail requirements will also be of use to any project or contractor who is disposing of excavated material.
-
Read the full document
Introduction
The construction of the central section of the Crossrail project comprised 42 km of tunnels running from Royal Oak Portal in the west of London, to Pudding Mill Lane portal on the north-east spur and Plumstead portal on the south-east spur and the excavation of boxes, shafts and caverns for associated portals, stations and shafts generating over 7 million tonnes of excavated material.
Figure 1 – Crossrail project central route section
By the time all the tunnelling, stations and shafts excavation was complete over 98% of the excavated material had been placed at sites for beneficial reuse and a large proportion of that had been used to create a significant part of one of the largest wildlife habitats in Western Europe In achieving this 80% on a tonne per km basis was transported by water or rail without compromising the either the tunnelling or any other elements of the construction programme.
This paper sets out how Crossrail Limited (CRL) achieved this exceptional outcome and in so doing provides some of the lessons learned along the way and recommendations for future projects faced with similar challenges.
The Authorisation of Crossrail
The powers and deemed planning permission for the Crossrail project are conferred on the organisation charged with delivering the railway (the ‘nominated undertaker’) by the Crossrail Act 2008 . It was during the authorisation and planning phase to obtain the Act that the first potential solution for suitably disposing of the excavated material generated by the project was identified and set out in the Crossrail Environmental Statement. That solution involved disposal at ten UK landfill sites and included where necessary the construction of new temporary wharf and rail facilities, where it would be used for engineering purposes principally cell construction and capping. The ten sites were Pitsea (Essex), Rainham (Havering), Calvert (Buckinghamshire), Stewartby (Bedfordshire), Colnbrook (Slough), Shakespeare Farm (Kent), Patteson Court, Redhill (Surrey), Springfield Farm (Buckinghamshire), Wapseys Wood (Buckinghamshire) and Westmill (Hertfordshire). These sites were identified against a construction strategy that included the aim to remove, where reasonably practicable, excavated material by rail and water transport and it was estimated then that approximately 30% of surplus material would be transported by rail, 15% by water and the remaining 55% by road.
At that time it was acknowledged that while this solution had been shown to be feasible, the future organisation responsible for delivering the Crossrail project would nevertheless be required to use the waste hierarchy to identify the most appropriate destination for excavated materials, seek to provide excavated materials for re-use on development projects being constructed at the same time, carry out a review of appropriate development projects prior to Crossrail project construction and develop a framework for the re-use of the excavated material on those developments.
Figure 2 – Crossrail Environmental Minimum Requirements Waste Hierarchy
From Authorisation to Delivery
CRL was named as the nominated undertaker for the Crossrail project by the Secretary of State in 2008, inheriting amongst other things responsibility for finding a final disposal solution for the excavated material.
With the funding framework established in October 2007 and the Crossrail Act receiving Royal Assent in July 2008 CRL began the further development of the design and to search for suitable disposal sites for the excavated material. The identification of suitable sites would help to de-risk the project by bringing programme and cost certainty to the tunnelling works which were scheduled to start in 2012. Twenty disposal sites and fourteen transhipment sites were considered against the following objectives:
- Beneficial reuse the material.
- Journey to disposal site to maximise water and rail transport where reasonably practicable.
- Ability to receive material in 4 years time (from 2012).
- Had planning permission or was in the process of obtaining permission.
- Flexibility to meet variations in the complex construction programme.
During this time CRL became aware that the RSPB was developing a nature conversation project at Wallasea Island located eight miles north of Southend-on-Sea, Essex and was looking for partners to supply material to reshape the geography of the island and help them create new habitat.
Figure 3 – Location of Wallasea Island and aerial photo from before work began
- CRL included Wallasea in its review of possible disposal options and found that it offered considerable benefits when considered against the obligations inherited from the authorisation stage:
- It met CRL’s commitment for beneficial reuse.
- As an island it promoted the use of water transport.
- Wallasea could take over 4 million tonnes of excavated material.
- It had started the planning process (application for planning permission was made by the RSPB in November 2008 and permission granted in July 2009).
- It allowed a detailed cost estimate and programme to be produced bringing certainty to this part of the Crossrail project.
CRL entered into an agreement with the RSPB in 2008 to construct a cell (cell 1, later named ‘Jubilee Marsh’) at Wallasea using suitable material excavated by the project and by September 2009 CRL had entered into a memorandum of understanding with the Port of London Authority to confirm its commitment to use barges and ships along the Thames to move its excavated material.
The work to identify suitable disposal sites together with the use of Wallasea included a review of the risks associated with their use and measures to mitigate those risks. The goal was to provide a solution that would support the main construction programme, in particular the tunnelling and provide alternatives should that programme change. The review concluded that if CRL was going to adopt a scheme that incorporated the use of Wallasea it should de-risk the overall disposal solution by:
- Implementing sections of the scheme in advance of main construction so that Wallasea could receive material when tunnelling started.
- Creating stockpile areas at contractual interfaces (transfer sites).
- Designing the Wallasea scheme to be able to deal with varying and maximum excavation rates.
- reviewing contractual interfaces; and
- Identifying alternative beneficial reuse disposal sites and modes of transport should material be unsuitable for, or be unable to be transported to Wallasea.
CRL mandated the use of Wallasea Island for the disposal of excavated material in its main works contracts by making the contractors responsible for transporting suitable excavated material to transfer sites previously established by CRL and unloading at them for onwards transportation to Wallasea for placement by a separate contractor procured specifically for that purpose.
Each main works contractor was given a date by which excavated material could be transported to Wallasea Island and if their works generated excavated material prior to that date then the contractor was made responsible for disposal of that excavated material in line with CRL’s requirements which included the contractor taking on the responsibility for the transportation and/or beneficial re-use of the excavated material.
CRL awarded the contract for the eastern running tunnels to the Dragados S.A. / John Sisk & Son (Holdings) Lt Joint Venture (DSJV) on 23 December 2010; the western running tunnels to the BAM Nuttall Ltd / Ferrovial Agroman (UK) Ltd / Kier Construction Ltd Joint Venture (BKF JV) on 31 January 2011; and the Thames tunnel to the Hochtief / J Murphy & Sons Ltd Joint Venture (HMJV) on 07 April 2011.
Unlike the main western and eastern tunnel drives which passed predominantly through London Clay, the Thames tunnel drive was through chalk. Wallasea could not accept chalk as it was unsuitable for habitat creation and the moisture content of the excavated material which is extracted as a slurry was far too high for it to be shipped in any case. Instead the slurry was processed through a slurry plant established on site to remove the water and the resulting material transported by road to Pitsea where it was used as a capping layer on the landfill site to create rare chalk wildflower meadow habitat.
Implementing the Scheme in Advance of Main Construction
The use of Wallasea Island for the disposal of excavated material required the construction of a new 180m jetty at Wallasea to receive the transport ships and a conveyor to transport the material within the site. The jetty comprised two 800 tonne steel pontoons, each 15m wide and was able to accommodate two 90m, 2,500 tonne ships simultaneously. At peak, two unloading machines per pontoon could service four ships and unload up to 10,000 tonnes of material over a 24 hour period. The conveyor was 800m long and stretched from the jetty to a holding point for the excavated material, from which the material was then distributed around the site by truck. Excavated material was unloaded directly from the ship onto the conveyor system. To accommodate tidal movements of up to 6m the conveyor comprised a flexible section on the pontoon connecting to a fixed shore section.
CRL awarded the jetty and conveyor contract to BAM Nuttall Ltd in January 2011 and the work was completed in August 2012 after which the facilities were handed over for operation and maintenance to a second, separate, Wallasea Island contract for the receipt, handling, shipping and end placement of the excavated material. This second contract was awarded to a joint venture comprising BAM Nuttall Limited / Van Oord UK Ltd in December 2011.
The BAM Van Oord JV was also responsible for operating a waste transfer site located in Barking & Dagenham known on the project as the Docklands Transfer Site, or DTS, providing shipping from DTS to Wallasea and shipping from another transfer site that was operated by the BFK western tunnel drive contract at Northfleet in Kent to Wallasea, unloading the ships at Wallasea and placing the material to create the Jubilee Marsh habitat area.
The Dragados/Sisk JV also established new wharf facilities for the eastern tunnel drive at Instone Wharf on the Limmo Peninsular in east London for the shipment of excavated material by BAM/Van Oord to Wallasea.
An extensive programme of ecological mitigation works had to be carried out before main works could commence within Cell 1 at Wallasea, with a number of management and monitoring plans being developed. Water voles are known to inhabit most of Wallasea Island’s ditches and as the construction programme at the island included extensive reshaping of the existing water course, many of the voles were rehomed. The work was undertaken over a period of 2 years and completed in 2014 with over 150 water voles living in the Cell 1 area being moved to nearby areas. Over 8,200 common lizards and 40 adders were also translocated under licence as part of the works. A number of main and outlier badger setts were located in the cell 1 area so these were closed under licence and an artificial sett created in another suitable location on the island.
All the facilities needed to successfully transport excavated material to Wallasea were completed and ready for use by the time tunnelling began on the western tunnel drive from Old Oak Common in May 2012 and the eastern drives in November of that year.
Establishing New Transfer Sites
Transport of material to Wallasea required the construction of two new transfer stations with wharf facilities: the Docklands Transfer Site (DTS) in Barking and the Northfleet transfer site in Kent. The DTS received material by road from station, shaft and portal excavations whilst the Northfleet site received material by rail from the western tunnelling portal at Royal Oak Portal/Westbourne Park.
When identifying the transfer sites CRL considered, amongst other things, transportation modes into the site (road or rail), tidal restrictions for the wharves, and land available for storage. The land available at each transfer site for storage capacity was based on maximum excavation rates and the operational layout of each site. Areas were needed to allow for the segregation of unsuitable materials, a material testing area, weighbridges and the efficient flow of traffic through the site. CRL also had to ensure that at each transfer site contractual interfaces were clear and each contractor was aware of where their responsibility applied.
CRL obtained the relevant planning permissions and environmental permits to operate these sites in advance so that the works at these sites could be implemented early BAM/Van Oord at DTS works and the western tunnelling contract (BAM/Ferrovial/Kier) at Northfleet. The permits were later transferred to the contractor responsible for operating the site. At both sites material was transported by ship to Wallasea by BAM/Van Oord. By CRL obtaining the environmental permits (and the planning permissions) it meant that the programme was not affected and it was then simple to transfer the permits to the contractors operating the site ensuring the ability to confer responsibility and limiting legal liability when site operation as a transfer site was in place.
The DTS permissions were originally sought for normal hours working i.e. 8am-6pm Monday to Friday and 8-1pm Saturday, but this had to be renegotiated subsequently to allow 24/7 operation because this was needed to support 24/7 working hours on the central section worksites.
Figure 4 – Docklands Transfer Site (DTS)
Figure 5 – Northfleet
As noted earlier the Dragados/Sisk JV also established new wharf facilities for the eastern tunnel drive at Instone Wharf on the Limmo Peninsular in east London for the shipment of excavated material by BAM/Van Oord to Wallasea.
Figure 6 – Instone Wharf
Figure 7 – Limmo & Instone Wharf
Alternative Beneficial Re-use Sites
When it was first developed the excavated material strategy planned for sending 4.6 million tonnes of material to Wallasea and the rest to be taken to other sites. CRL identified two alternative sites to Wallasea (Ingrebourne Valley and Fairlop Quarry) for handling material generated by early contracts before Wallasea was available and to take any material that was not suitable for disposal at Wallasea. At Ingrebourne the material was used to create a new golf complex, Ingrebourne Links, on a site previously used as a municipal landfill in Rainham, Essex. At Fairlop Quarry, another old landfill site, it was used as capping and for engineering to create new agricultural and nature conservation sites. CRL set up the arrangements with Ingrebourne and Fairlop in 2011 and communicated the arrangement to the relevant contractors via a contract instruction. By identifying and making the commercial arrangements with these sites directly CRL had clear visibility of where material was being sent when it could not go to Wallasea and ensured compliance with the ‘beneficial reuse’ requirement as well as creating a commercial advantage due to the volume of material and reducing the interface with Fairlop and Ingrebourne to being with CRL rather than multiple contractors.
HMJV (Hochtief Murphy Joint Venture) were responsible for identifying a beneficial reuse site for chalk tunnelling material arising from their contract. HMJV identified Pitsea in South Essex where the material was used to support restoration of an RSPB nature reserve and Kingsnorth where it was used in land raise to allow for construction of a commercial park. Some of the material from the HMJV portals at North Woolwich and Plumstead was sent to Wallasea as this material was suitable.
Within the Works Information, contractors had the opportunity to submit proposals for reuse, recycling and/or disposal of excavated material and its transportation to CRL for acceptance prior to removing materials from the site; however this mainly applied to sites where the material could not be taken to Wallasea due to not meeting criteria.
Transport & Logistics
A summary schematic illustrating the original plan for how excavated material was to be transported from the central section sites is provided in Figure 6.
Figure 8 – Excavated material transportation planning
Working with the tunnelling contractors, CRL had to obtain tunnelling rate parameters in order to evaluate the flow of excavated material through the logistics system e.g. how much material was required to be loaded or offloaded and how much material the conveyors had to carry (tonnes per minute). The end-to-end system had to be capable of dealing with variations of multiple tunnel boring machine rates, so that the system itself did not become the limiting factor for tunnel boring machine rates. Adequate space on sites was identified to provide stockpile area with capacity for an agreed number of days of production. These areas provided a limited buffer should it not be possible to remove excavated material from a site. Generally each station and tunnelling site had approximately 3 days worth of storage space whilst at DTS and Northfleet there was 2 months and 1 years worth of stockpile storage respectively.
Rail paths between the western tunnel portal at Royal Oak in West London and the transfer station at Northfleet were obtained by CRL in advance of the procurement of the main contracts. Traditionally rail freight companies ‘own’ particular train paths, so contractors would have to use the company that ‘owned’ the required rail paths. However by CRL obtaining their own train paths in advance it meant CRL could freely issue them to the contractor (BFK JV) who could then competitively tender for a rail freight operator, rather than being limited to operators that had the necessary paths. This reduced the risk as it secured a rail route from Royal Oak Portal to Northfleet.
Further rail paths were used by the eastern running tunnels contractor (DSJV) for movement of material from Pudding Mill Lane via Bow Midland Yard to Calvert and these were operated by the freight operator.
CRL carried out contingency planning to consider options should parts of the excavated material strategy underperform or fail. This considered scenarios such as the Thames Barrier being closed, the rail path from Royal Oak Portal to Northfleet being unavailable and stockpiles becoming full. This led the project to reserve disposal space at two sites, Fairlop and Ingrebourne, to which excavated material could be diverted at short notice should the need arise.
Whilst this material would be diverted from Wallasea the fact that this disposal space had been reserved created certainty that it would still be beneficially reused and of the disposal cost. As material could be diverted to these sites at short notice it provided confidence that the excavated material strategy would not impact on construction rates.
Issues Encountered
Operating Transfer Sites- Cross-contamination
For the majority of construction sites, especially the station and shaft sites in the central section, excavated material had to be initially taken out by road. This was because the location of the sites in central London just did not allow for initial transport by rail, or water. Arrangements for road transport were made by the contractors with material taken to either one of the two Crossrail transfer sites, or directly to one of the alternative disposal sites identified by Crossrail, or a new site identified by the contractor and accepted by Crossrail.
Loads arriving at the DTS were inspected before they were accepted. If contamination was suspected, or the material deemed unsuitable for Wallasea Island, then it was tipped in a holding area whilst further investigations took place. Ultimately, any rejected loads were removed at the expense of the contractor that brought the material to the DTS.
Some loads arrived at DTS containing non compliant material such as general site waste (e.g. rebar, personal protective equipment gloves). Often this was from the station worksites where space was limited to store waste and sort it before sending it off-site. In general the tunnelling material did not suffer from this issue as the material came straight out from the tunnel boring machines via a conveyor and was loaded straight onto trains (sometimes lorries) with limited opportunity for any mixing with other waste. The process for rejected loads was determined at an early stage and communicated to contractors which helped to ensure it was clear as to who had to pay for the removal and the point of transfer of waste at the transfer site.
Operating Transfer Sites and Wallasea – Waste Acceptance
The Wallasea environmental permit required the production of a Waste Acceptance Procedure (WAP) which due to the relative timing of the permit and tunnelling procurement programmes was not developed in time to be included in the contracts and had to be provided to contractors subsequently.
The WAP document helped contractors understand the acceptance procedure agreed with the Environment Agency for all excavated material that was to be shipped to Wallasea and consisted of three steps to identify and periodically check the main characteristics of the waste:
- Level 1: Basic characterisation. It was the Contractor’s responsibility to carry out and submit this characterisation and a Waste Information Form was provided as a checklist for this submission.
- Level 2: Compliance checking. As excavation of tunnels, stations, portals or shafts progressed contractors had to periodically check the waste to ensure that the properties had not changed.
- Level 3: On-site verification. Contractors had to undertake on-site verification during excavation and loading of material onto outbound lorries, trains or other transport. Also, the Wallasea Island contractor had to check each delivery at the DTS and at Wallasea Island to verify that it was the expected waste.
The WAP went through a number of revisions as various complexities were identified such as clarifications on tunnelling additives, testing regimes and further detail on naturally occurring Selenium and Sulphate in London Clay.
This last issue was unexpected when the Environment Agency directed that the known elevated levels of Selenium and Sulphate in London Clay which formed the majority of the excavated material meant that material could not be assumed to be inert and that testing was required before making a decision about disposal. The Landfill Directive allows for some derogation above the specified limits for inert waste, subject to appropriate risk assessment and variation of permits at inert landfills that would receive the material and provided a way forward to progress with taking excavated material to inert landfill sites.
Before any tunnelling material could be placed at Wallasea its ecotoxicity potential for the aquatic environment had to be assessed. CRL worked with the tunnelling contractors to ensure any additives and polymers were risk assessed and consented in sufficient time to prevent any delays. Polymers are used to facilitate the handling of material when being processed through the Tunnel Boring Machine and as the polymers are entrained within the material itself, there was a need to assess what impact, if any, they may have on the aquatic environment when placed at Wallasea Island.
The study into eco-toxicology was based on the Environment Agency methodology: The direct toxicity assessment of aqueous environmental samples used the marine copepod (Tisbe battagliai) lethality test (2007). In addition to the toxicity testing, as the polymer is thoroughly entrained within the material being excavated by the TBM (Thanet Sand or London Clay), leachate analysis was undertaken by each tunnelling contractor in order to ascertain the leaching potential of the polymer.Disposal Sites Identified by Contractors
In some circumstances, contractors identified their own disposal locations for the excavated material and the contractor needed to demonstrate ‘beneficial reuse’ for their chosen site. The contractor also needed to provide reporting for client visibility. The Environment Agency asked CRL, as a major project, to demonstrate it knew the fate of its material and expected a greater focus on duty of care. This would not have been possible without the reporting requirements built into the Works Information. Although there was a requirement in the Works Information for a contractor to notify the Project Manager of any disposal sites they were proposing sending the material to, this information was often accepted at project level and therefore not all options selected were to the benefit of the overall programme in terms of excavated material strategy and a more aligned approach could have been beneficial.
Use of Conveyors
Conveyors were used to transport excavated material at a number of sites, most notably in removing material from the western and eastern tunnel drives at Royal Oak Portal and Limmo, respectively. Conveyors were also used to load the ships at DTS and Northfleet. In each case these conveyors were all designed, constructed, operated and maintained by a single contractor who therefore held the risk should they not perform as required.
The conveyor at Wallasea Island, however, was designed and constructed by one contractor, but it was handed over to be operated and maintained by another. When the Wallasea conveyor failed to perform as intended the ownership of this risk was disputed, compromising resolution of the issue.
On 29 September 2012 a hopper on the conveyor at Royal Oak Portal collapsed leading to the conveyor having to stop moving the material. The solution was to load the excavated tunnelling material by excavator onto the trains to Northfleet until the conveyor hopper could be fixed which only took a short time.
Around November 2012 it was identified that the Wallasea conveyor was struggling to process some of the material being shipped to Wallasea. When the tunnelling material (mainly London Clay) was on the ship on the journey from Northfleet to Wallasea some of the material became more cohesive so on reaching Wallasea it would come out in large lumps, be dropped into the hopper but couldn’t be broken down. As a result the conveyor became blocked. The solution was to mix material from Northfleet (cohesive) with DTS material which was more granular and also to amend the mechanical parts of the conveyor to enable it to more easily process the material along the conveyor.
Whilst the Royal Oak portal hopper/conveyor issue was shortlived, the Wallasea conveyor issue meant that for a time no material could be shipped from Northfleet so it began to run out of stockpiling space. BFK had to review whether extra land was required for further stockpiling however this was not required in the end.
Shipping Excavated Material
Prior to procuring the main tunnelling contracts CRL had carried out extensive geotechnical testing to identify the nature of the ground that would be encountered. A large number of boreholes were sunk prior to procurement and the results were included in the contract (as the Geotechnical Baseline Report). Crossrail identified that ships with flat bottomed holds were suitable for the specification of material to be shipped to Wallasea and they were more available for the type of journey required. However, after the eastern running tunnels contractor (DSJV) directly encountered material on the drive between Limmo and Farringdon it was identified that the moisture content was above the safe shipping standard and thus could not be shipped to Wallasea. This then led to the material being removed both by barge to Goshems Farm and by lorry to Ingrebourne. Alternative arrangements for the removal and disposal of the excavated material had to be found whereby a combination of barges with v-shaped holds and lorries was used. Barges with v-shaped holds operate to a different specification than ships and hence could transport the higher moisture content excavated material safely. The barges transported the excavated material to Goshems Farm where it was used to support the creation of grazing pasture for livestock and some lorries transported material to Ingrebourne.
In the end it transpired that the geology that produced the problematic high moisture content excavated material was found all the way up to Stepney Green. Throughout this period further options were explored in an attempt to reduce the amount of excavated material that has to be removed by road. Attempts were made to source alternative specialist ships with v-bottomed holds that could transport the high moisture content excavated material, but unfortunately brokers were unable to source these at that point in time. The potential to modify the existing ships so that they can safely transport the high moisture content excavated material was explored. However, the earliest availability of modified existing ships was going to be at the end of August 2013, too late to be practicable. In the end the combination of barges and lorries turned out to be the only feasible option for removing the excavated material in accordance with the programme. Ships with v-shaped holds would have been able to transport the material to Wallasea safely however these were not available in enough time, and although barges with v-shaped holds were available these were not able to enter the North Sea to reach Wallasea.
The Contract
CRL awarded a number of contracts for enabling and main construction works which involved the excavation of material. The requirements for excavated material were incorporated into the contract (the Works Information) in two separate sections, the Environment and Logistics sections and the Geotechnical Baseline Report was also included for information. It was found later that information in each was not always consistent which on occasion led to contractual difficulties. Although the ground investigation data was included in the Geotechnical Baseline Report, CRL identified that it often was not provided to all relevant specialists, for example contaminated land specialists and waste specialists within both design teams and contractors, who could have used the information to carry out further interpretation of the data in order to classify material for suitable disposal and provide early recommendations for disposal sites.
The Works Information did not explicitly stipulate that contractors’ staff signing Waste Transfer Notes (WTN) should be competent and trained and as a result it was discovered early on that WTN were not being completed correctly and material unsuitable for Wallasea was being sent to DTS where the acceptance procedures picked this up. In addition, the competency requirements for the Waste Manager listed in the Works Information did not include waste planning which led to a number of other staff e.g. logistics managers making key decisions about the fate of material. This often led to disposal sites being chosen based on commercial decisions, or distance from the originating site and did not necessarily meet the beneficial reuse requirement. For future projects it is recommended that there is a clear allocation of responsibility between the waste manager, the environment manager and the logistics manager.
The term ‘beneficial reuse’ was included within the Works Information however CRL did not provide a deliverable as to what was expected to be provided by contractors to demonstrate beneficial reuse. This led to the CRL team having to complete the exercise to identify where material was sent by contractors and review environmental permits to confirm the beneficial reuse at that location. Ideally a requirement to provide the disposal site’s full environmental permit with details of the planned end restoration of the sites, as well as a letter from that site’s operating company confirming what the material being sent by the Contractor was being used for and where on the site it would be placed would have been useful. Examples of beneficial reuse were provided to contractors including but not limited to: engineering use such as capping a landfill site or creating cell linings with London Clay, creating a wildlife reserve or farmland, land raising, and recreational land creation e.g. a golf course.
On contract award, CRL required the construction contractors to produce an excavated material plan prior to the start of construction. The purpose of the plan was for the contractor to demonstrate how all of the legal and client requirements for excavated material would be met on the contract. In the Works Information, CRL required contractors to put in place robust processes for excavation and materials handling in order to discharge all legal and contractual requirements. These are detailed in Volume 2B Part 21.9 of the Crossrail Works Information which is available separately.
Tracking and Reporting Excavated Material Movement
CRL implemented a number of processes for assuring that contractors were meeting all legal and contractual requirements for excavated material. A proprietary software product, the Codegate system, was used to record the excavated material transported by lorries from worksites to the DTS. Each lorry journey was recorded on the Vehicle Management Planning System (VMPS) which was used to track all vehicle movements. The Codegate system was not advanced enough at the time of Crossrail works however a future project could consider using a product such as Codegate and linking into EDOC (Electronic Duty of Care) and any reporting tool as the electronic upload of Waste Transfer Notes (WTNs) would allow the client to have visibility and traceability of waste. On occasion, CRL found that paper copy WTNs had not been fully completed or incorrectly completed. As a result Crossrail ensured that anyone completing WTNs e.g. security guards/gatemen, were appropriately trained in completing WTNs and regular checks were carried out.
The excavated material from the western tunnel drives was transported to Northfleet by train. The excavated material was transferred together with a WTN and a train configuration sheet declaring its nature and volume. The material from Northfleet to other locations such as Wallasea was accompanied by a WTN a copy of which was returned by the contractor placing the material at Wallasea to the tunnelling contractor at Northfleet.
All contractors were required to use the Building Research Establishments (BRE) SMARTWaste tool to report on the volumes of excavated material waste removed from site each period along with the destination site for the material. The tool was extremely useful in order to measure the volume of excavated material and to ensure that CRL could report on percentage diverted from landfill as well as carry out assurance on the destination of the material. It also ensured that all the excavated material data was held on one database that the client team could access easily and was in a common format to ensure ease of reporting. As a client organisation, CRL needed visibility on the destination of excavated material so that assurance of requirements could be undertaken. CRL used BRE’s SMARTWaste system to collect data and a separate legacy paper has been written detailing this.
One unexpected difficulty encountered was that because the contract did not explicitly require the Waste Manager to enter information into SMARTWaste this task was often carried out by office administrators who were not trained to use the tool, or in the waste classification system. As a consequence errors were frequently encountered such as incorrect waste classification which in turn led to having to introduce a second layer of resource at the programme level to double check the waste data and have errors corrected by SMARTWaste and/or the contractor. CRL identified that contractor personnel reporting were not always aware of the difference between a waste haulier, a waste broker and a waste management contractor/disposal site which led to CRL having to double check data.
Another difficulty was that the tool allowed for a number of entries created by different contractors for the same site using a slightly different spelling, for example, Docklands Transfer Site or DTS or River Road which meant that the CRL client team had to complete a reconciliation exercise to identify sites in order to report accurately.
The tool also allowed different contactors to report their excavated material in either tonnes or m3 whereas it is recorded at weighbridges in tonnes so there needed to be conversions applied. Crossrail found that the SMARTWaste system did not always convert accurately enough given Crossrail knew the volumes excavated and then tonnages, so Crossrail were able to update the conversion factors to allow for more accurate reporting.
Summary
As a result of these issues the amount of excavated material that could be transported to Wallasea was reduced to just over 3 million tonnes and the final amounts transferred are illustrated in Figure 9, along with factors affecting material delivered to Wallasea in Figure 10.
Figure 9 – Waste Crossrail delivered to Wallasea (planned v actual) in tonnes
Figure 10 – Factors affecting material delivered to Wallasea
Conclusion
Throughout the timescales of the Crossrail project, the excavated material strategy evolved to address the various challenges that arose as discussed in this paper. Not all excavated material could be sent to Wallasea but the mitigations put in place meant that the tunnelling and construction programme was not compromised and 98% of excavated material was beneficially reused. Figure 11 highlights the ten sites that received the majority of Crossrail material. 80% per km tonne of excavated material was transported by rail or water.
In conclusion the solution adopted met the requirements set out at the start of the project with Wallasea contributing a significant proportion as it could take a large amount of material and allowed a certain volume to be secured, was flexible in terms of timescales and allowed the commitments of maximising rail and water transport, and beneficially reusing the material to be met.
Figure 11 – The final destinations of excavated material (Top 10 sites receiving the majority of Crossrail material)
-
Authors
Lorna Mellings BSc MSc CEnv MIEMA - Crossrail Ltd
Lorna is the Environmental Assurance Manager at Crossrail. She is responsible for programme wide environmental best practice through various fora such as the Environmental Managers Forum and she is responsible for the promotion of a positive environmental culture throughout Crossrail, through managing and developing the Green Line environmental engagement award scheme. Lorna also provides technical environmental advice to the business, specifically with regards to excavated material, contaminated land and ecology.
Lorna joined Crossrail in 2008 as a Principal Environmental Planner having previously worked for Carillion on a number of national building projects and the Government’s Aspire Defence Project.
Greg Limna BEng(Hons) CEng MICE - Crossrail Ltd
Greg Limna was Head of Logistics for the Crossrail Project, responsible for the projects logistics strategy.
Greg joined the project in 2003 to work on the Hybrid Bill submission. In the subsequent years he worked on the utility diversions, enabling works and excavated material, and was responsible for delivery of the projects vehicle movement and safety programme.
Greg started his engineering career in the water industry before joining the Channel Tunnel Rail Link (HS1) and now has 20 years experience of delivering railway infrastructure projects.