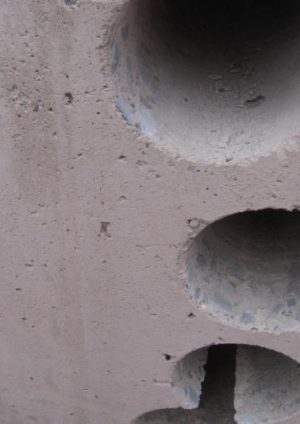
Low Carbon Concrete
Document
type: Micro-report
Author:
Mike de Silva BSc PhD FCIWEM MIEEM CSci C.WEM
Publication
Date: 14/03/2017
-
Abstract
Concrete production is responsible for signficant carbon emissions as a result of the conversion of calcium carbonate into calcium oxide, releasing carbon dioxide, and of the use of hydrocarbon derived fuels. Yet it is a vital constituent of our built environment. Whilst concrete remains invaluable and irreplaceable the carbon content of concrete can be reduced and a number of innovations are being investigated. Crossrail worked with the David Ball Group to investigate the viability of using its CemFree product for infrastructure. This report details the outcomes of the trials and describes the constraints imposed on the industry by the limitations of the current standards.
-
Read the full document
Introduction and Industry Context
Mega civil engineering projects like Crossrail inevitably consume vast quantities of concrete with consequent emissions of carbon dioxide as a by-product of the calcination of calcium carbonate to calcium oxide and also through the hydrocarbon derived fuels used by cement kilns. Many concrete specifications utilise cement replacements such as ground granulated blast furnace slag (ggbs) and pulverised fuel ash (pfa) as these make the concrete more resistant to sulphate and attack from other salts. High levels of cement replacement are therefore not unusual in aggressive ground conditions such as London Clay with its high sulphate content and also in marine environments. The presence of slags in concrete can also help to mitigate early age thermal cracking and as such provide more controllability of the curing process in hot climates.
If cement can be replaced in its entirety, then the carbon dioxide emission impacts of concrete can be reduced significantly. Furthermore, the concrete reinforcement can be redesigned, reducing the steel with further potential savings in both cost and carbon.
Crossrail trials
In recognising the potential benefits, Crossrail Ltd worked with David Ball Group who were in the process of obtaining a patent for alkali-activated cement utilising 95% ggbs and a proprietary activator. The challenge was to gain confidence in the product which would need to meet stringent performance criteria for a design life of 120 years. Ironically, the technology pre-dates the advent of ordinary Portland cements and many long standing examples can be found. However, the use of such materials is not currently supported by British or CEN standards.
Given the international priority to reduce atmospheric carbon emissions, every sector must play its part, so the recognition that low carbon concretes can reduce the construction sector’s contribution provided an important driver for Crossrail to investigate the potential to utilise this technology if practicable. As such Crossrail endeavoured to build confidence in low carbon concrete such that it could be adopted on the project, or if not, then on future projects. Crossrail sought to do this by working collaboratively with its supply chain to carry out trial tests of a low carbon concrete mix and using the results of the tests together with a review of its compliance with existing concrete standards to assess the potential for its use.
During the course of the investigation several issues were identified that prevented its use on Crossrail. Some of these issues were technical in nature, but the most significant barrier was the constraint placed by the lack of current standards to support the use of this technology. As a consequence Crossrail was unable to implement the use of this technology.
Lessons learned and Recommendations for Future Projects
Although Crossrail was unable to use low carbon concrete the results of this work will contribute to a growing body of knowledge that will hopefully support the eventual use of low carbon concrete on future projects. To that end the technical report of the work undertaken that was produced by Arup on behalf of Crossrail in September 2014 is included as part of this learning legacy. The report was produced with significant input from the David Ball Group, the developers of CemFree concrete, and the contractor Vinci. The Arup report is accompanied by an addendum provided by the David Ball Group which updates the findings of the report to the current level of knowledge on this subject as at November 2016.
One important recent development since the Crossrail investigation was undertaken has been the publication of PAS8820:2016, Alkali-activated cementitious material and concrete: Specification. The concrete produced using alkali-activated cementitious materials (AACM) can have performance benefits such as improved chemical and fire resistance and/or lower permeability to water and aggressive agents. However, these new AACM products are not fully covered in other British Standards for cement and concrete. PAS 8820 has been developed to fill this gap and encourage the use of AACMs in the construction industry.
To conclude, the trialling of CemFree on Crossrail, the subsequent work undertaken by the David Ball group and the publication of the PAS contribute significantly to building confidence in the use of this material in future infrastructure projects.
-
Document Links
-
Authors
Mike de Silva BSc PhD FCIWEM MIEEM CSci C.WEM - Bechtel
Sustainability Manager
Mike has over 25 years of environmental and sustainability design and construction experience much of which has been gained in the rail industry. He has worked on the two largest rail link projects in the United Kingdom, Crossrail and High Speed 1. Mike worked as Sustainability Manager on the Crossrail between 2009 and 2017 and was responsible for delivering its sustainability strategy and reporting as well as leading on CEEQUAL and BREEAM project management, and had an assurance role on the management & measurement of the project’s carbon footprint. He is currently working on HS2 Phase 2b.
He is well known in the industry and has published a number of works including the well reviewed Royal Institute of Chartered Surveyors publication “Sustainability & the Property Lifecycle”. He has also sat on a number of working groups including CEEQUAL International, BREEAM Infrastructure and BES6001 a voluntary standard on responsible sourcing of construction materials & products, and is currently on the editorial panel for the ICE Journal, Engineering Sustainability.