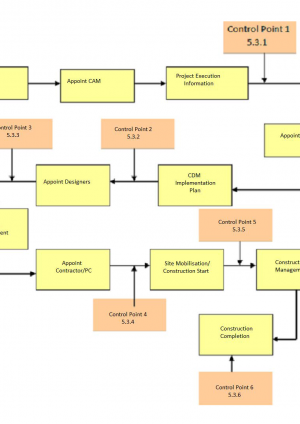
CDM 2015 – Multi-Site Arrangements
Document
type: Case Study
Author:
Mike Davies RIBA Tech IOSH IMaPS
Publication
Date: 14/03/2017
-
Abstract
The CDM challenge for the Crossrail project was to maintain a consistent approach to CDM compliance on more than 40 diverse projects. These were spread over a wide geographic area and consisted of challenging projects and work sites varying from green field sites to tunnelling under central London to new build facilities. This case study will explain how Crossrail, as Client and Principal Designer, discharged its CDM duties through the use of a CDM Integrator; managing the defined activities undertaken by a wide range of Crossrail post holders, providing assurance that compliance with CDM was maintained. This was all undertaken in–house by competent resources, using defined processes and procedures that were managed by Project Managers and Health and Safety Advisors with guidance from the CDM Integrator. These all worked closely with Principal Contractors, who integrated the Crossrail process and procedure into their own management systems. Consistent verification of compliance with the CDM procedures and processes assisted in ensuring compliance with the CDM duties and was aided by constructive feedback and suggestions from the Designers and Principal Contractors as to how to improve and develop the processes. This case study will be of use to Clients and Principal Designers on similar multi site construction projects wanting to ensure legal compliance with their CDM duties define expectations, and the means by which they are defined, managed, monitored and shared.
-
Read the full document
Introduction
The CDM challenge for the Crossrail project was to maintain a consistent approach to CDM compliance on more than 40 diverse projects over a wide geographic area consisting of challenging projects and work sites varying from green field sites, tunnelling under central London to new build facilities. Crossrail needed to ensure a uniformly high standard of Principal Designer (previously the CDM-Co-ordinator) service across all projects, and comply with the Client duties consistently and coherently.
As with most major construction projects, cooperation and coordination presented a risk to Crossrail, not just due to the size and complexity of the project, but also with its location mainly within central London. Additionally, there were many interfaces with other major infrastructure assets such as London Underground and Network Rail.
In order to facilitate the required legal compliance, management of CDM cooperation and coordination, plus resolve any possible conflicts or misunderstandings in CDM arrangements, a role was created within Crossrail – the CDM Integrator (CDMI), based on a successful similar approach used by the Olympic Delivery Authority (ODA).
Development of the Crossrail Model
The Olympic Delivery Authority (ODA) Approach
The ODA was the public sector body responsible for the delivery of the London 2012 Olympic venues and infrastructure. It appointed a delivery partner, CLM (comprising construction company Laing O’Rourke, Project Management specialist Mace and engineering and consulting firm CH2M Hill), to project manage the venues and infrastructure programme.
Despite CLM’s constituent parts, the ODA as Client, decided that it did not have sufficient resources to carry out the full duty of the then CDM – C (CDM Coordinator under the CDM Reg2007 – now replaced /enhanced with the Principal Designer role under CDM 2015) . The ODA decided to procure CDM Coordination services through its multiple suppliers – often design and build (D and B) contractors.
CDM-Cs reported directly to their ODA project sponsor, (individual officers within the ODA , who were responsible for projects as CDM Clients).The challenge for the ODA was to manage a large diverse grouping of 38 CDM – C service providers divided among many procurement packages including 10 venues, 16 utility, eight road /bridges. To manage this CLM proposed the role of a ‘CDM Integrator’ to work with the ODA to assist with this process.
Crossrail’s CDM Approach
Crossrail developed this idea of a single CDM Integrator, to suit the specific challenges of a multi site complex programme of over 40 diverse projects in a wide geographical area.
Crossrail decided that due to the technical complexity of the required structures, sensitivity of locations and desired high quality of design, it required greater control of design than that possibly achieved with D and B projects. Initially, it employed a team of eleven Framework Design Consultants, who developed designs to accurately reflect the clients detailed and specific requirements, but which allowed some scope for further detailed design by the Principal Contractors. This approach allowed the client a greater degree of design control, customisation of design elements, quality of specifications and also a more precise and detailed cost appreciation/awareness.
With the advent of CDM 2015[1] and the clear requirement of ensuring safe design solutions Crossrail decided that it would appoint itself as Principal Designer. This was to provide compliance, particularly at the crucial early stage of design and development. It also gave CRL greater ‘hands on’ control and guaranteed sufficient resources.
In total, CDM Coordinator services were provided in three different stages, as the project developed. Each individual stage may each be applicable for use on projects that are of differing scale and complexity.
1. Initially CRL had an in-house team of 14 CDM coordinators under a CDM Manager, each responsible for individual projects.
2. When Bechtel was then appointed Delivery Partner the role of CDM Coordinator was part of their service provision and the exiting CDM coordinator team was seconded into the Delivery Partner Team.
3. Further on in the programme, as the complexity and sensitivity of design elements developed, the role was taken back in-house. It was felt that in order to apply greater control and have influence over more sophisticated solutions CRL should appoint itself as CDM Coordinator, and then CDM Principal Designer under the CDM 2015 Regulations. This required a comprehensive retraining programme run by the CDMI so as to ensure adequate skills, knowledge and experience of the individuals. Training sessions run by the CDMI were attended in total by 500 persons, both CRL employees and Frame Work Designers and Contractors.
CDM Roles and Responsibilities
Crossrail Ltd was appointed as both Client and Principal Designer under the CDM Regulations 2015 (CDM). Crossrail discharged these duties through a range of defined responsibilities and activities undertaken by a number of post holders. This ‘distributed model’ is recorded in a CDM Responsibility Matrix, prepared by the CDM Integrator, which systematically allocates specific responsibilities (in line with each of the CDM regulations) to Crossrail post holders.
Line Managers were responsible for ensuring that their staff members were inducted into roles, including activities on the CDM Responsibility Matrix.
CDM Integrator role
In Crossrail the CDM integrator is a point of contact and source of professional advice and support. The CDM Integrator (CDMI), working as part of the Health and Safety Assurance team, provides oversight of the CDM management arrangements on the Crossrail programme and manages the processes that ensure that the programme remains CDM compliant. Ultimately the CDMI is responsible for providing assurance to Crossrail that compliance with CDM is being maintained. The CDMI role is detailed in the CDM responsibility matrix. Essentially, the CDMI principally fulfils the following duties:
- Ownership of CDM Processes and Procedures across the programme
- Assurance relative to CDM
- Advice and guidance at design review workshops
- CDM Training to Crossrail and Contractors
- Management of the F10 Notification Process
Other similar large scale complex projects consisting of diverse sites, spread over a large area, many with unique characteristics, and separate teams of designers are likely to have similar challenges that would benefit from having a similar role.
CDM Processes and Procedures
The following documents provide the overarching CDM framework for all projects:
Designing for Health and Safety Procedure
Health and Safety Standard for Contractors and Partners
Design for Health and Safety Guide for Designers
In order to ensure a consistent approach to the management of CDM, a CDM Procedure document, produced by the CDMI, was written to ensure compliance with corporate management of CDM. It was produced as a comprehensive guidance on the CDM management process and identifies individual role responsibilities for specific CDM actions so as to ensure legal compliance. This procedure describes the Control Points process used by Crossrail to provide assurance that all applicable CDM duties have been discharged.
As part of the programme, Crossrail made a commitment to excellence in Health and Safety. This commitment was defined in the Health and Safety Standard for Contractors and Partners document. Excellence in the application of good practice to CDM compliance is an important part of Crossrail’s health and safety commitments. This procedure applied to all Crossrail design and construction activities where Crossrail had a CDM duty, including where other organisations have been Elected as Client.
The following are management documents used by the CDMI to ensure clarity and consistency across the programme:
Periodic CDM Verification Activity Report
Monthly /periodic CDM Assurance questionnaires Template
Assurance
Control Points
The CDM Procedure mandates the use of Control Points, (critical stop/go points in the CDM process); these provide assurance that programme activities remain compliant with CDM requirements. There are 6 critical points:
- Control Point 1: Project Execution Information
- Control Point 2: CDM Implementation Plan
- Control Point 3: Appointment of Designer
- Control Point 4: Appointments of Contractors and Principal Contractors
- Control Point 5: Site Mobilisation and Start of Construction
- Control Point 6: Works Completion and Site Demobilisation
The passing through of each Control Point is be documented by the Project Manager using the Control Point Certificate . The certificate and the appropriate supporting evidence is prepared by the relevant Project Manager.[Note: Control points 3 and 4 can be combined where the Designer and the Principal Contractor are appointed at the same time.]
Figure 1 below graphically illustrates the relationship between project progression and the agreed Control Points.
Figure 1 – CDM Control Points
Control Point Management
The management of the Control Point process is delegated to CDM Assurance Managers (CAMs) through the completion of the Control Points. The control point criteria must be achieved before any work scope moves forward.
The Programme Director and Finance Director can delegate management of the process (through Control Point 1) to others. For the purposes of this procedure where a delegation is made, post holders are collectively known as CAMs and can include the:
- Area Delivery Director
- Operations Director
- Technical Director
- Land and Property Director
- Chief Engineer
The scope of the delegation is defined in the Project Execution Information document (see Control Point 1) and, where it is a normal part of the post’s responsibilities, be identified in the post job description. Figure 2 below shows the interfaces between the various posts.
Figure 2 – CDM Flow Diagram
The CAMS have overall responsibility for the control points and should ensure:
that a Project Manager is appointed to fulfil the responsibilities identified for the role. (Where no appointment is made, the CAM shall have the Project Manager responsibilities)
the competency of the teams
the effective development of the Project Execution Information (PEI)
that sign-off is properly completed and Control Point Certificates are prepared
sign-off of Health and Safety Executive (HSE) project notifications (F10) on behalf of Crossrail
that consultation takes place with the relevant Health and Safety Managers
that where an external Principal Designer appointment is required the appointment is made at the earliest stages of the project.
In conjunction with the Procurement Director the CAM should define the procurement plan and ensure that there is adequate definition of scope; that through the tender evaluation and, if relevant prequalification evaluation, only competent persons or organisations are appointed.
CDM Procedure
Assurance of compliance with the CDM Regulations and the Company’s arrangements is achieved through the application of the CDM procedure.
Each Crossrail project Health and Safety (H&S) Advisor, allocated to all projects, is required to submit a standard return summarising CDM related activities each period. The CDMI reviews these returns and carries out additional verification checks on site to ensure that returns are accurate. A clear picture is developed of levels of compliance; any areas of concern are quickly identified and addressed. Regular resulting periodic CDM verification activity reports are prepared, with concerns highlighted and communicated to senior Client representatives in order that these can be discussed and resolved at senior level meetings with the PCs.
Design Assurance
With the greater emphasis on safe design under the new CDM 2015 regulations [1], and Crossrail’s new role as Principal Designer responsible for ensuring that the designers fulfil their duties under CDM 2015, Crossrail had to update its relevant processes and procedures. The main document that covers the checking of the designers’ compliance is covered in the Crossrail Procedure – Designing for Health and Safety Procedure, which sets out the mechanism by which Crossrail undertakes its design responsibilities as Principal Designer duty holder under the CDM 2015 Regulations and the requirements for Designers.
Designers attend regular design review ‘workshops’ organised and managed by the Designers Lead Co-ordinator together with respective Designers present to review and collectively discuss and review design risk management proposals. Formal design reviews are undertaken at key Royal Institute of British Architects (RIBA) stages and/or ‘Gate Review’ milestones.
Crossrail Assurance Engineers, who have the appropriate skills, knowledge and experience, amongst other Crossrail representatives, attend such design review meetings and review the designers proposed designs and risk registers. The CDMI attends these meetings as required and provides guidance on suitable safety in the design process.
The CDMI also carries out additional regular checks on the designers proposals , which consist of issuing monthly /periodic CDM Assurance questionnaires to the Crossrail Health and Safety (H&S) Advisors on each project, which contains specific requests for information on how Designers are eliminating / reducing risks in their designs. Additional questions are included on the preparation of the Health and Safety File for each project. This includes production of the Designers Residual Risks from their Risk Registers .The responses are regularly validated by the CDMI visiting the H&S Advisors on site and reviewing the information available as evidence of the Designers elimination/reduction of risks.
The Crossrail H&S Advisors also attend regular Designers Risk/Design Review meetings with individual project designers on each of their sites and the CDMI will attend as required in order to ensure a consistent approach to cooperation and coordination and compliance with Crossrail obligations.
Training
Additionally, in order to ensure a consistent approach to cooperation and coordination and compliance with Crossrail’s obligations, the CDM Integrator carries out regular training sessions both internally to Crossrail staff and project site teams (both Crossrail and Principal Contractor (PC) team members). These sessions explain the Crossrail CDM Management Procedure and the Designing for Health and Safety procedure – including the requirements on Designers.
Further on-site training sessions are given by the CDMI on the production of the Heath and Safety Files to ensure that a consistent approach as set out the in the Crossrail H&S File Guidance document prepared by the CDMI.
F10 Health and Safety Executive (HSE) Notification Register
To ensure overall control of the F10 HSE Notification process the CDMI is responsible for the setting up, management and maintenance of the Crossrail Project F10 Register. This is continually updated to record changes to existing F10s and the issuing of new Notifications. Reports are issued regularly to Directors, Project Managers and Health and Safety Advisors which highlight F10s that are due for renewal, so that, if necessary they can be updated/renewed in a timely manner.
Lessons Learned
- On similar large scale complex programmes, consisting of many varied diverse projects, it is of benefit to have an easily accessible central source of CDM expertise advice and guidance in the form of a CDM Integrator. This provides consistency and robust professional guidance, so as to ensure that the clients CDM obligations are met and complied with.
- It is important that consistent and robust CDM management processes and procedures are in place and that they are communicated to all parties at prequalification stages through to construction and completion.
- Ensure all designers and Principal Contractors are suitably competent with adequate skills knowledge and experience and are adequately resourced for their projects by means of a detailed assessment procedure.
- Continually provide CDM training sessions delivered by the CDMI throughout the project to client and designer / PC teams so as to ensure all are clear as to what the procedures require.
- Assurance of the Designers and PCs compliance with the client’s CDM Management process and procedure is essential thorough the project via means of periodic CDM metrics returns followed up by regular on site verification meetings with the Client H&S Advisors and the PC representatives.
- Designing for Safety. It is important to have, at the early design development stages, client representatives at Design Review meetings that are adequately competent to meaningfully get involved with design discussions and decisions. If required they must be able to confidently challenge design proposals that appear not to reduce or control hazards adequately. This will obviate the need at later more detailed design stages to alter designs.
- Health and Safety File. Start early discussions with the End Users to agree content and format. This requirement should be clearly communicated to the Designers and PCs so that timely File information is developed throughout the project rather than leaving it to near the end when key knowledgeable and experienced site staff are leaving the project who could contribute to the File preparation.
Conclusion
By means of a single source of coordinating and managing the CDM compliance on large scale, complex multi-site developments, the CDMI role can ensure the required Client legal compliance. This can be achieved by robust guidance, encouragement and management of cooperation and communication and regular CDM compliance verification checks on designers and Principal Contractors.
Encouragement of innovative means of reducing risks and improving health and safety at the early design, and construction stages will assist in achieving this.
Other similar large scale complex projects, many with unique characteristics, and separate teams of designers are likely to have similar challenges, but can be satisfactorily, managed by similar means of a central coordinating managing, and guiding role – the CDM Integrator.
Recommendations for Future Projects
Designing for Safety
Innovative proposals made by designers should be encouraged if they improve Health and safety during construction.
Consider any innovative proposals from tendering PCs that could improve health and safety on site. At one new build station project a PC suggested the use of a temporary large scale Giant Gantry Crane for offloading the concrete precast elements from low loaders and locating the units into the structure – this reduced the need for mobile cranes and allowed greater accuracy in locating elements and reduced on site manual manoeuvring of very large concrete structural elements.
Competent Design Review Representation by Client
Have competent client representatives at design review meetings especially at early stages, who are able to contribute positively to design development and challenge inappropriate /unsafe design proposals with authority so to influence the designers to develop safer design solutions .Whilst encouraging innovative design the clients PD /representative must be in a position to challenge unsafe design proposals.
Corporate Guidance Documents
For consistency produce CDM guidance documents that aid safe design and construction that are applicable to all projects in the programme.
These could include guidance on designing for health and safety (such as Crossrails’s designing for Health and Safety Procedure) – setting out the mechanism by which the Client undertakes its design responsibilities as Principal Designer duty holder under the CDM 2015 Regulations and the requirements for Designers . Additionally related documents such as ‘Healthy by Design-a Guide for Crossrail Design Teams‘ could be produced which aids healthy design choices enabling designers to meet legal responsibilities, work in accordance with organisation policies and ethical codes conduct as required by bodies such as RIBA, ICE, etc.
Programme Wide Site Inductions
Project- wide inductions are recommended on all separate sites, for all planning to work on site, to provide an overall consistent message. This explains to the multiple sites the essential health & safety, environmental and quality responsibilities necessary to access sites in a safe and secure manner.
The project wide-inductions should be part of the comprehensive site induction process which includes the all important Principal Contractor’s induction which then incorporates site specific conditions and requirements , such as PC site rules ,site layouts ,welfare , effects on and relationships with neighbours, emergency /fire procedures , accident and incident reporting , briefings , and environmental issues. The combined induction presentations should provide a comprehensive presentation including graphics and videos and it would be beneficial to end with a test.
Site-specific briefings are also recommended to reinforce the messages for individual sites.
References
[1]The Construction (Design and Management) Regulations 2015, [online], available at
-
Document Links
-
Authors
Mike Davies RIBA Tech IOSH IMaPS - Crossrail Ltd
Mike Davies is the Crossrail CDM Integrator, and is ultimately responsible for providing assurance to Crossrail Ltd that compliance with Construction (Design and Management) Regulations (CDM) is being maintained.
Working as part of the Health and Safety Assurance team, he provides oversight of the CDM management arrangements on the Crossrail programme and manages the processes that ensure that the programme remains CDM compliant.
Mike started his career in large scale, design led, complex highly serviced developments for research and development companies including computer manufacturers, research companies and oil and gas companies. Clients included IBM, BA, and BP. He then moved to large scale city centre redevelopment projects for several major clients including Land Securities.
Mike joined Crossrail in 2008 as a CDM Coordinator, became CDM Manager andthen Health and Safety Advisor on several station, tunnel and portal projects.
-
Peer Reviewers
John Edwards, Group Safety,Health,Environment and Assurance Director, Kier Group PLC