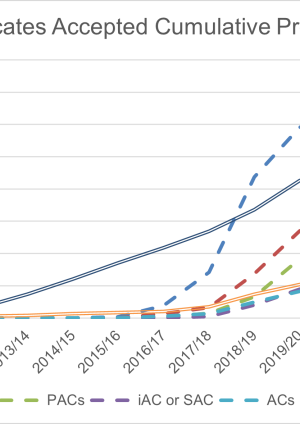
Managing Contractor Self-Certification on Crossrail
Document
type: Technical Paper
Author:
Judith Griffiths CQP MCQI
Publication
Date: 17/05/2023
-
Abstract
Based on processes and lessons from High Speed 1, the requirements for Self-Certification were written into Parts 13, 20 and 29 of the Works Information 2B and supplemented with procedures and templates specific to civils, fit-out, MEP and Routeway systems.
Each contractor was responsible for providing contemporaneous records to demonstrate their works complied with design, specifications, and statutory and regulatory requirements. Each contractor broke their scope of works into Certification Packages and upon the completion of the related physical works, they submitted an index of all associated documents, known as a Records Package Listing (RPL), and a Certificate to give the necessary assurance to Crossrail.
These 2 documents made a Certification Package and each one was tracked from planned through to acceptance and collectively accumulated in over 17,000 packages from 70+ contracts and 40+ contractors. This paper provides an insight into how this process was managed from 2010 to 2023.
-
Read the full document
Introduction
Writing Self-Certification into Parts 13, 20 and 29 of section 2B of the Works Information (WI) was key for setting out the requirements right from the top and from the beginning, and taking the information used on the High Speed 1 project provided a foundation from where to start. Each Contractor was liable for their works and fully responsible for the inspections and sign-off, except for sprayed concrete lining (SCL). Crossrail witnessed or observed the Contractor’s inspections to ensure compliance with the Inspection & Test Plans (ITPs) and that tests and inspections were carried out by competent persons.
As Crossrail was going to involve multiple contracts and contractors there was the potential to have a variance in processes to meet the requirements of the WI. Consistency was the priority, so a procedure was developed that set expectations and provided this as a supplement to the WI to avoid ambiguity. Elements of the original templates were combined to avoid unnecessary excess and the Construction Certificate and Records Package Listing became one document, rather than two. The civils procedure was amended over the duration of the project as we moved from the early civil works through to fit out of stations. A gap in the certification requirements of the Testing & Commissioning phases required in Part 28 of the WI was also recognised, which meant developing a process, procedure, and templates for mechanical, electrical, public health and routeway systems such as CCTV, High Voltage Power, etc. Although different in scope, the same principles were applied for providing certification packages, consisting of a T&C phase certificate and a records package listing, together with progressive assurance. Having procedures and templates set boundaries for all contractors to comply with and help to achieve the consistency a giga-project like Crossrail needed. The key certification procedures developed are included in the references section at the end of this document.
It was also key to recognise that the records package listing template established for the early works, in particular the tunnelling, was not going to include the same deliverable records as for fit-out of the stations, therefore these templates were revised accordingly. For the central section of the Elizabeth line, everything was progressively assured including piling, utilities, brickwork, steelwork, rail track, CCTV cameras, HV cables, so much more and even a kitchen sink. Crossrail consisted of two railways, a physical one and a digital one and because the records were produced alongside construction, the digital railway was ready for opening of the physical railway.
Breakdown Structures and Schedules
Each contract scope was different, and the contractors, together with their respective Crossrail Field Engineering (FE) Team, determined the best way to break down their works into certification packages. This formed a Certification Breakdown Structure. For civils and architectural fit out works, a traditional organogram style hierarchy was considered best practice to identify the Construction and Sub Construction levels, leading down from (and back up to) the Whole Contract Construction Certificate (WCCC). For MEP and Routeway they followed the Testing and Commissioning (T&C) phasing, so it was more appropriate to create logic diagrams or other formats as the interfacing of packages did not lend itself to a traditional hierarchy view. These T&C Certificates also sat underneath the WCCC for each contract.
The breakdown of the packages was reasonably fluid, allowing for changes to the physical works to influence the deliverance of progressive assurances. Packages were descoped, added, merged, or split and the breakdown structure was a ‘live’ plan of intent. Alongside the structure(s), the contractors created Certification Schedules. Each package was tied to an activity which then provided a planned submission date. These schedules were reviewed anywhere from monthly to daily depending on the phase of the works or the changes to the programme. For most of the construction works the schedule was stand-alone, but as the works moved into the completion stages, and particularly the T&C phases, each certificate was included in the construction programme and visible at a high level.
Further details and diagrammatic representations of certification hierarchy are shown in the following referenced documents: MEP and Systemwide Certification Process[2] and Construction Certification for Civil Engineering and Station Works Procedure[3]. An example of civil and architectural package breakdown for a typical station is also shown in the Learning Legacy technical paper The importance of planning in the production of Construction Deliverable Records.
KPIs
In the early days of the civil works there was limited aspiration to provide the assurance on-time which was partly due to behaviours and experiences on other construction projects at that time. This was causing delays for review and acceptance. Recognising there would be a high volume and with the determination to succeed in bringing assurance delivery as close to construction completion as possible, it needed to be a joint effort between the contractors and Crossrail. This led to the implementation of a specific Certification Key Performance Indicator (KPI) that involved both contractor and Crossrail to improve delivery performance and drive the behaviours needed. After a few trials in 2013 an on-time acceptance target was established for >90% of packages to be submitted, reviewed, and accepted at code 1 in the EDMS (eB), along with all deliverable records and closure of any NCRs, by a target date of planned submission date + 60 days. This target acceptance date was generated and monitored by the Crossrail Certification Team by keeping a master schedule with information gathered across all contracts.
Contractors had the opportunity to change their planned submission dates, providing it was programme related and agreed by the Supervisors Rep. Therefore, the target dates did move but boundaries were universally applied by the Certification Team. Initially the programme collectively achieved around 37% of ‘on-time’ certification package, far short of the target. The following year we achieved around the 79% and then the next few years we consistently achieved over 90%. Towards the back end of the project this KPI wasn’t providing the quick turnaround needed, 60 days was too long, and the construction schedules were changing at a pace that made the KPI redundant and less of a focus compared to achieving handover dates. However, the provision of providing progressive assurance deliverables and the certification processes were embedded into every day working practices. For something that was once considered an after-thought, it had now become part of the works.
The profile of the certification KPI was raised by including it within the Quality Performance Indicator (QPI). The QPI was the principal quality metric that was published each period in a league table format for each Tier 1 contractor. This provided visibility of performance across the programme and helped to incentivise the supply chain to improve through competition.
It was issued to a wide circulation of both client and contractor, Senior Management, Site, Engineering and Delivery teams. QPI measurements were developed to reflect performance in line with the changing phases of Crossrail (Construction through to Testing & Commissioning).
The QPI was made up of a number of key metrics including certification. During the main delivery phase 2 metrics were included (as below and in figure C1), these were:
- % certification completed on time
- Total overdue acceptance.
Figure 1 – Quality Performance Index – Certification completed and overdue
Certification performance in the QPI was developed in the latter stages of the programme to focus on the delivery of certification with a ‘countdown to zero’ metric. This was calculated from the number of certificates to go and the periods to completion to give a score for run rate. See details in figure 2.
Figure 2 – Quality Performance Index – Delivery of Certification metric
Training & Workshops
Achieving the KPI and embedding the process into the works was brought about by providing guidance on the process to the contractors and Crossrail FE Teams, which started back in the beginning in 2010, through 1-2-1 sessions. By 2013 group training sessions were fully established, gathering all parties who were involved in the process to explain the requirements and expectations, which ensured collective understanding and to demonstrate what the aim was going to be. These training sessions were held over the years as new contractors and Crossrail people came on board. Crossrail also supplemented the training with a Certification Working Group. A forum to share best practice, lessons learned and continuous improvement ideas. It was an open platform given to those involved to contribute to the holistic process and recognition was given to best performing contracts and most improved. Milestone achievements were awarded, and a league table initiated which encouraged some competitiveness in the earlier days. Proactively engaging with the teams helped to drive behaviours to meet the expectations and to recognise it was a monumental collaborative effort to assure the railway for opening.
Boundaries
Setting clear boundaries played an essential role in the process and thanks to the independence of the Certification Team they could be controlled, adhered to, and measured consistently across the whole programme. The acceptance criteria for Certification Packages included all deliverable documents on the records package listing (RPL) to be in eB, accepted, or closed, in the case of NCRs & RFIs. The Certification packages then had to be reviewed, signed, accepted, uploaded to eB, given an acceptance code 1 and the eB metadata closed. Each package was then verified for it to be counted as complete, which was most beneficial when packages were being issued in multiple numbers in the T&C phases particularly.
For the MEP and routeway T&C certification packages, Crossrail introduced an intermediary step of “signed”, which enabled the site teams to make the decision that the T&C tests had been carried out successfully, with results available, to assure it was ready for the next phase to begin and to sign the T&C certificate. The remaining steps of completing the package listing and any open deliverable documents would take the package to ‘completed’ status.
The boundary and definition of what “completed” meant was communicated throughout, but the lesson learned is to not presume everyone understands this and to address it from the top before interpretations arise.
Resources
It was a requirement for the contractors to have a dedicated resource for managing the certification process. As the T&C works started, it was common, and practical, to have teams split into civil & architectural fitout and MEP, with the MEP teams often supported by Tier 2 certification resources. In addition to the contractor resources, Crossrail Field Engineers and the Supervisor’s Representatives played a pivotal role in reviewing and accepting the deliverable documents and certification packages.
The Crossrail Certification Team were responsible for providing independent support to each contract team, by sharing lessons learned and best practices, actively monitoring performance, keeping focus on the package as whole, verifying the information was available in the EDMS and maintaining consistency for the process and reporting for the programme. Each Certification Engineer maintained a ‘master tracker’ for each of their assigned contracts, which enabled Crossrail to provide progress performance updates by contract and overall. This team were key to the consistency of the whole certification process.
By the end of 2015 the team resources had peaked at 14 who were deployed across all contracts in preparation of the build-up of construction activities and certification packages. But in March 2016 this was cut following budget constraints. The remaining 6 individuals continued to support every contract as the number of packages greatly increased. April 2017 to March 2020 saw the number of packages increase by over 600%, with the team expanding slightly in early 2019 as the T&C was in full production across all contracts. All the while every certification package continued to be monitored and verified. Figure 3 below represents the number of resources in the certification team and the volume of certification packages accepted. The number of resources from the contractors and the Crossrail Field Engineering Teams was not measured.
Figure 3 – Crossrail Certification team resources
Certification Packages
To demonstrate the works were built, installed, and tested in accordance with specifications, design, statutory and regulatory requirements, the contractors provided contemporaneous records at the start, during and end of the activities. These could include design, construction, and fabrication drawings, material compliance, inspection & test plans (ITPs), inspection records, test records, technical reports, change requests, NCRs, RFIs, red line drawings and as built drawings. Each record would be reviewed and accepted by the Crossrail FE Teams and kept in the Crossrail EDMS (eB). For the acceptance of certification packages, the criteria were set for all related records to be accepted ‘code 1’ or received for information ‘code 4’, and NCRs were to be closed. Documents that were at code 3 status, which was ‘rejected’ meant the package must not be accepted and the contractor had the responsibility to revise and resubmit. Any document at a code 2, accepted with comments, was upon the discretion of the PFE/Supervisor’s Rep.
All these related deliverables, together with their EDMS document number were listed on the Records Package Listing. The RPL was then reviewed for adequacy and verified that the records met the criteria given above. The Field Engineer, or first reviewer and the Supervisor’s Rep would sign a statement of acceptance, together with the appropriate level of Certificate which would also be signed by the Project Manager. These two templates would be given one document reference number and kept on the EDMS to be allocated towards the handover process.
Results
At the time of writing this paper, 17,283 certification packages (99.9%) had been produced and accepted since the first certificate in August 2010 for Royal Oak Portal demolition. Only two Whole Contract Construction Certificates (WCCCs) remain for the Signalling and Communications contracts. See figure 4 below. When the Elizabeth line opened in May 2022, 7 of 8 opened stations were fully assured, with Canary Wharf station finalising some back-of house details. When Bond Street station opened later in 2022, it was assured together with the routeway systems. Overall, the Crossrail certification process helped to lay the foundation for a successful handover of the new railway.
With 70+ contracts, 40+ contractors, spanning 13 years it was the Crossrail Certification team who maintained active monitoring of performance through to completion and it is from their master trackers that the following information is provided.
Of the total certification packages accepted shown in figure 5, 49% (total of 8496) were done between April 2018 and March 2020, peaking at an average of 79 and 85 packages accepted per week in those 2 years.
Figure 4 – Crossrail Certification cumulative performance
Figure 5 – Crossrail average weekly acceptance
Figure 6 – Crossrail performance by certificate – cumulative
Con C Construction Certificates (Civil & Architectural Fit out works) A certificate issued by the Contractor that certifies the completion of works for a major element e.g. Station – West Ticket Hall > Architectural Fit Out.
Sub C Sub Construction Certificates (Civil & Architectural Fit out works) A certificate issued by the Contractor that certifies the completion of works for a sub element (within the construction certificate) e.g. West Ticket Hall > Architectural Fit Out > Masonry and Blockwork (at a specific location or level).
AC Acceptance Certificates (MEP & Routeway Systems Testing & Commissioning phase 3) A certificate issued by the Contractor that formalises the end of Phase 3 when an Elementary System is completely tested along with its interfaces. For some systems the AC can be received at the end of phase 2.3 (if there is no integration testing required with 3rd parties)
iAC or SAC Interim Acceptance or Stage Acceptance Certificates (MEP & Routeway Systems Testing & Commissioning phase 3) A certificate produced by the Contractor where the AC is broken down for interim / stage acceptance. PAC Partial Acceptance Certificates (MEP & Routeway Systems Testing & Commissioning phase 2.3) A certificate issued by the Contractor that formalises the end of Phase 2.3 when a sub-system is completely tested as a stand-alone system with its interface simulated. PCC Pre Commissioning Certificates (MEP & Routeway Systems Testing & Commissioning phase 2.2) A certificate issued by the Contractor that formalises the end of Phase 2.2 when a Commissioning Lot is completely energised and tested. IRN Installation Release Notice (MEP & Routeway Systems Testing & Commissioning phase 2.1) The document issued by the Contractor certifying its installation and the end of Phase 2.1. Formalising the transfer of responsibility for part of a system (Commissioning Lots) from installation to commissioning.
Stations Certification
The following certification performance is from seven of the central section stations:
The first main station to kick-off the certification process was Paddington in February 2013, which was the longest running main station, taking 484 weeks from the first certificate to completion. After 407 weeks Farringdon was the first to achieve close-out in March 2021. Farringdon also had the least number of certification packages preferring to minimise the breakdown of the scope of works. For T&C works, despite much smaller numbers of certificates, the size of the scope of each package meant that Liverpool Street, with more than three times the numbers as Farringdon, finished in less time.
Woolwich had the shortest duration running at 320 weeks and was also the quickest to complete the civil and architectural fit out certification at 300 weeks. For T&C it was quite close in longevity between six of the stations, ranging from 201 weeks at Woolwich to 240 weeks at TCR. Bond Street was the last project to complete and had the largest volume of certification packages due to a combination of contracts. On average, these stations took 415 weeks from the first certificate acceptance to the last, at an average acceptance rate of 3 per week. In total these stations took 528 weeks to complete and an average acceptance rate of 18 per week.
Station Total (C & AFO) First (C & AFO)
Last (C & AFO)
Weeks (C & AFO) Total (T&C) First (T&C) Last (T&C) Weeks (T&C) Total (all) Close out Weeks (all) Av. p/w BOS 460 Jun-2014 Feb – 2023 414 1474 May-2017 Dec-2022 284 1948 Mar-2023 456 4.3 FAR 213 May-2013 Oct-2020 390 334 Oct-2016 Mar-2021 227 548 Mar-2021 407 1.3 LIS 383 Dec-2013 Dec-2021 418 1018 May-2017 Jun-2021 224 1402 Jan-2022 420 3.3 PAD 364 Feb-2013 Mar-2022 477 803 Dec-2017 Mar-2022 225 1410 May-2022 484 2.9 TCR 328 Jun-2016 Dec-2021 341 1133 Jan-2017 Aug-2021 240 1462 Mar-2022 353 4.1 WHI 393 Jul-2013 Mar-2022 452 989 Sep-2017 Mar-2022 235 1383 May-2022 463 3.0 WOO 187 Nov-2015 Aug-2021 300 619 Aug-2017 Jun-2021 201 807 Jan-2022 320 2.5 Routeway Certification
The following information is from the six main Systemwide contracts:
The Main Systemwide Contract C610 was the first to start the certification process for routeway contracts in August 2016 and High Voltage Power C650 was the first contract to achieve close-out in September 2022.
Assuming both signalling and communications complete by the end of May, C610 was the longest running routeway contract, from starting the first certificate to completion was 342 weeks and Platform Screen Doors C631 the shortest at 258 weeks.
For the main six routeway contracts it took 354 weeks, 2959 certification packages and an acceptance rate of 8 per week.
Routeway Total (civ) First (civ)
Last (civ)
Weeks (civ) Total (T&C) First (T&C) Last (T&C) Weeks (T&C) Total (all incl. WCCC) Close out Weeks (all) Av. p/w (T&C) C610 Main works
67 Aug-2017 Sep-2022 264 1274 Aug-2016 Jul-2022 311 1342 Mar-2023 342 4.6 C620* Signalling
214 Sep-2017 May-2023 288 214 May-2023 297 0.9 C631 PSDs
1 May-2021 May-2021 0 108 Nov-2017 Aug-2022 247 110 Oct-2022 258 0.9 C644 Traction Power
26 Nov-2016 Jun-2019 137 73 Jun-2017 Jan-2021 189 100 Dec-2022 319 0.5 C650 HV Power
306 Apr-2017 Aug-2020 174 307 Sep-2022 281 1.8 C660* Comms
885 Feb-2017 May-2023 317 886 May-2023 326 2.7 *At the time of writing, both the Signalling and Communications contracts had been closed out by the completion of an Interim ECP (see below section). Results are based on this.
Link to ECP
The close-out of all certification packages was verified as part of the Employers Completion Process (ECP). Once all ECP actions were complete the contractor submitted a Whole Contract Construction Certificate (WCCC) for acceptance which became the final certificate for each contract and ultimately sat at the top of their certification breakdown structure.
At the time of writing, the final works for C620 Signalling and C660 Communications and Control are to be handed over to Rail for London (RfL) for final completion. This transfer leaves only completion of the final 2 certificates, WCCCs for both C620 and C660.
In order for this to take place an ‘Interim ECP’ was completed for both contracts, C660 (12 May 23) and C620 (15 May 23) to complete all works and certification possible before handover.
The remaining scope of works and deliverables for both of these contracts was then transferred to TfL Capital Projects under RfLI direction.
After outstanding items are completed and the Post-Interim ECP (Full ECP) has been achieved, the Whole Contract Construction Certificate (WCCC) will be signed off after which those contracts will go into their Defects Periods.
Reporting & Dashboards
Figure 8 is a typical example of the certification dashboard reporting. Dashboards were issued initially on a period basis and from 2019 weekly.
Figure 8 – Certification performance dashboard
Figure 9 – Certification summary of all contracts to 9 May 2023
Lessons Learned
With reflection on the Crossrail certification process the following lessons learned should be considered:
- Ensure clear guidelines and expectations are set and maintained with well-defined criteria. Development of detailed but clear procedures that could be (relatively) easily followed and updated to reflect the advancing programme.
- Maintaining consistency was key to the success of the process. This was achieved with ‘1 to 1’ and ‘group’ training supplemented with a Certification Working Group, a forum to share best practice, lessons learned and continuous improvement ideas. It was an open platform given to those involved to contribute to the holistic process and recognition was given to best performing contracts and most improved.
- It was key to engage the Tier 1 contractors to improve and maintain performance. i.e. by:
- Rewarding milestone achievements.
- League table initiated which encouraged some competitiveness.
- Including certification metrics in reporting i.e. Certification dashboards and the QPI.
- Proactively engaging with the teams helped to drive behaviours to meet the expectations and to recognise it was a monumental collaborative effort to assure the railway for opening.
- Buy-in and support for the Certification process at the highest level to allow the profile of certification to be raised.
- Where an electronic system is used for storing document (such as eB, the Crossrail document management system), it is important to develop an effective and ‘user friendly’ interface and ensure that the system has provision for clearly defined reporting and data export functionality.
References
[1] CRL1-XRL-O4-GUI-CR001-50009 Rev 2.0 Certification Package Compilation Process
[2] CRL1-XRL-O8-GUI-CRG03-50001 Rev 3.0 MEP and Systemwide Certification Process
[3] CRL1-XRL-O4-GPD-CR001-50006 Rev 5.0 Construction Certification for Civil Engineering and Station Works Procedure
-
Document Links
-
Authors
Judith Griffiths CQP MCQI - Bechtel
Judith Griffiths was the Delivery Certification Manager on Crossrail and was responsible for managing the requirements for contractor self-certification across the central section.
Joining the project in 2010, Judith and the Certification Team monitored compliance and performance of each contract, from demolition and enabling works to commissioning of rail and station systems. Having overseen the production and acceptance of almost 17,000 certificates during her 12 years, and the completion and handover of all but one station, Judith left Crossrail following the opening of the Elizabeth line in 2022
Judith is a member of the Chartered Quality Institute and achieved Chartered Quality Professional status through completing the Crossrail CQI Quality Training course in 2013.
20 years of Judith’s 23-year career have involved self-certification and assurance records, for both contractor and client on major infrastructure projects in the UK.